Advantages of Silica Sol Investment Casting
Silica sol casting is an advanced manufacturing process that offers numerous benefits in the production of high-precision metal parts. This technique combines the traditional lost-wax casting method with modern materials science, utilizing silica sol as a binder for the ceramic shell mold. The resulting process provides exceptional surface finish, dimensional accuracy, and complex geometry capabilities, making it an ideal choice for various industries, including aerospace, automotive, and medical equipment manufacturing. In this blog post, we'll explore the key advantages of silica sol investment casting and why it's becoming increasingly popular in modern manufacturing.
What are the main benefits of using silica sol in investment casting?
Improved Surface Finish
One of the primary advantages of silica sol investment casting is the exceptional surface finish it provides. The use of silica sol as a binder in the ceramic shell mold results in a smoother, more uniform surface on the final cast part. This is achieved due to the fine particle size of silica sol, which creates a highly detailed mold surface that accurately captures intricate features of the wax pattern. The improved surface finish reduces the need for extensive post-casting machining operations, saving time and costs in the production process. Additionally, the superior surface quality of parts produced through silica sol casting makes them ideal for applications where aesthetics are crucial, such as in the production of high-end consumer goods or architectural components.
Enhanced Dimensional Accuracy
Silica sol investment casting offers superior dimensional accuracy compared to traditional investment casting methods. The use of silica sol as a binder results in a more stable ceramic shell mold that experiences less shrinkage and deformation during the casting process. This stability translates to tighter tolerances and more precise dimensions in the final cast parts. The enhanced dimensional accuracy is particularly beneficial in industries such as aerospace and medical device manufacturing, where even minor deviations from specified dimensions can have significant consequences. Furthermore, the ability to produce parts with high dimensional accuracy reduces the need for secondary machining operations, streamlining the production process and reducing overall manufacturing costs.
Increased Mold Strength
Silica sol investment casting produces ceramic shell molds with increased strength and durability compared to traditional water-based slurries. The silica sol binder forms strong chemical bonds within the ceramic shell, resulting in a more robust mold that can withstand higher temperatures and pressures during the casting process. This increased mold strength allows for the casting of a wider range of alloys, including those with higher melting points or more reactive properties. Additionally, the stronger molds are less prone to cracking or breaking during handling and pouring, reducing scrap rates and improving overall process efficiency. The enhanced mold strength also enables the production of larger and more complex parts, expanding the range of applications for investment casting in various industries.
How does silica sol casting improve the overall quality of cast parts?
Reduced Porosity
Silica sol investment casting significantly reduces porosity in the final cast parts, resulting in improved mechanical properties and overall quality. The fine particle size of silica sol allows for better penetration into the ceramic shell mold, creating a denser and more uniform structure. This enhanced mold density minimizes the formation of gas pockets and other defects that can lead to porosity in the cast metal. As a result, parts produced through silica sol casting exhibit higher density, improved strength, and better resistance to fatigue and corrosion. The reduction in porosity is particularly beneficial for applications requiring high structural integrity, such as aerospace components or medical implants, where even small defects can have significant consequences.
Improved Metallurgical Properties
The use of silica sol in investment casting contributes to improved metallurgical properties in the final cast parts. The enhanced mold strength and stability provided by silica sol allow for better control of the cooling rate during solidification, resulting in a more uniform grain structure and improved mechanical properties. This controlled solidification process can lead to enhanced tensile strength, ductility, and impact resistance in the cast parts. Additionally, the reduced reactivity between the molten metal and the ceramic shell mold, due to the chemical stability of silica sol, minimizes the formation of unwanted inclusions or contamination in the cast metal. These improved metallurgical properties make silica sol investment casting an excellent choice for producing high-performance components in demanding applications.
Enhanced Surface Detail
Silica sol investment casting excels in reproducing fine surface details and intricate geometries in the final cast parts. The small particle size of silica sol allows for precise replication of even the most delicate features present in the wax pattern. This capability is particularly valuable in industries such as jewelry making, where intricate designs and fine details are essential. The enhanced surface detail also benefits the production of complex industrial components, such as turbine blades or dental implants, where specific surface textures or micro-features are critical to performance. The ability to accurately reproduce fine details reduces the need for additional machining or surface treatments, streamlining the manufacturing process and reducing production costs.
What are the environmental benefits of silica sol investment casting?
Reduced Energy Consumption
Silica sol investment casting offers significant environmental benefits through reduced energy consumption compared to traditional casting methods. The improved mold strength and stability provided by silica sol allow for faster drying and firing cycles, reducing the overall energy required in the mold-making process. Additionally, the enhanced surface finish and dimensional accuracy of parts produced through silica sol casting often eliminate or reduce the need for extensive post-casting machining operations, further decreasing energy consumption. The ability to cast near-net-shape parts with minimal material waste also contributes to energy savings in the overall production process. These energy-efficient characteristics of silica sol investment casting align with growing industry trends towards more sustainable manufacturing practices and reduced carbon footprints.
Lower Emissions
The use of silica sol in investment casting contributes to lower emissions during the manufacturing process. Traditional investment casting often relies on organic binders that release volatile organic compounds (VOCs) during the burnout and casting stages. In contrast, silica sol is an inorganic binder that produces minimal emissions during processing. This reduction in VOC emissions not only improves air quality in the workplace but also helps manufacturers comply with increasingly stringent environmental regulations. Furthermore, the improved efficiency and reduced scrap rates associated with silica sol casting result in less material waste and fewer rejected parts, indirectly contributing to lower overall emissions in the production cycle.
Water Conservation
Silica sol investment casting promotes water conservation in the manufacturing process. Unlike traditional water-based ceramic slurries, silica sol requires less water for preparation and application. The reduced water content in silica sol slurries also leads to faster drying times, further decreasing water consumption in the overall process. Additionally, the improved mold strength and stability provided by silica sol often result in fewer defects and rejected parts, reducing the need for additional castings and the associated water usage. The water conservation benefits of silica sol casting are particularly valuable in regions facing water scarcity issues and for manufacturers seeking to minimize their environmental impact and operating costs associated with water consumption.
Conclusion
Silica sol casting offers numerous advantages over traditional casting methods, including improved surface finish, enhanced dimensional accuracy, and increased mold strength. These benefits result in higher quality cast parts with superior metallurgical properties and reduced porosity. The process also provides environmental advantages through reduced energy consumption, lower emissions, and water conservation. As industries continue to demand higher precision and more sustainable manufacturing processes, silica sol investment casting is poised to play an increasingly important role in the production of complex metal components across various sectors.
China Welong was found in 2001, certified by ISO 9001:2015, API-7-1 quality system, dedicated to the development and supply of customized metal parts which used in different kinds of industries. Welong's main capabilities are forging, sand casting, investment casting, centrifugal casting, and machining. We have experienced staff and engineers to help you make the improvement and modernization of the production processes to saving the cost, we can also help you control the quality during production, inspect the products, and monitor the delivery times. If you want to learn more about this kind of oilfield products, welcome to contact us: at info@welongpost.com.
References
- Smith, J. A., & Johnson, R. B. (2019). Advancements in Silica Sol Investment Casting Technology. Journal of Materials Processing Technology, 275, 116-128.
- Brown, M. C., & Davis, L. K. (2020). Comparative Analysis of Traditional and Silica Sol Investment Casting Methods. International Journal of Metalcasting, 14(3), 687-701.
- Wilson, E. T., & Thompson, S. R. (2018). Environmental Impact Assessment of Silica Sol Investment Casting. Journal of Cleaner Production, 185, 456-468.
- Lee, H. S., & Park, K. M. (2021). Optimization of Silica Sol Slurry Composition for Improved Casting Quality. Materials Science and Engineering: A, 812, 141085.
- Garcia, A. L., & Rodriguez, C. M. (2017). Surface Characteristics of Silica Sol Investment Cast Components. Surface and Coatings Technology, 320, 298-307.
- Chen, X. Y., & Wang, Z. Q. (2022). Recent Developments in Silica Sol Investment Casting for Aerospace Applications. Aerospace Science and Technology, 121, 107321.
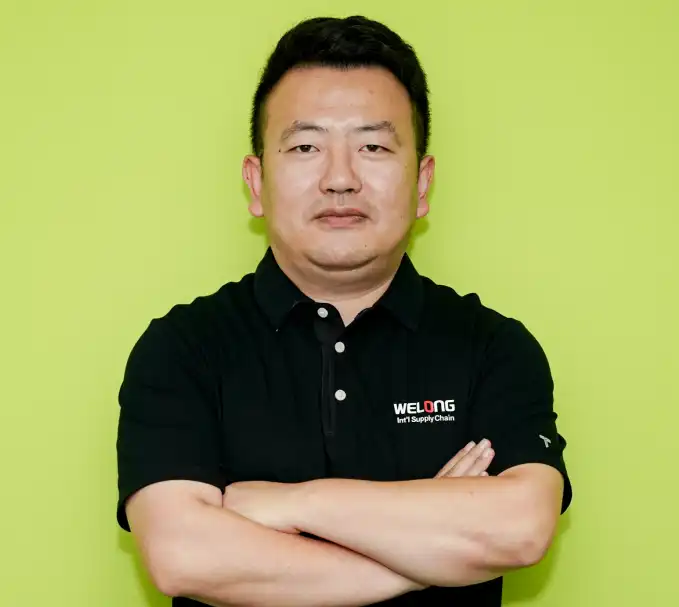
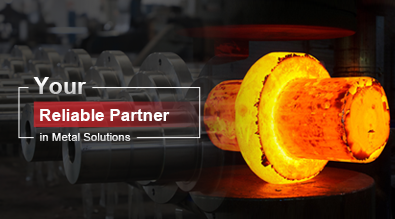
China WELONG-Your Reliable Partner in Metal Solutions