What are Casting Parts?
Casting parts is a fundamental manufacturing process that has been used for thousands of years to create complex metal components. This blog post delves into the world of casting, exploring its various techniques, applications, and advantages in modern manufacturing. We'll examine the intricacies of the casting process, discuss common challenges, and highlight the importance of quality control in producing high-performance parts.
What are the main types of casting processes used in manufacturing?
Sand Casting: The Versatile Workhorse
Sand casting is one of the most widely used casting processes in manufacturing. This versatile method involves creating a mold from sand and pouring molten metal into it to form the desired shape. Sand casting is particularly well-suited for producing large, complex parts with intricate details. The process begins by creating a pattern of the desired part, which is then used to form a cavity in the sand mold. Molten metal is poured into this cavity, allowed to cool and solidify, and then removed from the mold. Sand casting offers several advantages, including low tooling costs, the ability to cast a wide range of alloys, and the flexibility to produce both small and large parts. However, it may require additional machining to achieve tight tolerances and smooth surface finishes.
Investment Casting: Precision and Complexity
Investment casting, also known as lost-wax casting, is a process that excels in producing parts with exceptional detail and accuracy. This method begins by creating a wax pattern of the desired part, which is then coated with ceramic material to form a shell. The wax is melted and drained, leaving a precise cavity in the ceramic shell. Molten metal is then poured into this cavity, creating a highly accurate reproduction of the original pattern. Investment casting is particularly useful for producing complex geometries, thin-walled parts, and components with intricate internal features. It offers excellent surface finish and dimensional accuracy, making it ideal for aerospace, medical, and jewelry applications. However, investment casting can be more expensive and time-consuming than other methods, especially for large production runs.
Die Casting: High-Volume Production
Die casting is a high-speed, high-volume casting process that involves injecting molten metal into a reusable metal mold under high pressure. This method is particularly well-suited for producing large quantities of small to medium-sized parts with excellent dimensional accuracy and surface finish. Die casting offers several advantages, including rapid production rates, the ability to cast thin-walled parts, and excellent repeatability. The process begins by injecting molten metal into a steel mold cavity at high pressure, which quickly solidifies to form the part. Die casting is commonly used for automotive components, household appliances, and consumer electronics. However, it has limitations in terms of part size and material selection, as only metals with relatively low melting points can be used effectively in this process.
How does material selection affect the casting process and final product quality?
Alloy Composition and Properties
The choice of material plays a crucial role in the casting process and the quality of the final product. Different alloys have varying properties that affect their behavior during casting and the characteristics of the finished part. For example, aluminum alloys are popular in casting due to their low density, good corrosion resistance, and excellent castability. However, they may require special handling to prevent porosity and achieve optimal mechanical properties. Steel alloys, on the other hand, offer high strength and durability but can be more challenging to cast due to their higher melting points and tendency to form oxides. The alloy composition also influences factors such as fluidity, shrinkage, and solidification rate, which directly impact the casting process and final part quality. Careful consideration of material properties is essential to ensure that the chosen alloy meets the performance requirements of the casting parts while being compatible with the selected casting method.
Thermal Characteristics and Solidification
The thermal characteristics of the selected material significantly affect the casting process and the quality of the final product. Each alloy has unique melting and solidification behaviors that must be carefully managed during casting. For instance, some materials have a wide freezing range, which can lead to segregation and porosity if not properly controlled. Others may be prone to hot tearing or shrinkage defects during solidification. Understanding these thermal properties is crucial for designing appropriate gating and risering systems, determining optimal pouring temperatures, and managing cooling rates. Advanced simulation software can help predict how different materials will behave during the casting process, allowing engineers to optimize mold design and process parameters. By carefully considering the thermal characteristics of the chosen material, manufacturers can minimize defects and improve the overall quality of casting parts.
Surface Finish and Post-Processing Requirements
The material selection also impacts the surface finish of casting parts and any necessary post-processing steps. Some alloys naturally produce a smoother surface finish during casting, while others may require additional treatments to achieve the desired appearance or texture. For example, aluminum alloys often result in a good as-cast surface finish, whereas cast iron may require more extensive post-processing to achieve a smooth surface. The material's properties also influence the ease of machining, polishing, or applying surface treatments after casting. Some alloys may be more prone to work hardening during machining, while others may be difficult to weld or heat treat. Understanding these material-specific characteristics is essential for designing an efficient production process that minimizes post-casting operations while meeting the required specifications for the casting parts.
What are the common quality control measures used in casting parts production?
Non-Destructive Testing (NDT) Techniques
Non-destructive testing (NDT) plays a crucial role in ensuring the quality and integrity of casting parts without damaging the components. Various NDT techniques are employed throughout the production process to detect defects, verify dimensional accuracy, and assess material properties. One common method is radiographic testing, which uses X-rays or gamma rays to identify internal defects such as porosity, inclusions, or cracks. Ultrasonic testing is another valuable technique that uses high-frequency sound waves to detect flaws and measure material thickness. For surface defects, magnetic particle inspection and dye penetrant testing are effective in revealing cracks or other discontinuities. Additionally, eddy current testing can be used to detect surface and near-surface defects in electrically conductive materials. These NDT methods allow manufacturers to inspect casting parts thoroughly, ensuring that only high-quality components progress to the next stage of production or are delivered to customers.
Dimensional Inspection and Metrology
Accurate dimensional inspection is critical in the production of casting parts to ensure that components meet specified tolerances and fit requirements. Advanced metrology equipment, such as coordinate measuring machines (CMMs), laser scanners, and optical comparators, are used to verify the dimensions and geometries of cast parts. These tools allow for precise measurements of complex shapes and features, often comparing the actual part to the original CAD model. In addition to traditional contact measurement methods, non-contact techniques like 3D scanning are becoming increasingly popular for their ability to quickly capture detailed surface data. Statistical process control (SPC) is often employed to monitor dimensional trends and identify potential issues before they lead to out-of-specification parts. By implementing rigorous dimensional inspection procedures, manufacturers can ensure that casting parts consistently meet customer requirements and maintain high-quality standards throughout the production process.
Material Composition and Mechanical Testing
Ensuring the correct material composition and mechanical properties of casting parts is essential for their performance and reliability in service. Material composition is typically verified through spectrographic analysis, which can quickly determine the elemental makeup of the alloy. This helps confirm that the correct material was used and that no contamination occurred during the melting or pouring process. Mechanical testing is conducted to evaluate the physical properties of the cast parts, such as tensile strength, hardness, and impact resistance. Common tests include tensile testing, hardness testing (e.g., Brinell, Rockwell, or Vickers), and impact testing (e.g., Charpy or Izod). These tests often require the production of separate test specimens cast alongside the actual parts. In some cases, non-destructive methods like ultrasonic hardness testing can be used to assess mechanical properties without damaging the casting parts. By rigorously testing material composition and mechanical properties, manufacturers can ensure that casting parts meet the required specifications and perform reliably in their intended applications.
Conclusion
Casting parts production is a complex process that requires careful consideration of materials, techniques, and quality control measures. By understanding the various casting methods, material selection impacts, and quality assurance practices, manufacturers can produce high-quality components that meet stringent performance requirements. As technology advances, the casting industry continues to evolve, offering new opportunities for innovation and improvement in the production of casting parts.
China Welong was founded in 2001, certified by ISO 9001:2015, API-7-1 quality system, dedicated to the development and supply of customized metal parts used in different kinds of industries. Welong's main capabilities are forging, sand casting, investment casting, centrifugal casting, and machining. We have experienced staff and engineers who help you make the improvement and modernization of the production processes to save the cost, we can also help you control the quality during production, inspect the products, and monitor the delivery times. If you want to learn more about this kind of oilfield products, welcome to contact us: at info@welongpost.com.
References
- Campbell, J. (2015). Complete Casting Handbook: Metal Casting Processes, Metallurgy, Techniques and Design. Butterworth-Heinemann.
- Beeley, P. R. (2001). Foundry Technology. Butterworth-Heinemann.
- Sahoo, M., & Sahu, S. (2014). Principles of Metal Casting. McGraw-Hill Education.
- ASM International. (2008). ASM Handbook, Volume 15: Casting. ASM International.
- Brown, J. R. (1999). Foseco Ferrous Foundryman's Handbook. Butterworth-Heinemann.
- Heine, R. W., Loper, C. R., & Rosenthal, P. C. (2001). Principles of Metal Casting. McGraw-Hill.
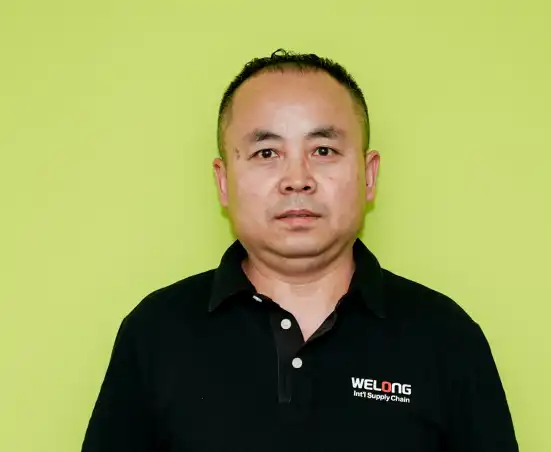
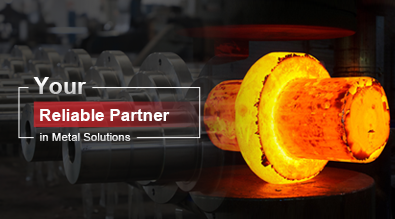
China WELONG-Your Reliable Partner in Metal Solutions