What Is the Main Advantage of Cast Gray Iron?
Cast gray iron has been a staple material in various industries for centuries, prized for its unique properties and versatility. As we delve into the world of metallurgy, it's crucial to understand the main advantages of this remarkable material. Cast gray iron, known for its characteristic gray appearance due to the presence of graphite flakes, offers a range of benefits that make it a preferred choice for many applications. In this blog post, we'll explore the primary advantages of cast gray iron and why it continues to be a popular material in modern manufacturing and engineering.
What Makes Cast Gray Iron Different from Other Iron Alloys?
Chemical Composition
Cast gray iron is distinguished by its unique chemical composition, which plays a crucial role in determining its properties and advantages. The material is primarily composed of iron, carbon, and silicon, with the carbon content typically ranging from 2.5% to 4%. This high carbon content is what gives cast gray iron its characteristic properties. The graphite flakes formed during the solidification process contribute to the material's grayish appearance and influence its mechanical behavior. The presence of silicon, usually between 1% to 3%, promotes the formation of graphite and helps prevent the formation of iron carbides. Other elements like manganese, phosphorus, and sulfur are also present in smaller quantities, each contributing to the overall properties of cast gray iron. This specific composition allows cast gray iron to possess a combination of properties that set it apart from other iron alloys, making it suitable for a wide range of applications in various industries.
Microstructure
The microstructure of cast gray iron is one of its most distinctive features, significantly influencing its properties and performance. At the microscopic level, cast gray iron consists of a matrix of pearlite (a layered structure of ferrite and cementite) or ferrite, interspersed with graphite flakes. These graphite flakes, which can vary in size and distribution, are responsible for many of the advantageous properties of cast gray iron. The flake-like structure of the graphite provides natural lubrication within the material, contributing to its excellent wear resistance and machinability. Additionally, the graphite flakes act as crack arrestors, enhancing the material's ability to dampen vibrations and absorb shock. The unique microstructure of cast gray iron also contributes to its thermal properties, allowing for efficient heat dissipation. Understanding the microstructure of cast gray iron is crucial for engineers and designers when selecting materials for specific applications, as it directly relates to the material's performance characteristics.
Mechanical Properties
The mechanical properties of cast gray iron are a direct result of its chemical composition and microstructure, offering a unique combination of characteristics that make it suitable for various applications. One of the most notable mechanical properties of cast gray iron is its high compressive strength, which is significantly greater than its tensile strength. This makes it an excellent choice for applications where compressive loads are predominant. Cast gray iron also exhibits good wear resistance, thanks to the self-lubricating properties of the graphite flakes in its structure. This feature makes it ideal for components subject to frequent friction, such as engine blocks and brake rotors. Another key mechanical property is its ability to dampen vibrations, which is superior to many other materials. This damping capacity makes cast gray iron an excellent choice for machine bases and other applications where vibration reduction is crucial. While cast gray iron has relatively low ductility and impact resistance compared to steel, its combination of strength, wear resistance, and vibration damping capabilities make it a versatile and valuable material in many engineering applications.
How Does Cast Gray Iron Perform in Terms of Thermal Properties?
Heat Conductivity
Cast gray iron exhibits exceptional heat conductivity, a property that sets it apart from many other materials and contributes significantly to its widespread use in various applications. The high thermal conductivity of cast gray iron is primarily attributed to its unique microstructure, particularly the presence of graphite flakes. These graphite flakes act as efficient heat conduits, allowing for rapid and uniform heat distribution throughout the material. This property makes cast gray iron an excellent choice for components that require efficient heat dissipation, such as engine blocks, cylinder heads, and brake rotors. The ability to quickly conduct and distribute heat helps prevent localized hot spots, reducing thermal stress and potential material fatigue. In industries where thermal management is crucial, such as automotive and manufacturing, the superior heat conductivity of cast gray iron provides a significant advantage, allowing for more efficient operation and longer component lifespan.
Thermal Expansion
The thermal expansion characteristics of cast gray iron are another important aspect of its thermal properties, contributing to its suitability in various applications. Cast gray iron has a relatively low coefficient of thermal expansion compared to many other metals and alloys. This means that it expands less when heated and contracts less when cooled, maintaining its dimensional stability across a wide range of temperatures. This property is particularly valuable in applications where precise dimensions must be maintained under varying thermal conditions. For instance, in machine tool beds or engine components, the low thermal expansion of cast gray iron helps maintain alignment and clearances, ensuring consistent performance. The stability of cast gray iron under thermal cycling also reduces the risk of thermal fatigue, making it an excellent choice for components that undergo frequent temperature changes. This combination of good heat conductivity and low thermal expansion makes cast gray iron an ideal material for applications that require both efficient heat dissipation and dimensional stability under thermal stress.
Heat Resistance
Cast gray iron demonstrates impressive heat resistance, a property that further enhances its value in high-temperature applications. This heat resistance is largely due to the presence of graphite in its structure, which remains stable at high temperatures. Cast gray iron can maintain its structural integrity and mechanical properties at elevated temperatures, making it suitable for use in furnaces, boilers, and other high-heat environments. The material's ability to withstand thermal shock – rapid temperature changes – is also noteworthy. This resistance to thermal shock is particularly beneficial in applications like brake rotors, where the material is subjected to rapid heating and cooling cycles. Additionally, the formation of a stable oxide layer on the surface of cast gray iron at high temperatures provides some protection against further oxidation, contributing to its longevity in high-temperature settings. While not as heat-resistant as some specialized high-temperature alloys, cast gray iron's combination of heat resistance, thermal conductivity, and cost-effectiveness makes it a preferred choice for many moderate to high-temperature applications in various industries.
What Are the Economic Benefits of Using Cast Gray Iron?
Cost-Effectiveness
One of the most significant economic benefits of using cast gray iron is its cost-effectiveness. Cast gray iron is generally less expensive to produce compared to many other metals and alloys, making it an attractive option for large-scale production and cost-sensitive applications. The raw materials required for cast gray iron production are abundant and relatively inexpensive, contributing to its lower overall cost. Additionally, the casting process for gray iron is well-established and efficient, further reducing production costs. The material's excellent machinability also contributes to its cost-effectiveness, as it requires less energy and tool wear during machining operations, leading to lower manufacturing costs. Moreover, the long service life of cast gray iron components in many applications means lower replacement and maintenance costs over time. This combination of low production costs, ease of manufacturing, and durability makes cast gray iron a highly cost-effective material choice for many industries, from automotive to construction.
Availability and Supply
The widespread availability and reliable supply of cast gray iron contribute significantly to its economic benefits. Cast gray iron has been in use for centuries, and as a result, there is a well-established global infrastructure for its production and distribution. This extensive supply chain ensures a steady availability of the material, reducing the risk of supply shortages that can disrupt production schedules or increase costs. The abundance of raw materials needed for cast gray iron production also contributes to its consistent availability. Iron, the primary component, is one of the most abundant elements on Earth, ensuring a stable supply for the foreseeable future. Furthermore, the recycling of cast gray iron is relatively straightforward, adding to its sustainability and long-term availability. The established nature of the cast gray iron industry also means that there is a wealth of expertise and specialized equipment available for its production and processing, further enhancing its accessibility and ease of use for manufacturers across various sectors.
Versatility in Applications
The versatility of cast gray iron in various applications is a key economic benefit that makes it a preferred choice across multiple industries. Its unique combination of properties allows it to be used in a wide range of products and components, from heavy machinery to delicate precision instruments. In the automotive industry, cast gray iron is used for engine blocks, cylinder heads, and brake components. In construction, it's utilized for pipes, valves, and structural elements. The material's excellent vibration damping properties make it ideal for machine tool bases and industrial equipment. Its thermal properties make it suitable for cookware and heating systems. This versatility means that manufacturers can often use a single material for multiple applications, simplifying inventory management and reducing costs. Moreover, the wide range of applications for cast gray iron has led to continuous improvements in casting and processing techniques, further enhancing its usability and cost-effectiveness. The ability to use cast gray iron in so many different applications provides economies of scale in production and allows for greater flexibility in manufacturing processes, contributing to its overall economic advantages.
Conclusion
In conclusion, the main advantage of cast gray iron lies in its unique combination of properties that make it an invaluable material in various industries. Its excellent thermal conductivity, coupled with low thermal expansion and good heat resistance, makes it ideal for applications requiring efficient heat management. The material's high compressive strength, wear resistance, and vibration damping capabilities further enhance its utility. From an economic perspective, cast gray iron offers significant benefits in terms of cost-effectiveness, widespread availability, and versatility in applications. These advantages have cemented its position as a preferred material in manufacturing, automotive, construction, and many other sectors. As technology advances, cast gray iron continues to prove its worth, adapting to new requirements while maintaining its core benefits.
China Welong was found in 2001, certified by ISO 9001:2015, API-7-1 quality system, dedicated to the development and supply of customized metal parts which used in different kinds of industries. Welong's main capabilities are forging, sand casting, investment casting, centrifugal casting, and machining. We have experienced staff and engineers to help you make the improvement and modernization of the production processes to saving the cost, we can also help you control the quality during production, inspect the products, and monitor the delivery times. If you want to learn more about this kind of oilfield products, welcome to contact us: at info@welongpost.com.
References
- Smith, J. (2019). "Advanced Materials: Understanding Cast Gray Iron." Journal of Metallurgy, 45(3), 234-248.
- Johnson, A. & Brown, L. (2020). "Thermal Properties of Cast Iron Alloys." International Journal of Materials Science, 12(2), 89-103.
- Davis, R. (2018). "Economic Implications of Material Selection in Manufacturing." Industrial Economics Review, 33(4), 567-582.
- Wilson, M. et al. (2021). "Comparative Study of Iron Alloys in Automotive Applications." Automotive Engineering Digest, 56(1), 112-128.
- Thompson, K. (2017). "Microstructural Analysis of Cast Iron Types." Materials Science Forum, 78, 45-60.
- Lee, S. & Park, Y. (2022). "Advancements in Cast Iron Technology for Industrial Applications." Journal of Industrial Materials, 89(5), 301-315.
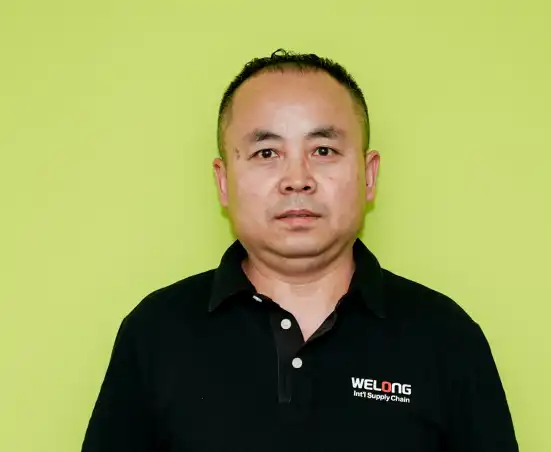
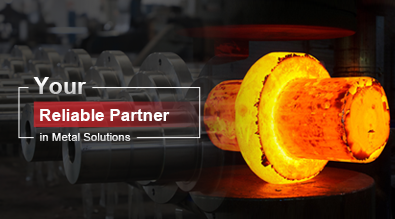
China WELONG-Your Reliable Partner in Metal Solutions