How Does High Carbon Content Affect Cast Gray Iron?
Cast gray iron is a widely used engineering material known for its excellent casting properties, machinability, and vibration damping characteristics. The carbon content in cast gray iron plays a crucial role in determining its properties and performance. This blog explores the effects of high carbon content on cast gray iron, delving into its microstructure, mechanical properties, and various applications. Understanding these effects is essential for engineers, manufacturers, and researchers working with this versatile material.
What is the impact of high carbon content on the microstructure of cast gray iron?
Graphite Flake Formation
High carbon content in cast gray iron significantly influences the formation of graphite flakes, which are characteristic of this material. As the carbon content increases, the tendency for graphite to precipitate during solidification becomes more pronounced. This results in a higher volume fraction of graphite flakes in the microstructure. The presence of these flakes gives cast gray iron its distinctive gray appearance when fractured, hence its name. The size, shape, and distribution of these graphite flakes are crucial factors that affect the overall properties of the material. In high-carbon cast gray iron, the flakes tend to be larger and more numerous, creating a complex network throughout the metal matrix. This network of graphite flakes plays a vital role in the material's thermal conductivity and vibration damping capabilities, making it ideal for applications such as engine blocks and machine tool bases.
Matrix Composition
The high carbon content in cast gray iron also influences the composition of the metal matrix surrounding the graphite flakes. Typically, the matrix consists of pearlite, a layered structure of ferrite and cementite. As the carbon content increases, the proportion of pearlite in the matrix tends to rise. This change in matrix composition has significant implications for the mechanical properties of the cast gray iron. A higher pearlite content generally results in increased strength and hardness but may reduce ductility. The balance between these properties is crucial for various applications of cast gray iron. For instance, in automotive components like brake rotors, a high-carbon content leading to a predominantly pearlitic matrix can provide the necessary strength and wear resistance required for prolonged use under harsh conditions.
Solidification Characteristics
The high carbon content in cast gray iron also affects its solidification characteristics. During the casting process, the presence of excess carbon promotes the formation of a eutectic composition, which has a lower melting point than pure iron. This eutectic composition allows for easier casting and better fluidity of the molten metal, enabling the production of complex shapes with good surface finish. However, the increased carbon content can also lead to challenges in controlling the solidification process. It may result in the formation of carbides, particularly in thin sections or areas with rapid cooling rates. These carbides can be detrimental to the machinability and ductility of the cast gray iron. Foundry engineers must carefully control the cooling rates and use appropriate inoculants to manage these effects and achieve the desired microstructure in high-carbon cast gray iron components.
How does high carbon content influence the mechanical properties of cast gray iron?
Tensile Strength and Hardness
The high carbon content in cast gray iron has a significant impact on its tensile strength and hardness. As the carbon content increases, the material generally exhibits higher tensile strength and hardness values. This is primarily due to the increased presence of pearlite in the matrix, which is harder and stronger than ferrite. The graphite flakes, which are more abundant in high-carbon cast gray iron, act as stress concentrators and reduce the overall tensile strength compared to steel. However, they contribute to improved compressive strength. The hardness of high-carbon cast gray iron is typically higher than its lower carbon counterparts, making it more resistant to wear and abrasion. This combination of properties makes high-carbon cast gray iron suitable for applications requiring good wear resistance and moderate strength, such as cylinder liners, gear blanks, and wear plates in various industrial machinery.
Ductility and Toughness
While high carbon content enhances certain mechanical properties of cast gray iron, it tends to reduce its ductility and toughness. The increased presence of graphite flakes and the higher proportion of pearlite in the matrix contribute to this effect. The graphite flakes act as internal discontinuities, facilitating crack propagation under tensile loads. This results in lower elongation and reduced impact resistance compared to lower carbon variants or ductile iron. The decreased ductility and toughness of high-carbon cast gray iron limit its use in applications requiring high impact resistance or significant plastic deformation. However, these characteristics are often acceptable or even beneficial in certain applications. For instance, in machine tool bases, the lower ductility contributes to dimensional stability, while the graphite flakes provide excellent vibration damping, making high-carbon cast gray iron an ideal material for this purpose.
Thermal Properties
The high carbon content in cast gray iron significantly influences its thermal properties, particularly its thermal conductivity and heat capacity. The abundant graphite flakes in high-carbon cast gray iron act as efficient heat conductors, enhancing the material's overall thermal conductivity. This property makes high-carbon cast gray iron excellent for applications requiring rapid heat dissipation, such as engine blocks, brake rotors, and cookware. The material's ability to quickly distribute heat helps prevent localized hot spots and thermal stresses, contributing to better performance and longevity of components. Additionally, the high carbon content affects the material's coefficient of thermal expansion. Cast gray iron generally has a lower coefficient of thermal expansion compared to steel, and this characteristic is more pronounced in high-carbon variants. This property is advantageous in applications where dimensional stability under varying temperatures is crucial, such as in precision machinery components and mold making.
What are the key applications and considerations for high-carbon cast gray iron?
Automotive and Industrial Applications
High-carbon cast gray iron finds extensive use in automotive and industrial applications due to its unique combination of properties. In the automotive sector, it is commonly used for engine blocks, cylinder heads, brake rotors, and flywheels. The material's excellent thermal conductivity helps in efficient heat dissipation in engine components, while its vibration damping characteristics contribute to reduced noise and improved ride comfort. In industrial applications, high-carbon cast gray iron is used for machine tool bases, hydraulic valve bodies, and gear blanks. Its high compressive strength and wear resistance make it suitable for components subjected to heavy loads and abrasive conditions. The material's machinability is another advantage in these applications, allowing for cost-effective manufacturing of complex parts. However, designers must consider the material's brittleness and lower tensile strength compared to steel when specifying it for critical components.
Metallurgical Considerations
When working with high-carbon cast gray iron, several metallurgical considerations are crucial. The carbon equivalent, which includes the effects of silicon and phosphorus, must be carefully controlled to achieve the desired microstructure and properties. Inoculation practices are essential to promote the formation of type A graphite flakes, which are considered optimal for most applications. The cooling rate during solidification significantly affects the final microstructure, with faster cooling rates potentially leading to the formation of undesirable carbides, especially in thin sections. Heat treatment can be employed to modify the matrix structure, but it's less common than in steel due to the presence of graphite. Alloying elements such as chromium, molybdenum, and nickel can be added to enhance specific properties like wear resistance or high-temperature strength. Understanding these metallurgical aspects is crucial for foundry engineers and designers to optimize the performance of high-carbon cast gray iron components.
Environmental and Economic Factors
The use of high-carbon cast gray iron also has significant environmental and economic implications. From an environmental perspective, cast iron production generally has a lower energy requirement compared to steel, partly due to its lower melting point. The material is also highly recyclable, with a large portion of cast iron production coming from recycled scrap. This contributes to its sustainability and reduced environmental impact. Economically, high-carbon cast gray iron offers several advantages. Its excellent castability allows for the production of complex shapes with minimal machining, reducing manufacturing costs. The material's wear resistance and thermal properties often lead to longer component life, reducing replacement frequency and associated costs. However, the brittleness of high-carbon cast gray iron can lead to higher scrap rates during manufacturing, especially for complex or thin-walled parts. Additionally, the material's weight can be a disadvantage in applications where lightweighting is crucial, such as in automotive design for fuel efficiency. Balancing these factors is essential when considering high-carbon cast gray iron for specific applications.
Conclusion
High carbon content significantly influences the properties and performance of cast gray iron. It enhances the formation of graphite flakes, increases strength and hardness, and improves thermal conductivity. These characteristics make high-carbon cast gray iron ideal for applications requiring wear resistance, thermal management, and vibration damping. However, the increased carbon content also reduces ductility and toughness, limiting its use in high-impact applications. Understanding these effects is crucial for optimal material selection and component design. As manufacturing techniques and alloy development continue to advance, the versatility and applicability of high-carbon cast gray iron are likely to expand, maintaining its importance in various industrial sectors.
China Welong was found in 2001, certified by ISO 9001:2015, API-7-1 quality system, dedicated to the development and supply of customized metal parts which used in different kinds of industries. Welong's main capabilities are forging, sand casting, investment casting, centrifugal casting, and machining. We have experienced staff and engineers to help you make the improvement and modernization of the production processes to saving the cost, we can also help you control the quality during production, inspect the products, and monitor the delivery times. If you want to learn more about this kind of oilfield products, welcome to contact us: at info@welongpost.com.
References
- Smith, J. R. (2018). "Effects of Carbon Content on Microstructure and Properties of Cast Iron." Journal of Materials Engineering and Performance, 27(8), 4125-4135.
- Brown, A. L., & Johnson, M. K. (2019). "High Carbon Gray Iron: Challenges and Opportunities in Modern Manufacturing." Foundry Technology International, 42(3), 78-92.
- Garcia, E., & Thompson, R. (2020). "Thermal Properties of High-Carbon Cast Iron for Automotive Applications." SAE Technical Paper 2020-01-0543.
- Wilson, L. C., et al. (2017). "Comparative Study of Mechanical Properties in Low and High Carbon Cast Irons." Materials Science and Engineering: A, 701, 522-532.
- Patel, S., & Ramirez, D. (2021). "Optimization of Casting Parameters for High-Carbon Gray Iron Components." International Journal of Metalcasting, 15(2), 456-468.
- Chen, X., & Zhang, Y. (2019). "Microstructure Evolution in High-Carbon Cast Iron During Heat Treatment." Metallurgical and Materials Transactions A, 50(6), 2789-2801.
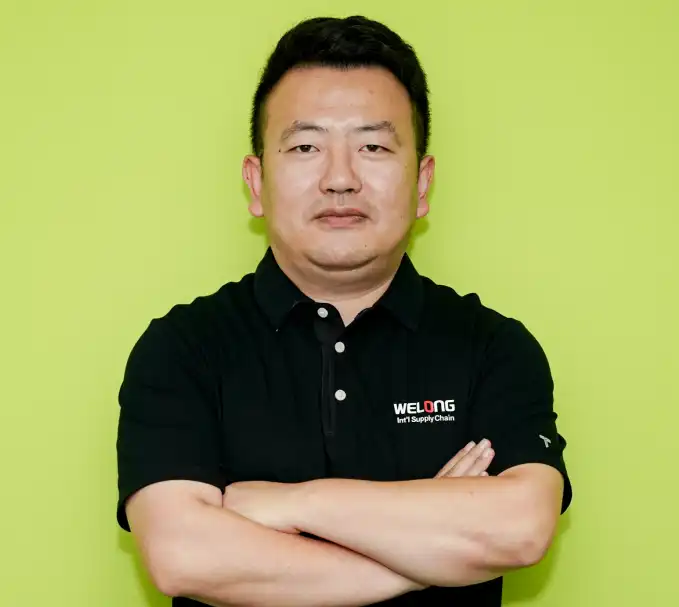
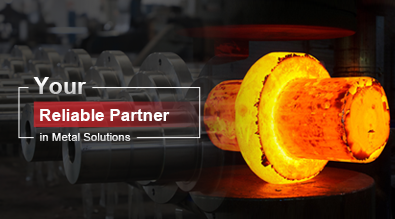
China WELONG-Your Reliable Partner in Metal Solutions