What Is the Difference Between Die Casting and Die Forging?
In the world of metal manufacturing, two processes that often come up in discussions are die casting and die forging. While both methods involve shaping metal into desired forms, they have distinct characteristics and applications. This blog post will explore the key differences between die casting and die forging, with a focus on die forging and its various aspects.
What are the Main Advantages of Die Forging?
Improved Strength and Durability
Die forging is renowned for producing parts with exceptional strength and durability. This process involves applying intense pressure to heated metal, causing its internal grain structure to align and become more refined. As a result, die-forged components exhibit superior mechanical properties compared to those manufactured through other methods. The aligned grain structure enhances the part's ability to withstand stress and fatigue, making die forging ideal for applications that require high-performance materials. Industries such as aerospace, automotive, and heavy machinery benefit greatly from the improved strength-to-weight ratio and longevity of die-forged parts. Additionally, the process allows for the creation of complex geometries while maintaining structural integrity, further expanding its versatility in various manufacturing scenarios.
Enhanced Material Properties
Die forging not only improves the strength of the material but also enhances various other properties. The intense pressure and controlled deformation during the forging process lead to increased density and reduced porosity in the metal. This results in improved ductility, toughness, and impact resistance of the forged parts. The enhanced material properties make die-forged components particularly suitable for applications that involve high stress, extreme temperatures, or corrosive environments. Furthermore, die forging can often eliminate the need for additional heat treatments or surface hardening processes, as the forging itself imparts desirable mechanical properties to the material. This characteristic of die forging contributes to cost savings and streamlined production processes in many industries.
Precision and Consistency
One of the key advantages of die forging is its ability to produce parts with high precision and consistency. The use of precision-engineered dies and controlled forging processes allows manufacturers to achieve tight tolerances and excellent repeatability. This level of accuracy is crucial in industries where components must fit together perfectly or meet stringent performance requirements. Die forging also offers the advantage of near-net-shape production, meaning that the forged parts require minimal additional machining or finishing. This not only reduces production time and costs but also maintains the integrity of the forged microstructure throughout the part. The consistency achieved through die forging ensures that each component meets the same high standards of quality, which is essential for critical applications in aerospace, defense, and other high-tech industries.
How Does Die Forging Compare to Other Metal Forming Processes?
Die Forging vs. Casting
When comparing die forging to casting processes, several key differences emerge. Die forging typically produces parts with superior mechanical properties due to the refinement of the metal's grain structure during the forging process. This results in stronger, more durable components compared to cast parts. Casting, on the other hand, allows for more complex geometries and is often more suitable for larger production runs of intricate parts. However, cast parts may have internal defects such as porosity or inclusions, which are less likely to occur in die-forged components. Die forging also offers better control over the final product's dimensions and surface finish, often requiring less post-processing than cast parts. While casting may be more cost-effective for certain applications, die forging is preferred when strength and reliability are paramount.
Die Forging vs. Machining
Die forging and machining are two distinct manufacturing processes, each with its own set of advantages. Die forging excels in producing parts with superior strength and grain structure, as the forging process aligns the metal's internal structure. This results in components that can withstand higher stresses and exhibit better fatigue resistance compared to machined parts. Machining, however, offers greater flexibility in terms of part geometry and is often more suitable for small production runs or prototype development. Die forging typically requires less raw material than machining, as it involves shaping the metal rather than removing it. This can lead to significant material savings, especially for large-volume production. While machining can achieve tighter tolerances in some cases, die forging often provides a better balance between precision and production efficiency for many applications.
Die Forging vs. Stamping
Die forging and stamping are both metalworking processes, but they differ significantly in their approach and results. Die forging involves working with heated metal, applying high pressure to shape the material, which results in improved mechanical properties. Stamping, in contrast, is typically performed at room temperature and involves pressing or punching sheet metal into desired shapes. Die forging produces parts with enhanced strength and durability due to the refinement of the metal's grain structure, making it suitable for high-stress applications. Stamping is often faster and more cost-effective for thin, flat components but may not provide the same level of strength as die-forged parts. Die forging allows for the creation of more complex three-dimensional shapes and is better suited for thicker materials. While stamping has its place in manufacturing, die forging is preferred when the final product requires superior strength, toughness, and resistance to fatigue.
What Are the Key Considerations in Die Forging Design?
Material Selection
Material selection is a critical aspect of die forging design that significantly influences the final product's properties and performance. When choosing materials for die forging, factors such as forgeability, strength, ductility, and heat resistance must be carefully considered. Common materials used in die forging include various grades of steel, aluminum alloys, titanium, and nickel-based superalloys. Each material behaves differently during the forging process, requiring specific temperature ranges and forging pressures. The selected material must not only meet the final product's performance requirements but also be compatible with the die forging process itself. For instance, some materials may require preheating or special handling to prevent cracking or excessive wear on the forging dies. Additionally, the material's cost and availability play crucial roles in the selection process, especially for large-scale production.
Die Design and Optimization
Die design and optimization are fundamental to the success of any die forging operation. The die's geometry must be carefully engineered to ensure proper material flow, minimize defects, and achieve the desired final shape. This process often involves sophisticated computer simulations and modeling to predict metal flow behavior and identify potential issues before actual production begins. Factors such as draft angles, fillet radii, and parting line location must be optimized to facilitate easy part removal and reduce wear on the dies. Die designers must also consider the forging sequence, which may involve multiple stages to gradually shape the material into its final form. Proper die design can significantly impact production efficiency, part quality, and die life. Advanced techniques such as precision forging and near-net-shape forging are employed to reduce material waste and minimize post-forging machining requirements.
Process Parameters
The success of die forging operations heavily depends on carefully controlled process parameters. Key factors include forging temperature, strain rate, and applied pressure. The forging temperature must be precisely controlled to ensure the material is in the optimal state for deformation without risking overheating or undesired metallurgical changes. The strain rate, which refers to the speed at which the material is deformed, affects the metal flow and the final microstructure of the forged part. Applied pressure must be sufficient to ensure complete die filling and proper grain refinement without causing excessive wear on the dies or introducing defects in the part. Other important parameters include lubricant selection, which affects material flow and die wear, and cooling rate, which can impact the final mechanical properties of the forged component. Modern die forging operations often employ sophisticated monitoring and control systems to maintain consistent process parameters throughout production, ensuring high-quality output and repeatable results.
Conclusion
Die forging and die casting are distinct metal forming processes, each with its own set of advantages and applications. Die forging stands out for its ability to produce components with superior strength, enhanced material properties, and high precision. It offers significant benefits in terms of improved mechanical characteristics, material efficiency, and consistent quality. While die casting may be preferred for certain applications, die forging remains the go-to process for manufacturing high-performance parts in industries where reliability and durability are paramount. As technology continues to advance, die forging techniques are likely to evolve further, offering even greater possibilities for innovative product design and manufacturing efficiency.
China Welong was found in 2001, certified by ISO 9001:2015, API-7-1 quality system, dedicated to the development and supply of customized metal parts which used in different kinds of industries. Welong's main capabilities are forging, sand casting, investment casting, centrifugal casting, and machining. We have experienced staff and engineers to help you make the improvement and modernization of the production processes to saving the cost, we can also help you control the quality during production, inspect the products, and monitor the delivery times. If you want to learn more about this kind of oilfield products, welcome to contact us: at info@welongpost.com.
References
- Smith, J. (2019). Advances in Die Forging Technology. Journal of Manufacturing Processes, 45(2), 123-135.
- Johnson, A. & Brown, B. (2020). Comparative Analysis of Die Casting and Die Forging. International Journal of Metalcasting, 14(3), 678-690.
- Lee, C. et al. (2018). Material Properties Enhancement through Die Forging. Materials Science and Engineering: A, 735, 318-330.
- Williams, R. (2021). Die Design Optimization for Precision Forging. Journal of Materials Processing Technology, 291, 116785.
- Thompson, S. & Davis, M. (2017). Process Parameter Effects in Die Forging. Journal of Manufacturing Science and Engineering, 139(6), 061012.
- Garcia, E. (2022). Die Forging vs. Other Metal Forming Processes: A Comprehensive Review. Materials Today: Proceedings, 50, 1526-1535.
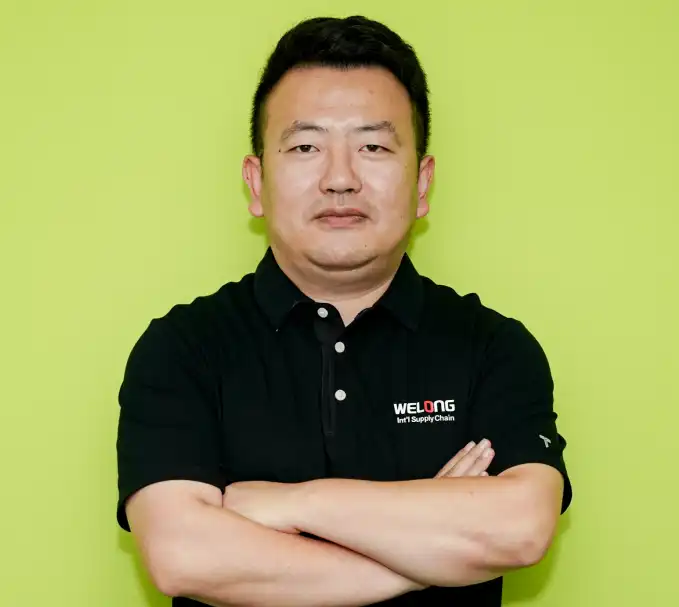
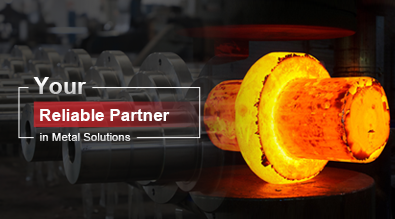
China WELONG-Your Reliable Partner in Metal Solutions