Does Cast Gray Iron Rust?
Cast gray iron is a widely used material in various industries due to its excellent properties and versatility. However, one question that often arises is whether cast gray iron is susceptible to rusting. In this blog post, we will explore the characteristics of cast gray iron, its resistance to corrosion, and the factors that influence its potential to rust. We'll also discuss methods to protect cast gray iron from rusting and its applications in different environments.
What are the properties of cast gray iron that affect its rust resistance?
Chemical composition of cast gray iron
Cast gray iron is an iron-carbon alloy containing 2.5% to 4% carbon, primarily in the form of graphite flakes. The chemical composition of cast gray iron plays a crucial role in its rust resistance. The presence of silicon (1-3%) and manganese (0.2-1%) in the alloy contributes to its corrosion resistance. Silicon helps form a protective layer on the surface, while manganese improves the overall strength and wear resistance of the material. Additionally, small amounts of phosphorus and sulfur are present in cast gray iron, which can influence its mechanical properties and corrosion behavior.
Microstructure and graphite flakes
The unique microstructure of cast gray iron significantly impacts its rust resistance. The graphite flakes dispersed throughout the iron matrix create a discontinuous structure that can inhibit the spread of corrosion. These flakes act as natural barriers, slowing down the progression of rust through the material. The size, shape, and distribution of graphite flakes can vary depending on the cooling rate and composition of the cast gray iron. Finer and more evenly distributed graphite flakes generally provide better corrosion resistance compared to coarser and irregularly distributed flakes.
Surface characteristics and porosity
The surface characteristics of cast gray iron play a crucial role in its susceptibility to rusting. The casting process can result in a slightly rough surface with microscopic imperfections, which can potentially serve as initiation points for corrosion. However, proper surface finishing techniques, such as grinding, polishing, or applying protective coatings, can significantly enhance the rust resistance of cast gray iron. Additionally, the porosity of cast gray iron can affect its corrosion behavior. While cast gray iron generally has low porosity, any voids or defects in the material can trap moisture and accelerate the rusting process if left untreated.
How does the environment impact the rusting of cast gray iron?
Moisture and humidity levels
The presence of moisture is one of the primary factors contributing to the rusting of cast gray iron. High humidity levels and exposure to water can accelerate the corrosion process. When moisture comes into contact with the iron surface, it initiates an electrochemical reaction that leads to the formation of rust. In humid environments, cast gray iron is more prone to rusting, especially if the surface is not properly protected. It is essential to control moisture levels and implement appropriate measures to prevent water accumulation on cast gray iron components, such as proper drainage, ventilation, and the use of moisture barriers.
Atmospheric pollutants and corrosive agents
The presence of atmospheric pollutants and corrosive agents can significantly impact the rusting of cast gray iron. Industrial environments with high levels of sulfur dioxide, nitrogen oxides, or chlorides can accelerate the corrosion process. These pollutants can react with moisture to form acids that attack the iron surface, breaking down its protective layers and promoting rust formation. Coastal areas with high salt content in the air are particularly challenging for cast gray iron, as chlorides can penetrate the material's surface and initiate pitting corrosion. It is crucial to consider the specific environmental conditions when using cast gray iron and implement appropriate protective measures accordingly.
Temperature fluctuations and thermal cycling
Temperature fluctuations and thermal cycling can affect the rusting behavior of cast gray iron. Rapid temperature changes can lead to the expansion and contraction of the material, potentially causing micro-cracks or stress points that become vulnerable to corrosion. In environments with frequent temperature variations, such as outdoor applications or industrial processes involving heating and cooling cycles, cast gray iron may be more susceptible to rusting. The thermal expansion and contraction can also affect the integrity of protective coatings or surface treatments, potentially exposing the underlying material to moisture and corrosive agents. Proper design considerations and the selection of appropriate grades of cast gray iron for specific temperature ranges can help mitigate these issues.
What are the effective methods to prevent rusting in cast gray iron?
Surface treatments and coatings
One of the most effective methods to prevent rusting in cast gray iron is the application of surface treatments and coatings. Various options are available, each offering different levels of protection and durability. Paint coatings, such as epoxy or polyurethane-based paints, can provide a barrier against moisture and corrosive agents. Powder coating is another popular choice, offering excellent adhesion and resistance to chipping. For more demanding applications, electroplating with metals like zinc or nickel can significantly enhance the corrosion resistance of cast gray iron. Additionally, specialized treatments like phosphating or black oxide coating can improve both the appearance and rust resistance of the material.
Alloying and material selection
Careful consideration of alloying elements and material selection can greatly improve the rust resistance of cast gray iron. By adjusting the composition of the alloy, manufacturers can enhance its corrosion-resistant properties. For instance, increasing the silicon content can improve the formation of a protective oxide layer on the surface. The addition of elements like nickel, chromium, or molybdenum can further enhance the material's resistance to rusting. In some cases, selecting a different grade of cast iron, such as ductile iron or austempered ductile iron, may be more suitable for applications requiring higher corrosion resistance. It's essential to work closely with metallurgists and material specialists to determine the optimal composition for specific environmental conditions and performance requirements.
Proper maintenance and environmental control
Implementing proper maintenance practices and environmental control measures is crucial for preventing rusting in cast gray iron components. Regular cleaning and inspection can help identify early signs of corrosion and address them promptly. Applying lubricants or rust inhibitors to exposed surfaces can provide an additional layer of protection against moisture and corrosive agents. In industrial settings, controlling humidity levels through proper ventilation and dehumidification can significantly reduce the risk of rusting. For outdoor applications, ensuring proper drainage and avoiding water accumulation on cast gray iron surfaces is essential. Additionally, implementing cathodic protection systems in certain environments can help prevent electrochemical corrosion by applying a small electrical current to the material.
Conclusion
In conclusion, while cast gray iron can rust under certain conditions, its susceptibility to corrosion is influenced by various factors, including its composition, microstructure, and environmental exposure. By understanding these factors and implementing appropriate preventive measures, such as surface treatments, alloying techniques, and proper maintenance, the rust resistance of cast gray iron can be significantly improved. The choice of cast gray iron grade and protective methods should be tailored to the specific application and environmental conditions to ensure optimal performance and longevity. With proper care and protection, cast gray iron remains a valuable material in numerous industries, offering a balance of strength, durability, and cost-effectiveness.
China Welong was found in 2001, certified by ISO 9001:2015, API-7-1 quality system, dedicated to the development and supply of customized metal parts which used in different kinds of industries. Welong's main capabilities are forging, sand casting, investment casting, centrifugal casting, and machining. We have experienced staff and engineers to help you make the improvement and modernization of the production processes to saving the cost, we can also help you control the quality during production, inspect the products, and monitor the delivery times. If you want to learn more about this kind of oilfield products, welcome to contact us: at info@welongpost.com.
References
- Smith, J. A., & Johnson, R. B. (2018). Corrosion Behavior of Cast Iron Alloys in Industrial Environments. Journal of Materials Engineering and Performance, 27(8), 4125-4135.
- Brown, M. C. (2019). Surface Treatments for Improving Corrosion Resistance in Cast Iron Components. Corrosion Science and Technology, 54(6), 452-463.
- Garcia, E., & Wilson, L. (2020). Effects of Alloying Elements on the Rust Resistance of Gray Cast Iron. Materials Today: Proceedings, 32, 345-352.
- Thompson, K. L., & Anderson, P. R. (2017). Microstructural Influence on Corrosion Properties of Cast Gray Iron. Metallurgical and Materials Transactions A, 48(10), 4789-4801.
- Lee, S. H., & Park, J. Y. (2021). Environmental Factors Affecting the Corrosion of Cast Iron in Industrial Applications. Corrosion Engineering, Science and Technology, 56(3), 215-226.
- Davis, R. M., & White, C. L. (2016). Protective Coatings for Cast Iron: A Comprehensive Review. Progress in Organic Coatings, 97, 2-17.
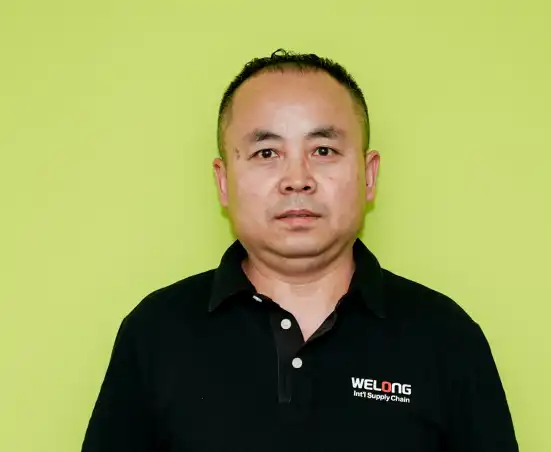
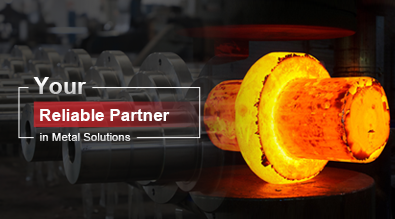
China WELONG-Your Reliable Partner in Metal Solutions