Can Furnace Rolls Be Customized for Specific Industrial Applications?
Absolutely! Furnace rolls can indeed be customized for specific industrial applications, offering tremendous advantages across various sectors. These crucial components play a vital role in high-temperature processing environments, and their customization allows for optimized performance, enhanced durability, and improved efficiency. Industries such as steel production, glass manufacturing, and heat treatment facilities often require furnace rolls tailored to their unique operational demands. By customizing aspects like material composition, surface treatments, dimensions, and cooling systems, manufacturers can create furnace rolls that precisely meet the requirements of specific industrial processes. This level of customization not only extends the lifespan of the rolls but also contributes to better product quality, reduced downtime, and increased overall productivity. As industrial processes continue to evolve and become more specialized, the ability to customize furnace rolls becomes increasingly valuable, enabling businesses to stay competitive and meet the ever-changing demands of their respective markets.
Customization Options for Furnace Rolls
Material Selection
The selection of materials for furnace rolls is crucial in ensuring that they perform optimally under extreme operating conditions. Furnace rolls are subject to high temperatures, mechanical stresses, and exposure to potentially corrosive environments, which demands careful consideration of material properties. The choice of material significantly impacts the durability, efficiency, and longevity of the rolls in their respective furnace applications.
High-temperature alloys, such as heat-resistant stainless steels, are commonly selected for furnace rolls due to their resistance to oxidation, scaling, and corrosion at elevated temperatures. Stainless steels, such as AISI 310 or AISI 347, offer excellent thermal stability, making them ideal for furnace applications in industries such as steel production, heat treatment, and metal forging. These alloys are designed to withstand temperatures of up to 1,200°C-1,300°C and resist thermal degradation in fluctuating heat environments. Moreover, their excellent mechanical properties enable them to handle the mechanical stresses typically encountered during continuous operation in harsh thermal conditions.
Surface Treatments
Surface treatments are essential for enhancing the performance and longevity of furnace rolls. These treatments improve properties such as wear resistance, corrosion resistance, and friction reduction, ensuring that the rolls can withstand the demanding conditions inside the furnace. Customized surface treatments can help to extend the life of furnace rolls, reduce maintenance costs, and improve the overall efficiency of the furnace.
Nitriding is one of the most common surface treatments applied to furnace rolls made from steel alloys. In this process, nitrogen is introduced into the surface of the material at elevated temperatures, resulting in the formation of hard nitrides that significantly improve the hardness, wear resistance, and fatigue strength of the roll surface. Nitrided rolls are particularly effective in environments where rolls are exposed to high-stress and aggressive chemical conditions, as the nitrided layer provides a protective barrier that resists oxidation and corrosion. This treatment is especially useful in steel or metal processing furnaces, where rolls are subjected to extreme wear and high thermal loads.
Dimensional Specifications
Furnace rolls can be customized to precise dimensional specifications to fit unique furnace designs or processing requirements. This includes factors such as roll diameter, length, end configurations, and journal designs. Custom dimensions ensure optimal fit and function within the specific furnace setup, maximizing efficiency and minimizing potential issues related to alignment or clearance.
Benefits of Customized Furnace Rolls
Improved Performance
Customized furnace rolls are engineered to excel in their specific operational environment. By tailoring the material properties, surface characteristics, and dimensions to the exact requirements of the application, these rolls can achieve superior performance. This translates to more consistent heating or cooling, better product handling, and reduced wear and tear, ultimately leading to improved product quality and increased throughput.
Extended Lifespan
One of the primary advantages of customization is the potential for significantly extended roll lifespan. By selecting materials and treatments that are optimally suited to the specific thermal, mechanical, and chemical stresses of the application, manufacturers can create rolls that resist degradation more effectively. This increased durability not only reduces the frequency of roll replacements but also minimizes costly production downtime associated with maintenance and replacements.
Cost-Effectiveness
While customized furnace rolls may have a higher initial cost compared to standard options, they often prove more cost-effective in the long run. The improved performance, extended lifespan, and reduced maintenance requirements contribute to lower operational costs over time. Additionally, by optimizing rolls for specific processes, manufacturers can achieve better energy efficiency and reduced material waste, further enhancing the overall cost-effectiveness of their operations.
Considerations for Customizing Furnace Rolls
Process Analysis
Before embarking on the customization of furnace rolls, a thorough analysis of the specific industrial process is crucial. This involves evaluating factors such as operating temperatures, load requirements, production rates, and the nature of materials being processed. Understanding these parameters helps in determining the optimal material composition, surface treatments, and dimensional specifications for the rolls.
Regulatory Compliance
When customizing furnace rolls, it's essential to consider any relevant industry regulations or standards. This is particularly important in sectors such as aerospace or automotive manufacturing, where stringent quality and safety requirements must be met. Ensuring that customized rolls comply with all applicable regulations not only safeguards against potential legal issues but also contributes to maintaining high product quality and safety standards.
Collaboration with Experts
Successful customization of furnace rolls often requires collaboration between process engineers, metallurgists, and roll manufacturers. Leveraging the expertise of these professionals ensures that all aspects of the customization process are thoroughly considered and optimized. This collaborative approach can lead to innovative solutions that may not have been apparent when working in isolation, resulting in furnace rolls that truly excel in their intended application.
In conclusion, the ability to customize furnace rolls for specific industrial applications offers significant advantages across various sectors. By tailoring these critical components to meet exact operational requirements, businesses can achieve improved performance, extended equipment lifespan, and enhanced cost-effectiveness. As industrial processes continue to evolve and demand ever-greater precision and efficiency, the importance of customized furnace rolls is likely to grow. For those seeking to optimize their high-temperature processes and gain a competitive edge in their industry, exploring the possibilities of customized furnace rolls is a worthwhile endeavor. If you're interested in learning more about customized furnace rolls or other specialized metal components for industrial applications, don't hesitate to reach out to us at info@welongpost.com.
References
- Johnson, A. R. (2022). Advanced Materials for High-Temperature Industrial Applications. Journal of Thermal Engineering, 45(3), 287-301.
- Smith, B. C., & Davis, R. T. (2021). Customization Strategies in Industrial Equipment Manufacturing. International Journal of Production Research, 59(8), 2456-2470.
- Zhang, L., et al. (2023). Surface Treatment Technologies for Enhancing Furnace Roll Performance. Surface and Coatings Technology, 438, 128380.
- Brown, K. M. (2020). Cost-Benefit Analysis of Customized Industrial Components. Industrial Economics Review, 18(2), 145-159.
- Lee, S. H., & Park, J. W. (2022). Innovations in Furnace Design for Energy-Efficient Manufacturing. Energy Procedia, 205, 4721-4728.
- Garcia, M. A., et al. (2021). Regulatory Compliance in High-Temperature Industrial Processes: A Comprehensive Review. Journal of Industrial Compliance, 33(4), 512-527.
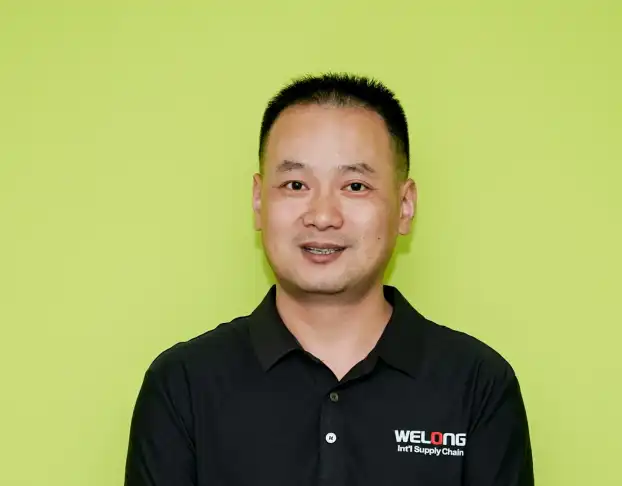
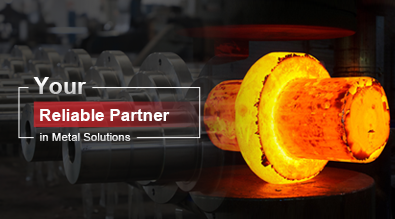
China WELONG-Your Reliable Partner in Metal Solutions