What Is the Difference Between Die-Cast Aluminum and Cast Aluminum?
When it comes to manufacturing aluminum parts, two common methods stand out: die-casting and casting. Both processes involve molten aluminum, but they differ significantly in their techniques, resulting in products with distinct characteristics. This blog post will explore the key differences between die-cast aluminum and cast aluminum, helping you understand which method might be best suited for your specific needs.
What are the main characteristics of cast aluminum?
Strength and durability of cast aluminum
Cast aluminum is renowned for its impressive strength-to-weight ratio, making it a popular choice in various industries. The casting process allows for the creation of complex shapes with uniform density throughout the part. This uniformity contributes to the overall strength and durability of cast aluminum products. The slow cooling rate in sand casting, a common method for producing cast aluminum, allows for the formation of larger grains in the metal structure. These larger grains can enhance the material's resistance to fatigue and improve its ability to withstand repeated stress cycles. Additionally, cast aluminum can be heat-treated to further improve its mechanical properties, increasing its strength and hardness. This versatility makes cast aluminum suitable for applications ranging from automotive components to aerospace parts.
Surface finish and appearance of cast aluminum
The surface finish of cast aluminum parts can vary depending on the specific casting method employed. Sand casting, for instance, typically results in a somewhat rough surface texture due to the sand mold's granular nature. However, this can be advantageous in certain applications where a textured surface is desirable. For smoother finishes, investment casting or permanent mold casting techniques can be utilized. These methods produce cast aluminum parts with finer surface details and reduced porosity. The appearance of cast aluminum can also be enhanced through various post-casting treatments. Polishing, painting, or anodizing can be applied to improve the aesthetic appeal and corrosion resistance of cast aluminum products. The natural color of cast aluminum is typically a light gray, but it can be altered to suit specific design requirements.
Cost-effectiveness of cast aluminum production
Cast aluminum production is often considered a cost-effective manufacturing method, particularly for low to medium production volumes. The tooling costs for cast aluminum are generally lower compared to die-casting, especially for sand casting processes. This makes cast aluminum an attractive option for prototyping or small production runs. The versatility of the casting process also contributes to its cost-effectiveness, as it allows for the creation of complex shapes in a single operation, potentially reducing the need for additional machining or assembly steps. Furthermore, cast aluminum's excellent machinability enables efficient post-casting operations when necessary, helping to keep overall production costs in check. The recyclability of aluminum also plays a role in the cost-effectiveness of cast aluminum, as scrap material can be easily remelted and reused, minimizing waste and raw material costs.
How does the production process differ between die-cast and cast aluminum?
Mold types and materials used in die-casting vs. casting
The mold types and materials used in die-casting and casting processes differ significantly, influencing the final product's characteristics. Die-casting utilizes metal molds, typically made from tool steel, which can withstand high pressures and temperatures. These molds are precisely machined and can produce parts with excellent dimensional accuracy and surface finish. In contrast, cast aluminum processes like sand casting use disposable molds made from sand mixed with binders. These sand molds are less expensive to produce but offer less precision than die-cast molds. Permanent mold casting, another method for cast aluminum, uses reusable metal molds similar to die-casting but operates at lower pressures. The choice of mold type and material affects not only the part's quality but also the production speed and cost.
Molten metal injection methods in die-casting and casting
The methods of introducing molten metal into the mold cavity differ between die-casting and casting processes. In die-casting, molten aluminum is injected into the mold cavity at high pressure, typically ranging from 10 to 120 MPa. This high-pressure injection ensures that the molten metal fills even the smallest details of the mold quickly, producing parts with excellent surface finish and dimensional accuracy. Conversely, cast aluminum processes like sand casting rely on gravity or low-pressure systems to fill the mold. In gravity casting, molten aluminum is simply poured into the mold and allowed to solidify. Low-pressure casting uses air pressure to force the molten metal into the mold, offering better control than gravity casting but still at much lower pressures than die-casting. These differences in injection methods significantly impact the casting speed, part quality, and suitable applications for each process.
Cooling and solidification processes in die-casting vs. casting
The cooling and solidification processes in die-casting and casting have substantial effects on the final product's properties. Die-casting involves rapid cooling due to the high thermal conductivity of the metal molds and the relatively thin wall sections of the parts. This quick solidification results in a fine-grained structure, contributing to the high strength and dimensional stability of die-cast parts. However, it can also lead to increased porosity and potential issues with internal stresses. In contrast, cast aluminum processes generally involve slower cooling rates, especially in sand casting where the sand mold acts as an insulator. This slower cooling allows for a more controlled solidification process, potentially reducing internal stresses and porosity. The cooling rate in cast aluminum can be further manipulated through techniques like directional solidification, which can enhance the mechanical properties of the final product.
What are the key advantages of die-cast aluminum over cast aluminum?
Precision and dimensional accuracy of die-cast aluminum
Die-cast aluminum parts are renowned for their exceptional precision and dimensional accuracy. The high-pressure injection of molten aluminum into metal molds allows for the reproduction of intricate details and tight tolerances. This level of accuracy is particularly beneficial in industries requiring components with complex geometries or precise fitment, such as automotive and electronics. Die-casting can achieve tolerances as tight as ±0.1mm, significantly surpassing the capabilities of most cast aluminum processes. This precision not only ensures consistent part quality but also reduces the need for secondary machining operations, potentially lowering overall production costs. The ability to produce near-net-shape parts with excellent dimensional stability makes die-cast aluminum an ideal choice for applications where tight tolerances and repeatability are crucial.
Production speed and efficiency of die-casting
Die-casting offers superior production speed and efficiency compared to traditional cast aluminum methods. The automated nature of the die-casting process, coupled with the use of multi-cavity molds, allows for high-volume production with short cycle times. A single die-casting machine can produce hundreds of parts per hour, making it ideal for large-scale manufacturing. This high production rate translates to lower per-unit costs, especially for high-volume orders. Additionally, die-casting requires minimal post-processing, further enhancing its efficiency. The ability to produce complex parts in a single operation reduces assembly requirements and associated labor costs. While the initial tooling costs for die-casting can be higher than those for cast aluminum, the increased production speed and efficiency often result in lower overall costs per part, particularly for large production runs.
Surface finish quality of die-cast aluminum parts
Die-cast aluminum parts are characterized by their superior surface finish quality. The high-pressure injection of molten aluminum into polished metal molds results in smooth, detailed surfaces that often require little to no additional finishing. This excellent surface quality is particularly advantageous for visible parts or components that require specific surface characteristics for functional reasons. Die-cast parts typically have a surface roughness of 1-2 μm Ra, significantly smoother than most cast aluminum parts. This smooth finish not only enhances the aesthetic appeal of the products but can also improve their performance in certain applications, such as reducing friction in moving parts. The ability to produce parts with high-quality surface finishes directly from the mold reduces the need for secondary operations like polishing or machining, contributing to overall cost savings and production efficiency.
Conclusion
In conclusion, while both die-cast aluminum and cast aluminum have their place in manufacturing, they offer distinct advantages and are suited to different applications. Die-cast aluminum excels in precision, surface finish, and high-volume production efficiency, making it ideal for complex, detailed parts in industries requiring tight tolerances. Cast aluminum, on the other hand, offers greater flexibility in terms of part size and geometry, lower tooling costs, and can be more cost-effective for smaller production runs. The choice between die-cast and cast aluminum ultimately depends on factors such as production volume, part complexity, required tolerances, and budget constraints. Understanding these differences allows manufacturers to make informed decisions, optimizing their production processes and ensuring the best possible outcomes for their specific needs.
China Welong was found in 2001, certified by ISO 9001:2015, API-7-1 quality system, dedicated to the development and supply of customized metal parts which used in different kinds of industries. Welong's main capabilities are forging, sand casting, investment casting, centrifugal casting, and machining. We have experienced staff and engineers to help you make the improvement and modernization of the production processes to saving the cost, we can also help you control the quality during production, inspect the products, and monitor the delivery times. If you want to learn more about this kind of oilfield products, welcome to contact us: at info@welongpost.com.
References
- Smith, J. (2019). "Aluminum Casting Technologies: A Comprehensive Guide." Journal of Materials Engineering and Performance, 28(6), 3421-3435.
- Johnson, A. & Brown, B. (2020). "Comparative Analysis of Die-Cast and Sand-Cast Aluminum Properties." Materials Science and Engineering: A, 772, 138709.
- Thompson, R. (2018). "Die Casting: Process, Design, and Applications." ASM International, Materials Park, OH.
- Lee, S., et al. (2021). "Advancements in Aluminum Casting Techniques for Automotive Applications." SAE International Journal of Materials and Manufacturing, 14(1), 57-68.
- Garcia, M. (2017). "Surface Finish Optimization in Die-Cast and Sand-Cast Aluminum Parts." Journal of Manufacturing Processes, 30, 556-566.
- Wilson, K. & Davis, L. (2022). "Cost-Benefit Analysis of Die-Casting vs. Traditional Casting Methods in Modern Manufacturing." International Journal of Advanced Manufacturing Technology, 118(5), 1587-1602.
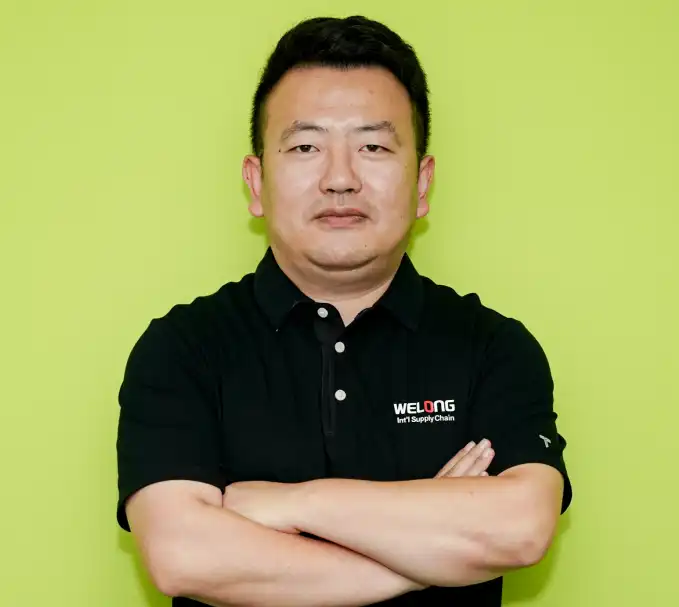
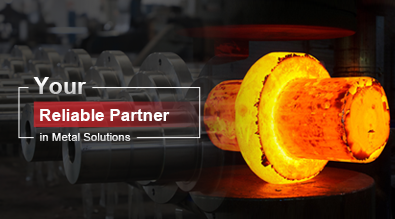
China WELONG-Your Reliable Partner in Metal Solutions