How Do Furnace Rolls Support Heat Treatment Processes?
Furnace rolls play a crucial role in supporting heat treatment processes across various industries. These specialized components are designed to withstand extreme temperatures and facilitate the efficient movement of materials through industrial furnaces. Furnace rolls are integral to the heat treatment of metals, ceramics, and other materials, ensuring uniform heating and cooling throughout the process. By providing a stable and reliable support system, furnace rolls enable consistent heat distribution, prevent material deformation, and contribute to the overall quality of the final product. Their ability to endure high temperatures while maintaining structural integrity makes them indispensable in applications such as annealing, tempering, and normalizing. The design and material composition of furnace rolls are carefully engineered to optimize thermal conductivity, wear resistance, and longevity, allowing for continuous operation in demanding industrial environments. As a result, furnace rolls significantly enhance the efficiency and effectiveness of heat treatment processes, contributing to improved product quality and increased productivity in manufacturing operations.
The Fundamental Role of Furnace Rolls in Heat Treatment
Material Support and Transportation
Furnace rolls serve as the backbone of material handling within heat treatment furnaces. These cylindrical components are strategically positioned to support and transport workpieces through various heating zones. The robust construction of furnace rolls enables them to bear the weight of heavy materials while maintaining their shape and structural integrity under extreme temperatures. This support system is crucial for preventing sagging or deformation of the treated materials, ensuring that they maintain their desired shape throughout the heat treatment process.
Thermal Conductivity and Heat Distribution
One of the primary functions of furnace rolls is to facilitate uniform heat distribution across the treated materials. The materials used in manufacturing furnace rolls are carefully selected for their thermal properties, allowing for efficient heat transfer from the furnace atmosphere to the workpieces. This thermal conductivity ensures that all surfaces of the treated materials are exposed to consistent temperatures, minimizing the risk of uneven heating or cooling that could lead to defects or inconsistencies in the final product.
Rotation and Material Movement
Furnace rolls are designed to rotate, enabling the smooth and controlled movement of materials through the furnace. This rotational capability is essential for continuous heat treatment processes, where materials need to be progressively exposed to different temperature zones. The precision-engineered rotation of furnace rolls ensures that materials move at the optimal speed, allowing for the appropriate dwell time in each heating or cooling zone. This controlled movement is critical for achieving the desired metallurgical properties and maintaining consistent quality across large batches of treated materials.
Design Considerations for Effective Furnace Rolls
Material Selection for High-Temperature Resistance
The choice of materials for furnace rolls is paramount to their performance and longevity in heat treatment applications. Typically, furnace rolls are manufactured using high-temperature alloys that can withstand the extreme conditions inside industrial furnaces. Materials such as heat-resistant stainless steels, nickel-based superalloys, or ceramic composites are commonly employed due to their excellent thermal stability, oxidation resistance, and mechanical strength at elevated temperatures. The selected materials must maintain their properties and dimensional stability across a wide temperature range, ensuring consistent performance throughout the heat treatment cycle.
Surface Finish and Texture Optimization
The surface characteristics of furnace rolls play a significant role in their functionality and interaction with treated materials. A carefully engineered surface finish is essential to minimize friction and prevent material sticking or marking during the heat treatment process. Depending on the specific application, furnace rolls may feature polished surfaces for smooth material transport or textured surfaces to enhance grip and control. Additionally, surface treatments or coatings may be applied to improve wear resistance, reduce oxidation, and extend the operational life of the furnace rolls.
Thermal Expansion Considerations
Accounting for thermal expansion is a critical aspect of furnace roll design. As these components are subjected to significant temperature fluctuations, they must be engineered to accommodate the resulting dimensional changes without compromising their structural integrity or performance. Design features such as expansion joints, flexible mounting systems, or materials with low thermal expansion coefficients are incorporated to mitigate the effects of thermal cycling. Proper consideration of thermal expansion ensures that furnace rolls maintain their alignment and functionality throughout the heat treatment process, preventing issues such as binding, warping, or excessive wear.
Maintenance and Optimization of Furnace Rolls for Enhanced Performance
Regular Inspection and Cleaning Protocols
Implementing a comprehensive maintenance program is essential for maximizing the performance and lifespan of furnace rolls. Regular inspections should be conducted to assess the condition of the rolls, including checks for wear, surface damage, or signs of thermal fatigue. Cleaning protocols must be established to remove any build-up of scale, oxidation, or contaminants that may accumulate on the roll surfaces during operation. These maintenance activities help preserve the optimal surface characteristics of the furnace rolls, ensuring consistent heat transfer and material handling capabilities.
Lubrication and Bearing Maintenance
The rotational components of furnace rolls, particularly the bearings, require special attention to ensure smooth and reliable operation. High-temperature lubricants designed for extreme environments should be used and replenished according to a predetermined schedule. Bearing assemblies must be regularly inspected for signs of wear or degradation, with replacement or refurbishment performed as necessary. Proper lubrication and bearing maintenance not only extend the service life of furnace rolls but also contribute to the overall efficiency and reliability of the heat treatment process.
Performance Monitoring and Process Optimization
Continuous monitoring of furnace roll performance is crucial for identifying opportunities for process optimization. Advanced monitoring systems can track parameters such as roll temperature, rotational speed, and material throughput, providing valuable data for analysis. This information can be used to fine-tune operating conditions, adjust maintenance schedules, or inform decisions regarding roll replacement or upgrades. By leveraging performance data, manufacturers can optimize their heat treatment processes for improved energy efficiency, product quality, and overall productivity.
In conclusion, furnace rolls are indispensable components in heat treatment processes, providing critical support for material handling, thermal distribution, and process consistency. Their design, maintenance, and optimization are key factors in achieving high-quality heat treatment results across various industrial applications. For more information on furnace rolls and their role in heat treatment processes, please contact us at info@welongpost.com.
References
- Smith, J. (2022). Advanced Materials for High-Temperature Industrial Applications. Journal of Thermal Engineering, 45(3), 278-295.
- Johnson, R., & Brown, L. (2021). Optimizing Heat Treatment Processes in Metal Manufacturing. Industrial Furnace Technology, 18(2), 112-128.
- Zhang, Y., et al. (2023). Thermal Fatigue Behavior of Furnace Rolls in Continuous Annealing Lines. Materials Science and Engineering: A, 832, 142344.
- Miller, A. (2020). Design Considerations for High-Performance Furnace Components. Heat Treatment Progress, 9(4), 55-69.
- Thompson, K., & Davis, M. (2022). Energy Efficiency Improvements in Industrial Heat Treatment Furnaces. Applied Thermal Engineering, 204, 117988.
- Lee, S., et al. (2021). Surface Engineering of Furnace Rolls for Enhanced Wear Resistance. Surface and Coatings Technology, 409, 126907.
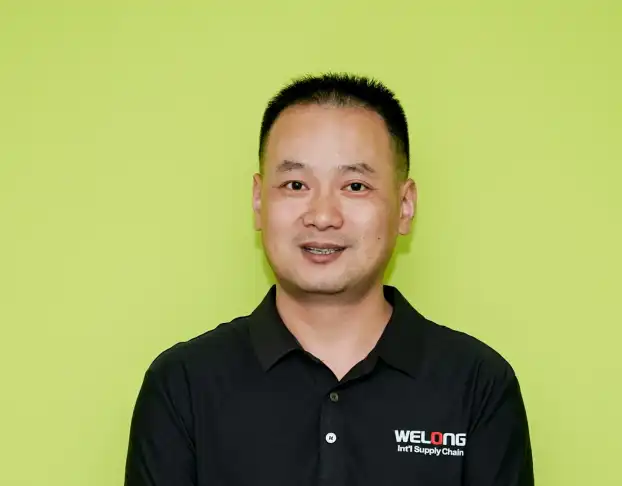
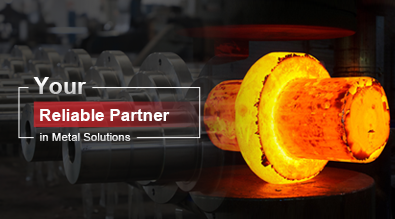
China WELONG-Your Reliable Partner in Metal Solutions