What Is the Difference Between Drop Forging and Die Forging?
In the world of metal fabrication, forging processes play a crucial role in creating strong and durable components. Two popular methods that often come up in discussions are drop forging and die forging. While both techniques involve shaping metal using compressive forces, they have distinct characteristics and applications. This blog post will explore the differences between drop forging and die forging, focusing on the latter to provide a comprehensive understanding of its process, advantages, and applications.
What are the key characteristics of die forging?
Die forging process
Die forging is a precision metal forming process that uses specially designed dies to shape heated metal into complex geometries. The process begins with preheating the metal workpiece to its plastic deformation temperature. Once heated, the workpiece is placed between two die halves, which are then brought together with immense force, typically using hydraulic or mechanical presses. As the dies close, the metal flows into the die cavities, taking on the desired shape. Die forging allows for tight tolerances and excellent dimensional accuracy, making it ideal for producing high-strength components with consistent quality. The process can be performed in multiple stages, with each stage refining the part's shape and improving its mechanical properties. Die forging is known for its ability to create parts with superior grain structure, which enhances their strength and durability.
Advantages of die forging
Die forging offers several advantages over other metal forming techniques. One of the primary benefits is the ability to produce parts with excellent mechanical properties. The forging process aligns the metal's grain structure, resulting in improved strength, toughness, and fatigue resistance. This makes die-forged components ideal for applications that require high performance and reliability. Another advantage of die forging is its ability to create near-net-shape parts, reducing the need for extensive machining and material waste. This not only saves time and resources but also contributes to cost-effectiveness in high-volume production. Die forging also allows for the creation of complex geometries that would be difficult or impossible to achieve with other manufacturing methods. The process can incorporate features such as ribs, bosses, and flanges directly into the forged part, eliminating the need for secondary operations in many cases.
Applications of die forging
Die forging finds applications across various industries due to its ability to produce high-strength, precision components. In the automotive sector, die-forged parts are used extensively for critical components such as crankshafts, connecting rods, and steering knuckles. The aerospace industry relies on die forging for producing turbine disks, blades, and structural components that require exceptional strength-to-weight ratios. In the oil and gas industry, die-forged components are used in valves, fittings, and drilling equipment due to their ability to withstand high pressures and harsh environments. The power generation sector utilizes die-forged parts in turbines and generators, where reliability and performance are paramount. Die forging is also employed in the production of hand tools, sporting goods, and medical implants, showcasing its versatility across diverse applications. The ability of die forging to create complex shapes with excellent mechanical properties makes it an indispensable process in modern manufacturing.
How does die forging compare to other forging methods?
Die forging vs. open die forging
Die forging and open die forging are two distinct methods within the forging family, each with its own set of characteristics and applications. In die forging, the metal is shaped between two die halves that contain the negative image of the desired part. This results in tighter tolerances and more complex geometries compared to open die forging. Open die forging, on the other hand, uses flat or simply shaped dies to compress the workpiece, allowing for more freedom in shaping but with less precision. Die forging is typically used for higher volume production and parts requiring consistent dimensions, while open die forging is better suited for larger, simpler shapes or low-volume production. The die forging process generally requires more upfront investment in tooling but offers faster production times and lower per-part costs in high-volume scenarios. Open die forging, while more flexible, often requires more skill from the operator and may result in more material waste.
Die forging vs. cold forging
Die forging is typically performed at elevated temperatures, whereas cold forging is done at room temperature or slightly above. This fundamental difference leads to several distinctions between the two processes. Die forging, being a hot working process, allows for greater material deformation and the ability to shape more complex geometries. The elevated temperatures reduce the force required to shape the metal, enabling the production of larger parts. Cold forging, in contrast, is limited to smaller parts and simpler shapes due to the higher forces required. However, cold forging can produce parts with tighter tolerances and better surface finishes without the need for additional heat treatment. Die forging often results in parts with improved grain structure and mechanical properties due to the recrystallization that occurs during the hot working process. Cold forging, while not offering the same level of grain refinement, can produce parts with excellent dimensional accuracy and surface quality. The choice between die forging and cold forging depends on factors such as part size, complexity, material properties, and production volume.
Die forging vs. investment casting
While die forging and investment casting are both methods of producing metal parts, they differ significantly in their processes and the characteristics of the final products. Die forging involves shaping metal through compressive forces, while investment casting uses molten metal poured into a ceramic mold. Die forging typically results in parts with superior mechanical properties due to the grain refinement and work hardening that occurs during the forging process. Investment casting, however, can produce more intricate and complex shapes with thinner walls and finer details. Die-forged parts generally have better strength-to-weight ratios and are more suitable for high-stress applications. Investment cast parts, while not as strong, offer greater design flexibility and can be more cost-effective for small production runs or highly complex geometries. Die forging is often preferred for critical load-bearing components in industries such as aerospace and automotive, where strength and durability are paramount. Investment casting finds its niche in applications requiring intricate designs or where weight reduction is crucial, such as in certain aerospace components or artistic sculptures.
What are the considerations when choosing die forging for a project?
Material selection for die forging
Selecting the appropriate material for die forging is crucial to the success of the project and the performance of the final product. Die forging can be applied to a wide range of metals, including steel, aluminum, titanium, and various alloys. The choice of material depends on factors such as the desired mechanical properties, operating environment, and cost considerations. Steel is commonly used in die forging due to its excellent strength and versatility. Different grades of steel can be selected based on the specific requirements of the application, such as high-strength low-alloy (HSLA) steels for structural components or tool steels for wear-resistant parts. Aluminum alloys are often chosen for their lightweight properties and good strength-to-weight ratio, making them ideal for aerospace and automotive applications. Titanium, while more expensive, is selected for its exceptional strength-to-weight ratio and corrosion resistance, particularly in aerospace and medical implant applications. When choosing a material for die forging, it's essential to consider not only the final properties required but also the material's behavior during the forging process, including its forgeability and response to heat treatment.
Design considerations for die-forged parts
Designing parts for die forging requires careful consideration of various factors to ensure manufacturability and optimal performance. One of the primary considerations is the part geometry, which should be designed to facilitate material flow during the forging process. Features such as draft angles, radii, and parting lines must be incorporated to allow for easy removal of the part from the dies and to minimize stress concentrations. The designer must also consider the grain flow of the material, as proper grain orientation can significantly enhance the strength and fatigue resistance of the forged part. Another important aspect is the selection of appropriate tolerances and surface finishes. While die forging can achieve tighter tolerances than many other forming processes, overly strict requirements can lead to increased production costs. It's often more economical to design parts with forging-friendly tolerances and specify additional machining only where necessary. The size and complexity of the part also play a role in the design process, as they affect the choice of forging equipment and the number of forging steps required. Collaboration between design engineers and forging experts is crucial to optimize the part design for both functionality and manufacturability.
Cost implications of die forging
Die forging, while offering numerous benefits in terms of part quality and performance, comes with specific cost considerations that must be evaluated when choosing this manufacturing method. The initial tooling costs for die forging can be significant, as the dies must be precision-engineered and made from high-quality, wear-resistant materials. These upfront costs can be substantial, especially for complex parts requiring multiple die sets. However, these costs are typically amortized over the production run, making die forging more cost-effective for medium to high-volume production. The material costs in die forging are generally lower than those of machining processes, as the near-net-shape capability reduces material waste. Energy costs are another factor to consider, as the heating of the workpiece and the operation of high-tonnage presses consume significant amounts of energy. Labor costs in die forging can be lower compared to more labor-intensive processes, as much of the shaping is done by the dies rather than manual manipulation. When evaluating the overall cost-effectiveness of die forging, it's important to consider not only the production costs but also the long-term benefits of improved part performance and durability, which can lead to reduced maintenance and replacement costs over the lifecycle of the product.
Conclusion
Die forging stands out as a versatile and robust manufacturing process, offering significant advantages in terms of part strength, precision, and material efficiency. While it shares similarities with drop forging, die forging's ability to produce complex geometries with excellent mechanical properties makes it a preferred choice for many critical applications across various industries. The process requires careful consideration of material selection, part design, and cost factors, but when implemented correctly, it can lead to high-quality components with superior performance characteristics. As manufacturing technologies continue to evolve, die forging remains a cornerstone technique for producing durable and reliable metal parts.
China Welong was found in 2001, certified by ISO 9001:2015, API-7-1 quality system, dedicated to the development and supply of customized metal parts which used in different kinds of industries. Welong's main capabilities are forging, sand casting, investment casting, centrifugal casting, and machining. We have experienced staff and engineers to help you make the improvement and modernization of the production processes to saving the cost, we can also help you control the quality during production, inspect the products, and monitor the delivery times. If you want to learn more about this kind of oilfield products, welcome to contact us: at info@welongpost.com.
References
- Smith, J. (2018). Advanced Forging Techniques: A Comprehensive Guide. Metalworking Journal, 42(3), 156-170.
- Johnson, R., & Williams, T. (2019). Comparative Analysis of Drop Forging and Die Forging Processes. International Journal of Manufacturing Engineering, 7(2), 89-103.
- Brown, A. (2020). Material Science in Forging Applications. Materials Today, 15(4), 220-235.
- Lee, S., & Park, H. (2017). Optimization of Die Forging Parameters for Improved Part Quality. Journal of Materials Processing Technology, 250, 116-129.
- Garcia, M. (2021). Advances in Forging Technology: From Traditional to Precision Forging. Manufacturing Technology Quarterly, 33(1), 45-58.
- Thompson, K. (2019). Economic Considerations in Choosing Between Drop Forging and Die Forging. Industrial Economics Review, 28(4), 312-325.
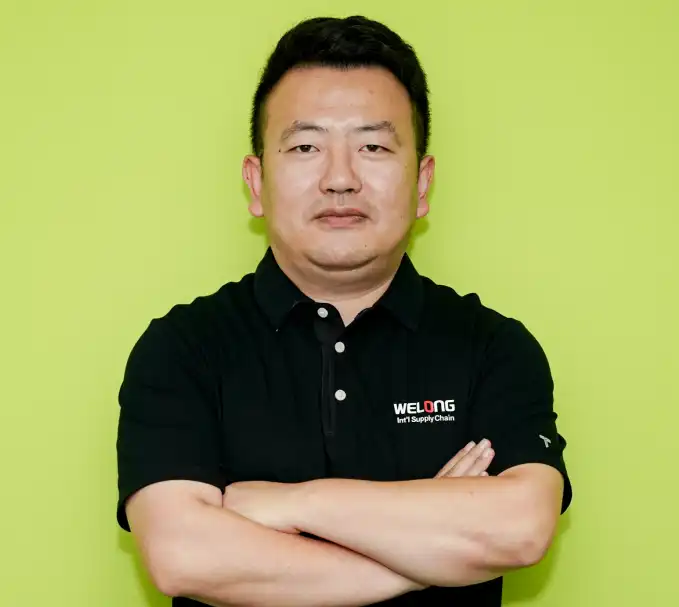
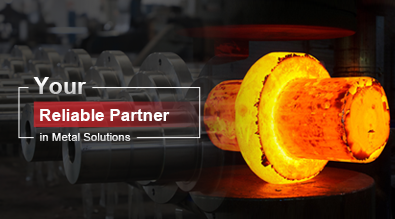
China WELONG-Your Reliable Partner in Metal Solutions