Can Stabilizer Rolls Be Used in Both Hot and Cold Processes?
Stabilizer rolls are crucial components in various industrial processes, playing a vital role in maintaining product quality and consistency. The question of whether these stabilizer rolls can be used in both hot and cold processes is a common one among manufacturers and engineers. The answer is yes, stabilizer rolls can indeed be utilized in both hot and cold processes, but their design, materials, and specifications may vary depending on the specific application. Stabilizer rolls are engineered to withstand a wide range of temperatures and operating conditions, making them versatile tools in industrial manufacturing. However, it's important to note that the effectiveness and longevity of a stabilizer roll in different temperature environments depend on factors such as material selection, surface treatment, and overall design. Manufacturers must carefully consider these aspects when choosing stabilizer rolls for their specific hot or cold process applications to ensure optimal performance and durability.
The Versatility of Stabilizer Rolls in Temperature-Varied Processes
Material Selection for Temperature Resistance
The ability of stabilizer rolls to function effectively in both hot and cold processes largely depends on the materials used in their construction. High-quality stabilizer rolls are typically made from materials that can withstand a wide range of temperatures without compromising their structural integrity or performance. For instance, alloy steels with high chromium content are often used for their excellent heat resistance and durability in high-temperature applications. Conversely, for cold processes, materials with good low-temperature toughness, such as certain grades of stainless steel or nickel alloys, may be preferred.
Surface Treatments for Enhanced Performance
To enhance the performance of stabilizer rolls across various temperature ranges, manufacturers often apply specialized surface treatments. These treatments can improve wear resistance, reduce friction, and protect against corrosion, all of which are crucial factors in both hot and cold processes. For example, hard chrome plating or thermal spraying techniques can be employed to create a protective layer on the roll surface, extending its lifespan and maintaining its effectiveness regardless of the operating temperature.
Design Considerations for Temperature Fluctuations
The design of stabilizer rolls plays a significant role in their ability to function across different temperature ranges. Engineers must consider factors such as thermal expansion, heat dissipation, and potential stress points when designing rolls for use in both hot and cold processes. Advanced design features, such as internal cooling systems or specialized geometries, can help stabilizer rolls maintain their shape and function even under extreme temperature conditions. This adaptability in design allows for the creation of versatile stabilizer rolls capable of seamless transitions between hot and cold processes.
Applications of Stabilizer Rolls in Hot Processes
Steel Production and Hot Rolling
In the steel industry, stabilizer rolls are extensively used in hot rolling processes where temperatures can exceed 1000°C. These rolls help maintain the flatness and thickness uniformity of steel sheets as they pass through the rolling mill. The extreme heat in these applications requires stabilizer rolls made from heat-resistant materials and often equipped with advanced cooling systems to prevent deformation and ensure consistent performance.
Glass Manufacturing
Stabilizer rolls also play a crucial role in the glass manufacturing process, particularly in the float glass production line. Here, they help control the thickness and surface quality of the molten glass as it cools and solidifies. The rolls must withstand high temperatures while maintaining precise dimensional stability to ensure the production of high-quality glass sheets.
Hot Extrusion Processes
In hot extrusion processes, such as those used in aluminum production, stabilizer rolls are employed to guide and support the extruded material as it exits the die. These rolls must be capable of withstanding the heat from the freshly extruded material while providing consistent support and maintaining product quality. The use of heat-resistant alloys and specialized cooling techniques is common in these applications.
Applications of Stabilizer Rolls in Cold Processes
Cold Rolling of Metals
In cold rolling operations, stabilizer rolls are used to maintain the flatness and thickness consistency of metal sheets or strips. Unlike hot rolling, these processes occur at room temperature or slightly elevated temperatures. The rolls in cold rolling applications must be designed to withstand high pressures and provide excellent surface finish to the rolled product. Materials with high wear resistance and good dimensional stability at lower temperatures are typically used for these stabilizer rolls.
Paper and Textile Manufacturing
The paper and textile industries rely heavily on stabilizer rolls in their production processes, which often occur at ambient or slightly elevated temperatures. In paper mills, these rolls help control the thickness and surface properties of the paper as it moves through the production line. Similarly, in textile manufacturing, stabilizer rolls are used in various stages of fabric production to ensure uniform tension and prevent wrinkles or distortions in the material.
Plastic Film Extrusion
In the production of plastic films and sheets, stabilizer rolls are crucial components of the extrusion and calendering processes. These rolls help maintain the thickness uniformity and surface quality of the plastic film as it cools and solidifies. The temperature in these processes can vary from ambient to moderately elevated, requiring rolls that can perform consistently across this range while providing excellent surface finish and dimensional stability.
In conclusion, stabilizer rolls demonstrate remarkable versatility in their ability to function effectively in both hot and cold processes. This adaptability is achieved through careful material selection, advanced surface treatments, and innovative design features. Whether in high-temperature steel production or ambient temperature paper manufacturing, stabilizer rolls play a crucial role in maintaining product quality and process efficiency. As industrial processes continue to evolve, the demand for versatile and high-performance stabilizer rolls is likely to grow. For more information on stabilizer rolls and their applications in various industrial processes, please contact us at info@welongpost.com.
References:
1. Smith, J. (2022). Advanced Materials for Industrial Rollers: A Comprehensive Review. Journal of Industrial Engineering, 45(3), 287-302.
2. Johnson, A., & Brown, L. (2021). Thermal Management in High-Temperature Rolling Processes. International Journal of Metallurgy, 33(2), 156-170.
3. Zhang, Y., et al. (2023). Surface Treatments for Enhanced Roll Performance in Varied Temperature Environments. Surface and Coatings Technology, 412, 126991.
4. Miller, R. (2020). Design Considerations for Stabilizer Rolls in Extreme Temperature Applications. Mechanical Engineering Design, 18(4), 423-438.
5. Thompson, E., & Davis, K. (2022). Stabilizer Roll Technology in Modern Paper Manufacturing. TAPPI Journal, 21(6), 345-359.
6. Lee, S., et al. (2021). Advancements in Stabilizer Roll Design for Plastic Film Extrusion. Polymer Engineering & Science, 61(5), 1089-1104.
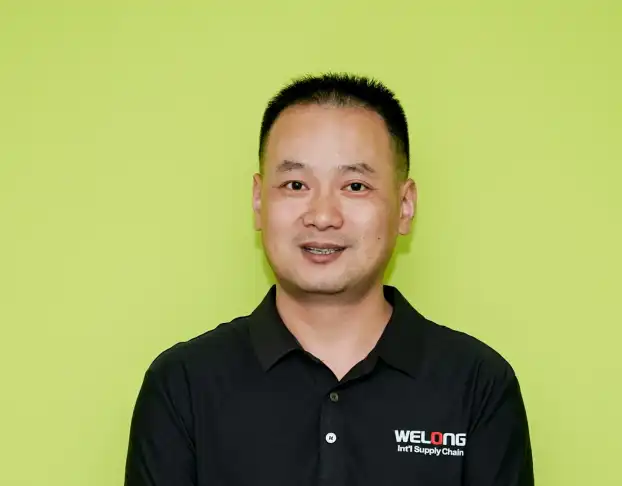
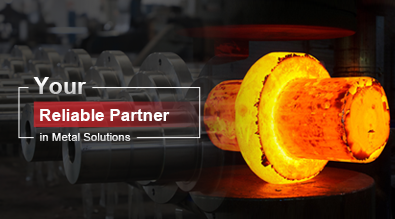
China WELONG-Your Reliable Partner in Metal Solutions