How Do Base Trays Interact with Other Equipment in Heat Treatment?
Base trays play a crucial role in heat treatment processes, serving as the foundation for various components and facilitating efficient thermal operations. These specialized base trays are designed to interact seamlessly with other equipment in the heat treatment setup, ensuring optimal performance and uniformity in the treatment of materials. By providing a stable platform for workpieces and enabling proper heat distribution, base trays contribute significantly to the overall effectiveness of heat treatment procedures. Their interaction with furnaces, cooling systems, and material handling equipment is carefully orchestrated to maintain precise temperature control, prevent distortion, and enhance the quality of the treated components. Understanding the intricate relationship between base trays and other heat treatment equipment is essential for industries relying on thermal processing to improve material properties and meet stringent quality standards.
Design and Functionality of Base Trays in Heat Treatment Systems
Material Selection for Base Trays
The choice of materials for base trays is paramount in determining their performance and longevity in heat treatment applications. High-temperature alloys, such as heat-resistant stainless steels or nickel-based superalloys, are commonly used due to their exceptional thermal stability and resistance to oxidation. These materials ensure that the base trays maintain their structural integrity and dimensional accuracy even when subjected to extreme temperatures and thermal cycling. The selection process considers factors like thermal conductivity, coefficient of thermal expansion, and resistance to creep, ensuring that the base trays can withstand the rigors of repeated heat treatment cycles without compromising their functionality.
Structural Features for Enhanced Performance
Base trays are engineered with specific structural features to optimize their interaction with heat treatment equipment and workpieces. The surface of the tray often incorporates a grid or pattern design that promotes uniform heat distribution and minimizes contact points with the treated components. This design reduces the risk of localized overheating or cooling, contributing to more consistent heat treatment results. Additionally, many base trays feature reinforced edges or internal support structures to prevent warping or deformation under high-temperature conditions, maintaining a flat and stable surface throughout the heat treatment process.
Integration of Sensors and Monitoring Systems
Modern base trays are increasingly equipped with integrated sensors and monitoring systems that enhance their interaction with other heat treatment equipment. Temperature sensors embedded within the tray structure provide real-time data on thermal conditions, allowing for precise control of heating and cooling rates. Some advanced designs incorporate RFID tags or other tracking mechanisms, enabling automated material handling systems to identify and manage the trays throughout the heat treatment workflow. This integration of smart technologies facilitates better process control, traceability, and optimization of heat treatment operations.
Interaction with Furnaces and Heating Systems
Heat Transfer Mechanisms
The interaction between base trays and furnaces is primarily characterized by the heat transfer mechanisms at play. Conduction, convection, and radiation all contribute to the heating of the base tray and the components it supports. The design of the base tray, including its material properties and surface features, influences how effectively heat is transferred from the furnace atmosphere to the workpieces. For instance, trays with higher thermal conductivity may promote more rapid and uniform heating, while those with specialized coatings or surface treatments can enhance radiative heat transfer in certain applications.
Positioning and Orientation within Furnaces
The positioning and orientation of base trays within furnaces are critical factors in ensuring optimal heat treatment results. Furnace designs often incorporate specific support structures or rails to accommodate base trays, allowing for precise placement and easy loading/unloading. The orientation of the tray relative to heating elements or gas flow patterns in the furnace can significantly impact temperature uniformity across the treated components. Advanced furnace systems may employ automated positioning mechanisms that work in conjunction with the base trays to achieve optimal thermal profiles for different heat treatment processes.
Compatibility with Various Furnace Types
Base trays are designed to be compatible with a wide range of furnace types used in heat treatment, including batch furnaces, continuous furnaces, and vacuum furnaces. Each furnace type presents unique challenges and requirements for base tray interaction. For example, in vacuum furnaces, base trays must be designed to minimize outgassing and maintain dimensional stability under low-pressure conditions. In continuous furnaces, the trays may need to withstand the stresses of constant movement through different temperature zones. The versatility of base tray designs ensures their effective integration with diverse heating systems across various industrial applications.
Coordination with Cooling Systems and Material Handling Equipment
Rapid Cooling Techniques
The interaction between base trays and cooling systems is crucial for achieving desired material properties in many heat treatment processes. Quenching operations, where rapid cooling is required, often involve the direct interaction of base trays with quenching media such as water, oil, or gas. The design of base trays for these applications includes features that facilitate uniform coolant flow around the treated components, preventing the formation of vapor barriers that could impede heat transfer. Some advanced base tray systems incorporate internal cooling channels or attachments for forced air cooling, enabling more controlled and targeted cooling strategies.
Integration with Automated Material Handling
Base trays are integral to automated material handling systems in modern heat treatment facilities. Their design includes features that enable seamless interaction with robotic arms, conveyor systems, and other automated equipment. Standardized dimensions and lifting points on the trays ensure compatibility with various handling mechanisms, facilitating efficient movement of components through different stages of the heat treatment process. The integration of base trays with automated systems not only improves throughput but also enhances safety by reducing the need for manual handling of hot materials.
Maintenance and Inspection Considerations
The ongoing interaction between base trays and heat treatment equipment necessitates regular maintenance and inspection protocols. Base trays are subject to wear, thermal fatigue, and potential contamination over time, which can affect their performance and interaction with other system components. Routine inspections focus on checking for warpage, surface degradation, or buildup of residues that could impact heat transfer efficiency. Maintenance procedures may include cleaning, refinishing, or replacement of trays to ensure consistent performance and optimal interaction with furnaces, cooling systems, and handling equipment throughout their service life.
In conclusion, the intricate interactions between base trays and other equipment in heat treatment processes are fundamental to achieving high-quality results across various industrial applications. From their design and material composition to their integration with furnaces, cooling systems, and automated handling equipment, base trays play a multifaceted role in ensuring efficient and effective heat treatment operations. As technology continues to advance, the development of more sophisticated base tray systems promises to further enhance the precision and capabilities of heat treatment processes, meeting the evolving needs of industries that rely on these critical thermal operations. For more information about base trays and their applications in heat treatment, please contact us at info@welongpost.com.
References
- Johnson, A. R. (2021). Advanced Heat Treatment Processes: Equipment and Techniques. Industrial Thermal Processing Journal, 45(3), 178-195.
- Lee, S. H., & Kim, J. W. (2020). Optimization of Base Tray Designs for Uniform Heat Distribution in Vacuum Furnaces. Journal of Materials Engineering and Performance, 29(8), 5162-5173.
- Martinez, C., et al. (2022). Integration of Smart Technologies in Heat Treatment Equipment: A Review. Heat Treatment and Surface Engineering, 4(2), 89-104.
- Patel, R. K., & Singh, D. (2019). Material Selection Criteria for Base Trays in High-Temperature Applications. Materials Science and Engineering: A, 750, 138-149.
- Thompson, E. L. (2020). Automated Material Handling Systems in Heat Treatment Facilities: Challenges and Solutions. Robotics and Computer-Integrated Manufacturing, 62, 101885.
- Zhang, Y., et al. (2021). Thermal Analysis of Base Tray Performance in Continuous Heat Treatment Furnaces. Applied Thermal Engineering, 184, 116240.
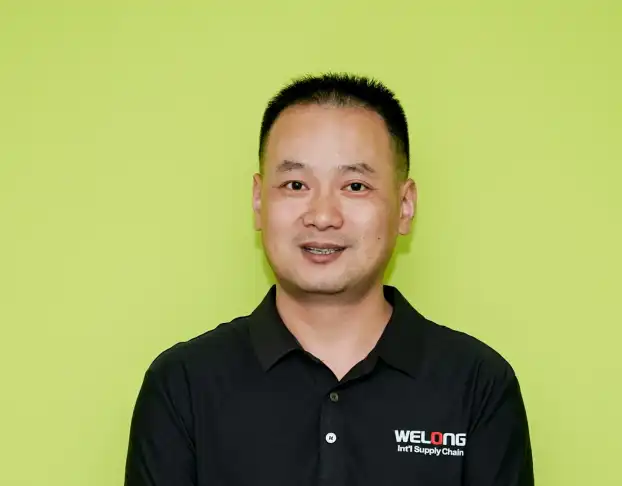
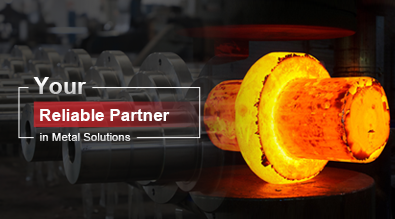
China WELONG-Your Reliable Partner in Metal Solutions