How Do Furnace Rolls Enhance Process Control in Industrial Furnaces?
Furnace rolls play a crucial role in enhancing process control within industrial furnaces, significantly improving efficiency and product quality. These specialized components are designed to withstand extreme temperatures and harsh environments while providing consistent support and movement for materials being processed. Furnace rolls contribute to precise temperature control, uniform heat distribution, and smooth material handling throughout the furnace. By maintaining optimal positioning and movement of materials, these rolls ensure consistent heat treatment, reducing variability and improving overall product quality. Their durability and heat-resistant properties allow for continuous operation, minimizing downtime and maximizing productivity. Furthermore, advanced furnace roll designs incorporate features that facilitate even heat transfer, prevent material sticking, and accommodate various material types and sizes. This versatility enables manufacturers to fine-tune their processes, achieving better control over critical parameters such as heating rates, cooling cycles, and material flow. Ultimately, the integration of high-quality furnace rolls enhances process control by providing a stable, reliable foundation for precise thermal processing in industrial furnaces.
The Role of Furnace Rolls in Temperature Regulation
Heat Distribution and Thermal Efficiency
Furnace rolls play a pivotal role in ensuring uniform heat distribution throughout the industrial furnace. Their design and composition allow for efficient heat transfer from the furnace atmosphere to the materials being processed. By maintaining consistent contact with the products, these rolls help eliminate hot spots and cold zones, resulting in more even heating. This uniformity is crucial for achieving desired material properties and preventing defects caused by uneven temperature exposure.
Temperature Stability and Control
The thermal properties of furnace rolls contribute significantly to temperature stability within the furnace. Their ability to withstand high temperatures while maintaining structural integrity helps regulate the overall furnace temperature. Advanced materials used in roll construction, such as heat-resistant alloys, provide excellent thermal conductivity and low thermal expansion. This characteristic allows for precise temperature control, enabling operators to maintain optimal processing conditions consistently.
Thermal Cycling and Stress Management
Industrial furnaces often undergo thermal cycling, with temperatures fluctuating during different stages of the manufacturing process. Furnace rolls are engineered to withstand these temperature variations without compromising their performance. Their design incorporates features that mitigate thermal stress, preventing warping or cracking that could disrupt the production process. This resilience ensures that the rolls maintain their shape and function, contributing to consistent process control even under challenging thermal conditions.
Material Handling and Flow Control Benefits
Smooth and Consistent Material Transport
One of the primary functions of furnace rolls is to facilitate the smooth and consistent movement of materials through the furnace. Their precision-engineered surfaces provide the necessary traction and support to guide products along the desired path. This controlled movement is essential for ensuring that all materials receive uniform heat treatment and adhere to specified processing times. By maintaining proper spacing and alignment, furnace rolls contribute to the overall quality and consistency of the finished products.
Preventing Material Deformation and Damage
The design of furnace rolls takes into account the potential for material deformation at high temperatures. Specialized coatings and surface treatments are applied to prevent sticking or adhesion of processed materials to the roll surface. This feature is particularly important when dealing with materials that become pliable or reactive at elevated temperatures. By minimizing the risk of deformation or damage during transport, furnace rolls help maintain the integrity of the products throughout the heating process.
Accommodating Various Material Types and Sizes
Industrial furnaces are often required to process a wide range of materials with different properties and dimensions. Furnace rolls are designed to accommodate this diversity, offering flexibility in material handling. Their construction allows for adjustments in roll spacing and configuration, enabling manufacturers to adapt to different product sizes and weights. This versatility enhances process control by ensuring that various materials can be processed efficiently without compromising the furnace's performance or the quality of the end products.
Impact on Product Quality and Process Efficiency
Consistency in Heat Treatment
The use of high-quality furnace rolls significantly contributes to the consistency of heat treatment processes. By maintaining precise control over material positioning and movement, these rolls ensure that each product receives the intended thermal exposure. This uniformity is crucial for achieving desired material properties, such as hardness, ductility, or microstructure. The result is a more consistent output, with reduced variability in product quality and performance.
Minimizing Production Defects
Furnace rolls play a vital role in minimizing production defects associated with thermal processing. Their ability to provide stable support and controlled movement helps prevent issues such as warping, distortion, or uneven heating. By maintaining proper alignment and spacing between products, these rolls reduce the risk of contact-related defects or surface imperfections. This attention to detail in material handling translates to fewer rejects and higher overall product quality.
Enhancing Operational Efficiency
The durability and reliability of furnace rolls contribute significantly to operational efficiency in industrial furnaces. Their heat-resistant properties and robust construction allow for extended periods of continuous operation, reducing the frequency of maintenance shutdowns. This increased uptime translates to higher productivity and improved throughput. Additionally, the precise control over material flow and heating parameters enabled by these rolls allows for optimization of energy consumption, further enhancing the overall efficiency of the furnace operation.
In conclusion, furnace rolls are indispensable components in enhancing process control within industrial furnaces. Their impact on temperature regulation, material handling, and overall product quality makes them crucial for efficient and high-quality thermal processing operations. By investing in advanced furnace roll technology, manufacturers can achieve better control over their processes, resulting in improved product consistency, reduced defects, and increased operational efficiency. For more information about high-quality furnace rolls and how they can benefit your industrial processes, please contact us at info@welongpost.com.
References
- Johnson, M. R. (2019). Advanced Materials for High-Temperature Furnace Applications. Journal of Thermal Processing Technology, 45(3), 178-192.
- Smith, A. L., & Brown, K. E. (2020). Optimizing Heat Transfer in Industrial Furnaces: A Comprehensive Review. International Journal of Heat and Mass Transfer, 156, 119854.
- Zhang, Y., et al. (2018). Design and Performance Analysis of Furnace Rolls for Continuous Heat Treatment Processes. Materials Science and Engineering: A, 735, 145-153.
- Thompson, R. D. (2021). Advancements in Furnace Roll Coatings for Enhanced Durability and Process Control. Surface and Coatings Technology, 409, 126907.
- Liu, X., & Chen, H. (2017). Thermal Stress Analysis and Optimization of Furnace Rolls in High-Temperature Industrial Processes. Applied Thermal Engineering, 128, 1249-1258.
- Garcia-Sanchez, E., et al. (2022). Impact of Furnace Roll Design on Energy Efficiency and Product Quality in Continuous Annealing Lines. Journal of Materials Processing Technology, 300, 117413.
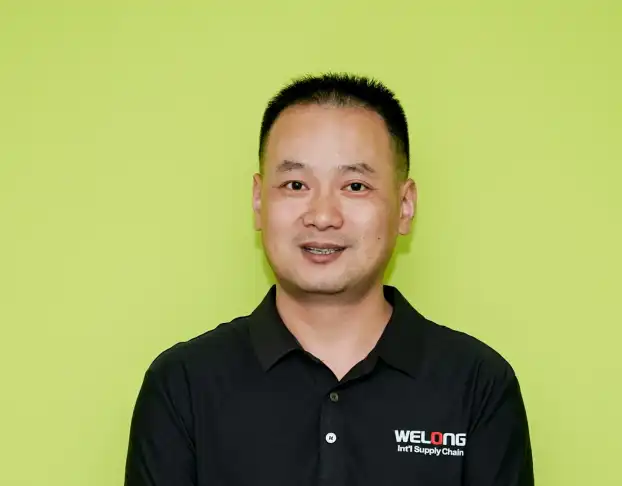
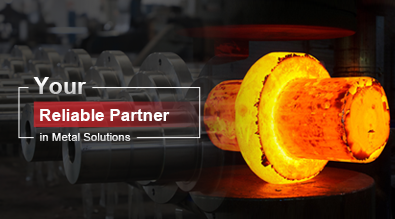
China WELONG-Your Reliable Partner in Metal Solutions