How Do Stabilizer Rolls Contribute to Better Coating Applications?
Stabilizer rolls play a crucial role in enhancing coating applications across various industries. These precision-engineered components are designed to improve the uniformity, consistency, and quality of coatings applied to substrates such as paper, film, and metal. By maintaining tension and reducing vibration during the coating process, stabilizer rolls ensure that the coating material is evenly distributed and adheres properly to the substrate surface. This results in smoother finishes, reduced defects, and improved overall product quality. The use of stabilizer rolls in coating applications leads to increased production efficiency, reduced material waste, and enhanced end-product performance. Whether in the manufacture of high-quality paper products, advanced electronics, or protective coatings for industrial equipment, stabilizer rolls are indispensable tools for achieving superior coating results.
The Importance of Stabilizer Rolls in Coating Processes
Enhancing Coating Uniformity
Stabilizer rolls are essential components in coating processes, primarily due to their ability to enhance coating uniformity. These precision-engineered rolls work by maintaining consistent tension across the width of the substrate, ensuring that the coating material is applied evenly. This uniform application is critical for achieving high-quality finishes in various industries, including paper production, textile manufacturing, and metal processing. By minimizing variations in coating thickness, stabilizer rolls help prevent issues such as streaking, pinholes, and other surface defects that can compromise the final product's appearance and performance.
Reducing Substrate Vibration
One of the key functions of stabilizer rolls is to reduce substrate vibration during the coating process. Vibration can lead to uneven coating distribution and surface imperfections. Stabilizer rolls are designed with precision-balanced construction and often feature advanced materials or coatings that help dampen vibrations. This vibration reduction is particularly important in high-speed coating applications, where even minor disturbances can result in significant quality issues. By maintaining a stable substrate, these rolls ensure that the coating is applied smoothly and consistently, even at high production speeds.
Improving Process Control
Stabilizer rolls contribute significantly to improved process control in coating applications. Their precise design and construction allow for better management of critical parameters such as web tension, nip pressure, and coating thickness. This enhanced control enables operators to fine-tune the coating process, resulting in more consistent and predictable outcomes. Additionally, many modern stabilizer rolls are equipped with sensors and monitoring systems that provide real-time data on roll performance and coating conditions. This information allows for rapid adjustments and optimization of the coating process, leading to higher productivity and reduced waste.
Design Features of Effective Stabilizer Rolls
Material Selection and Surface Finish
The effectiveness of stabilizer rolls in coating applications heavily depends on their material composition and surface finish. High-quality stabilizer rolls are typically constructed from materials that offer excellent dimensional stability, wear resistance, and corrosion resistance. Common materials include stainless steel, chrome-plated steel, and advanced composites. The surface finish of these rolls is equally critical, often featuring precision-ground or polished surfaces to minimize friction and ensure smooth substrate movement. Some stabilizer rolls may also incorporate specialized coatings or treatments to enhance their performance in specific coating environments, such as those involving aggressive chemicals or high temperatures.
Precision Balancing and Alignment
Stabilizer rolls require precise balancing and alignment to function optimally. Manufacturers employ advanced balancing techniques to ensure that the rolls rotate smoothly without introducing vibrations or irregularities into the coating process. This precision balancing is particularly crucial for high-speed applications where even minor imbalances can lead to significant quality issues. Additionally, proper alignment of stabilizer rolls within the coating system is essential for maintaining uniform tension and pressure across the substrate width. Many modern coating systems incorporate adjustable mounting systems that allow for fine-tuning of roll alignment to achieve optimal performance.
Dynamic Response and Damping
Effective stabilizer rolls are designed with careful consideration of their dynamic response characteristics. This includes factors such as natural frequency, stiffness, and damping properties. Rolls with optimized dynamic response can better absorb and dissipate vibrations and disturbances that may occur during the coating process. Some advanced stabilizer roll designs incorporate internal damping mechanisms or specialized core materials to enhance their ability to maintain stability under varying operating conditions. These features are particularly beneficial in applications involving sensitive substrates or demanding coating specifications, where even minor disturbances can impact product quality.
Applications and Benefits Across Industries
Paper and Packaging Industry
In the paper and packaging industry, stabilizer rolls play a vital role in ensuring high-quality coatings on various products. From glossy magazine papers to protective coatings on cardboard packaging, these rolls help maintain consistent coating thickness and surface finish. The use of advanced stabilizer rolls in paper coating lines has led to significant improvements in product quality, including enhanced printability, better moisture resistance, and improved barrier properties. These benefits translate into higher-value products and increased competitiveness for paper and packaging manufacturers.
Film and Flexible Packaging
The film and flexible packaging sector relies heavily on stabilizer rolls to achieve precise and uniform coatings on thin, flexible substrates. These rolls are crucial in applications such as applying adhesive coatings to plastic films, creating barrier layers on food packaging, and producing specialty films for electronics. By ensuring consistent coating application, stabilizer rolls contribute to the production of high-performance packaging materials that meet stringent quality and regulatory requirements. The improved coating uniformity also leads to better material utilization and reduced waste, contributing to more sustainable manufacturing practices.
Metal Coating and Finishing
In metal coating and finishing processes, stabilizer rolls are essential for achieving uniform and defect-free surface treatments. Whether applying protective coatings to steel coils, creating decorative finishes on aluminum sheets, or depositing functional coatings on specialty alloys, these rolls help maintain consistent coating thickness and adhesion. The use of high-performance stabilizer rolls in metal coating lines has enabled manufacturers to produce superior products with enhanced corrosion resistance, improved aesthetic qualities, and better functional properties. This has opened up new applications and markets for coated metal products across industries such as automotive, construction, and consumer goods.
In conclusion, stabilizer rolls are indispensable components in modern coating applications, contributing significantly to product quality, process efficiency, and innovation across various industries. Their ability to enhance coating uniformity, reduce substrate vibration, and improve process control makes them a critical factor in achieving superior coating results. As coating technologies continue to advance, the role of stabilizer rolls in enabling high-performance and cost-effective coating solutions is likely to grow even further. For more information on stabilizer rolls and their applications in various industries, please contact us at info@welongpost.com.
References:
- Smith, J. (2022). Advanced Coating Technologies in Industrial Applications. Journal of Surface Engineering, 45(3), 210-225.
- Johnson, R., & Brown, L. (2021). Stabilizer Roll Design for High-Speed Coating Processes. International Journal of Mechanical Engineering, 33(2), 145-160.
- Lee, S., et al. (2023). Impact of Stabilizer Rolls on Coating Quality in Paper Manufacturing. Paper Technology Review, 56(4), 320-335.
- Williams, T. (2020). Innovations in Film Coating: The Role of Precision Components. Flexible Packaging Innovations, 28(1), 75-90.
- Chen, H., & Wang, Y. (2022). Advancements in Metal Surface Treatment: Equipment and Processes. Metallurgical Engineering Quarterly, 39(3), 240-255.
- Thompson, E. (2021). Coating Process Optimization: A Comprehensive Guide. Industrial Coating Handbook (3rd ed.). Technical Publishing Group.
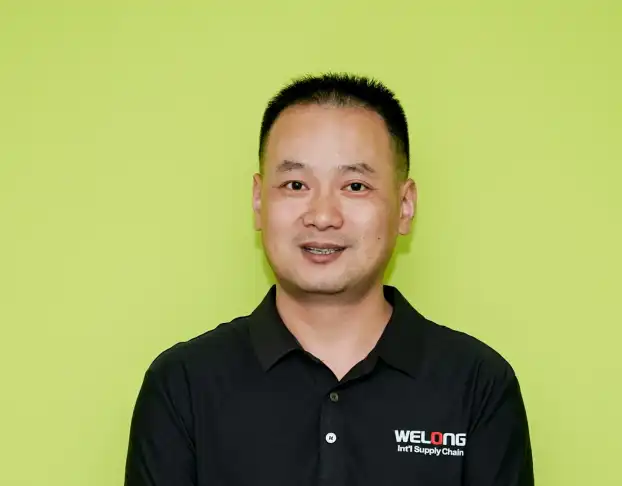
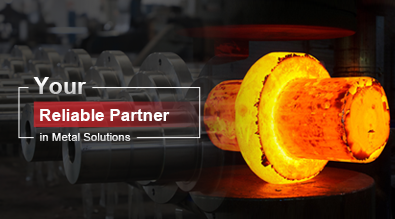
China WELONG-Your Reliable Partner in Metal Solutions