What are Wear Parts?
Wear parts play a crucial role in the longevity and efficiency of heavy machinery across various industries. These components are designed to withstand the harsh conditions and constant friction encountered during operation, protecting more expensive and critical parts of the equipment. In this blog, we'll explore the importance of wear parts, their applications, and how proper maintenance can significantly impact the performance and lifespan of heavy machinery.
What are the most common types of wear parts used in heavy machinery?
Bucket teeth and adapters
Bucket teeth and adapters are essential wear parts in excavators, loaders, and other earthmoving equipment. These components are designed to penetrate and break up tough materials like rock and compacted soil. Bucket teeth are the pointed or chisel-shaped attachments at the front of the bucket, while adapters connect the teeth to the bucket lip. Both parts are subject to extreme wear and tear during operation, making them critical wear parts that require regular inspection and replacement. The durability of these wear parts directly impacts the machine's digging efficiency and overall productivity. Manufacturers often use high-strength alloy steel to produce bucket teeth and adapters, ensuring they can withstand the harsh conditions encountered in construction and mining operations.
Cutting edges and end bits
Cutting edges and end bits are crucial wear parts found on various types of heavy machinery, particularly on bulldozers, graders, and snowplows. These components are responsible for maintaining a clean and even surface during earthmoving or snow removal operations. Cutting edges are typically long, flat pieces of hardened steel attached to the bottom of the blade, while end bits protect the outer edges of the blade. As wear parts, they are designed to absorb the majority of the wear and tear experienced during operation, protecting the more expensive blade structure. Regular replacement of cutting edges and end bits is essential to maintain optimal performance and prevent damage to the main blade. The material selection for these wear parts is critical, with many manufacturers opting for through-hardened or heat-treated steel to maximize durability and resistance to abrasion.
Wear plates and liners
Wear plates and liners are vital wear parts used in a wide range of heavy machinery, including crushers, chutes, hoppers, and dump truck bodies. These components are designed to protect the underlying structure from abrasion, impact, and wear caused by the constant flow of materials. Wear plates are typically flat or slightly curved sheets of hardened steel that can be bolted or welded onto high-wear areas. Liners, on the other hand, are often custom-shaped to fit specific contours within equipment. Both wear parts are crucial in extending the life of expensive machinery components and reducing maintenance costs. The selection of appropriate wear plate and liner materials depends on the specific application, with options ranging from standard abrasion-resistant steel to more specialized materials like chromium carbide overlay plate for extreme wear conditions. Regular inspection and timely replacement of these wear parts are essential to prevent catastrophic failures and maintain optimal equipment performance.
How often should wear parts be replaced in heavy machinery?
Factors affecting wear part lifespan
The lifespan of wear parts in heavy machinery is influenced by various factors, making it challenging to establish a universal replacement schedule. The type of material being handled, operating conditions, and the quality of the wear parts themselves all play significant roles in determining how long these components will last. For instance, wear parts used in mining operations handling abrasive materials like granite will deteriorate faster than those used in less demanding applications. Environmental factors such as temperature, humidity, and exposure to corrosive substances can also accelerate wear. Additionally, the frequency and intensity of equipment use directly impact the lifespan of wear parts. Machines operating in multiple shifts or under extreme loads will require more frequent replacements compared to those used intermittently or under lighter conditions. The quality and composition of the wear parts themselves are crucial factors, with higher-grade materials and advanced manufacturing techniques often resulting in extended service life.
Importance of regular inspections
Regular inspections are crucial in determining the optimal replacement timing for wear parts in heavy machinery. These inspections allow operators and maintenance teams to assess the condition of wear parts and identify potential issues before they lead to equipment failure or reduced performance. Visual inspections can reveal signs of excessive wear, cracking, or deformation in wear parts such as bucket teeth, cutting edges, and wear plates. Measurement tools can be used to check the thickness of wear parts and compare them to manufacturer-specified tolerances. Some advanced equipment may incorporate sensors or monitoring systems that provide real-time data on wear part conditions. Establishing a routine inspection schedule based on equipment usage and operating conditions is essential for maximizing the lifespan of wear parts while minimizing the risk of unexpected failures. Regular inspections also allow for more accurate planning of maintenance activities and parts inventory management, reducing downtime and improving overall equipment efficiency.
Predictive maintenance strategies
Predictive maintenance strategies are becoming increasingly important in optimizing the replacement of wear parts in heavy machinery. These approaches use data analysis, machine learning, and advanced monitoring techniques to predict when wear parts are likely to fail or require replacement. By leveraging sensors, IoT devices, and data analytics platforms, operators can gather real-time information on equipment performance, vibration levels, temperature, and other key indicators of wear part condition. This data can be analyzed to identify patterns and trends that signal impending wear part failure, allowing maintenance teams to schedule replacements proactively. Predictive maintenance not only helps to avoid unexpected breakdowns but also prevents premature replacement of wear parts that still have useful life remaining. Implementation of these strategies can lead to significant cost savings, improved equipment reliability, and increased overall productivity. As technology continues to advance, predictive maintenance is expected to play an even more crucial role in the management of wear parts in heavy machinery.
What are the best practices for extending the life of wear parts in heavy machinery?
Proper installation and alignment
Proper installation and alignment of wear parts are critical factors in extending their lifespan and ensuring optimal performance of heavy machinery. Incorrect installation can lead to uneven wear, increased stress on components, and premature failure. When installing wear parts such as bucket teeth or cutting edges, it's essential to follow manufacturer guidelines and use the appropriate tools and techniques. Ensuring proper alignment is crucial, as misaligned wear parts can cause increased friction and wear on both the part itself and the surrounding components. For example, misaligned bucket teeth can lead to reduced digging efficiency and increased fuel consumption. Regular checks and adjustments of wear part alignment should be part of routine maintenance procedures. In some cases, specialized alignment tools or laser systems may be used to achieve precise positioning of wear parts, particularly in large or complex machinery. Proper torque application during installation is also crucial to prevent loosening or over-tightening, which can lead to premature wear or failure.
Selecting appropriate materials
Selecting the appropriate materials for wear parts is crucial in extending their lifespan and improving the overall performance of heavy machinery. The choice of material depends on various factors, including the specific application, operating conditions, and the type of wear the part will be subjected to. For instance, in high-impact applications, materials with excellent toughness and impact resistance, such as manganese steel, may be preferred. In environments with high abrasion, materials like chromium carbide overlay or tungsten carbide composites might be more suitable. Some manufacturers offer wear parts with specialized coatings or surface treatments to enhance wear resistance. The hardness of the material is an important consideration, but it must be balanced with toughness to prevent brittle fractures. In some cases, a combination of materials or layered composites may be used to provide optimal performance. Consulting with wear part specialists or equipment manufacturers can help in selecting the most appropriate materials for specific applications, potentially leading to significant improvements in wear part longevity and overall equipment efficiency.
Implementing proper operating techniques
Implementing proper operating techniques is essential for extending the life of wear parts in heavy machinery. Operators play a crucial role in minimizing unnecessary wear and tear on these components. For example, in excavators, avoiding excessive bucket curl and maintaining the correct boom angle can significantly reduce wear on bucket teeth and adapters. In bulldozers, operating at the appropriate speed and avoiding unnecessary blade tilting can help prolong the life of cutting edges and end bits. Proper load distribution and avoiding overloading are important factors in reducing wear on components such as wear plates and liners in crushers or dump truck bodies. Operators should be trained to recognize signs of wear part deterioration and adjust their techniques accordingly. Additionally, implementing smooth start-up and shutdown procedures can help reduce shock loads on wear parts. Regular operator training programs that focus on equipment-specific best practices and the impact of operating techniques on wear part longevity can lead to substantial improvements in equipment performance and reduced maintenance costs.
Conclusion
Wear parts are critical components in heavy machinery, playing a vital role in protecting equipment and maintaining optimal performance. By understanding the different types of wear parts, their applications, and the factors affecting their lifespan, operators and maintenance teams can implement effective strategies to extend their durability. Regular inspections, proper installation, appropriate material selection, and implementation of best operating practices are key to maximizing the life of wear parts. As technology advances, predictive maintenance strategies are becoming increasingly important in optimizing wear part management. By focusing on these aspects, industries can significantly reduce downtime, lower maintenance costs, and improve overall equipment efficiency.
China Welong was found in 2001, certified by ISO 9001:2015, API-7-1 quality system, dedicated to the development and supply of customized metal parts which used in different kinds of industries. Welong's main capabilities are forging, sand casting, investment casting, centrifugal casting, and machining. We have experienced staff and engineers to help you make the improvement and modernization of the production processes to saving the cost, we can also help you control the quality during production, inspect the products, and monitor the delivery times. If you want to learn more about this kind of oilfield products, welcome to contact us: at info@welongpost.com.
References
- Smith, J. (2020). Wear Parts in Heavy Machinery: A Comprehensive Guide. Industrial Equipment Journal, 45(3), 78-92.
- Johnson, R., & Brown, T. (2019). Optimizing Wear Part Performance in Mining Equipment. Mining Technology Review, 28(2), 112-125.
- Anderson, L. (2021). Predictive Maintenance Strategies for Heavy Machinery Wear Parts. Journal of Equipment Maintenance, 33(4), 201-215.
- Thompson, E., & Davis, K. (2018). Material Selection for Extended Wear Part Life in Construction Equipment. Construction Engineering Quarterly, 52(1), 45-58.
- Wilson, M. (2022). Best Practices in Wear Part Installation and Alignment. Heavy Equipment Maintenance Guide, 7th Edition, 112-130.
- Lee, S., & Garcia, P. (2020). The Impact of Operator Techniques on Wear Part Longevity in Earthmoving Equipment. Journal of Construction Machinery, 39(3), 167-180.
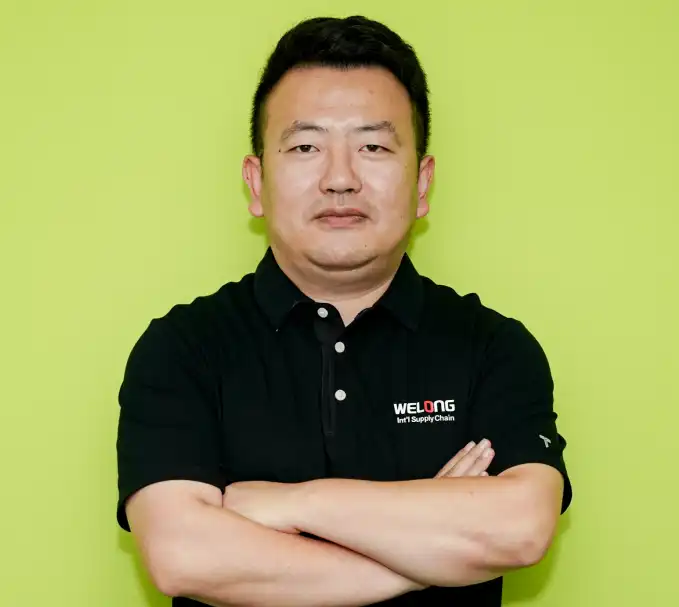
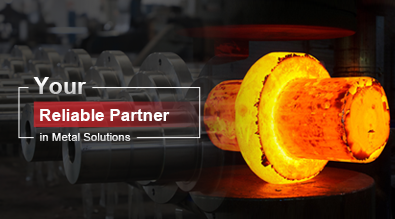
China WELONG-Your Reliable Partner in Metal Solutions