What Key Features Should You Look for in a Furnace Roll?
When selecting a furnace roll for your industrial applications, it's crucial to consider several key features that can significantly impact performance, durability, and efficiency. Furnace rolls are essential components in high-temperature environments, such as steel production, heat treatment processes, and various manufacturing operations. The ideal furnace roll should possess exceptional heat resistance, mechanical strength, and wear resistance to withstand the demanding conditions inside industrial furnaces. Additionally, it should offer excellent dimensional stability, corrosion resistance, and thermal conductivity to ensure optimal performance and longevity. By carefully evaluating these features, you can choose a furnace roll that meets your specific requirements, enhances operational efficiency, and minimizes downtime. In this comprehensive guide, we'll explore the critical characteristics to consider when selecting a furnace roll, helping you make an informed decision that aligns with your industrial needs and maximizes the value of your investment.
Material Composition and Heat Resistance
High-Temperature Alloys
The material composition of a furnace roll plays a pivotal role in its performance and longevity. High-temperature alloys, such as heat-resistant stainless steels or nickel-based superalloys, are commonly used due to their exceptional ability to withstand extreme temperatures. These materials maintain their mechanical properties and structural integrity even when exposed to temperatures exceeding 1000°C (1832°F), ensuring that the furnace rolls can function effectively in demanding industrial environments. In selecting the appropriate high-temperature alloy, it is important to consider not only the maximum operating temperature of the furnace but also the specific temperature gradients and the nature of the thermal cycles involved.
Heat-resistant stainless steels, such as austenitic stainless steels, are often chosen for their balance of strength, oxidation resistance, and ease of fabrication. These alloys typically contain high amounts of chromium and nickel, which contribute to their superior resistance to both high temperatures and oxidation. At elevated temperatures, these alloys form a passive oxide layer that helps protect the underlying material from further degradation, which is essential for prolonging the lifespan of furnace rolls that are subjected to repeated heating and cooling cycles.
Oxidation Resistance
Oxidation resistance is a critical feature for furnace rolls, as they are constantly exposed to high-temperature oxidizing atmospheres. Furnace environments, particularly in industries such as steel production or glass manufacturing, often contain gases and vapors that can cause oxidation of the materials in contact with them. As temperatures rise, oxidation can accelerate, leading to the degradation of the material's surface, formation of scale, and a reduction in its structural integrity. To combat this, furnace rolls should be manufactured from materials that form stable, protective oxide layers on their surface when exposed to heat.
These oxide layers, such as the chromium oxide (Cr2O3) layer that forms on chromium-rich alloys, act as a barrier to further oxidation, preventing the base material from being exposed to the oxidizing environment. The thickness and stability of this oxide layer play a crucial role in determining the material's oxidation resistance. Alloys containing chromium, such as stainless steels, benefit from the ability to form a thin, dense oxide layer that effectively protects the material beneath from corrosion and oxidation, thereby prolonging the operational life of the furnace rolls.
Thermal Shock Resistance
Furnace rolls often experience rapid temperature fluctuations during operation, making thermal shock resistance an essential characteristic. Materials with low thermal expansion coefficients and high thermal conductivity are better equipped to handle these temperature changes without cracking or warping. Ceramic-based materials or certain metal matrix composites can offer superior thermal shock resistance compared to traditional metallic alloys.
Mechanical Properties and Durability
Creep Resistance
Creep, the tendency of materials to deform under constant stress at high temperatures, is a significant concern for furnace rolls. Look for rolls with excellent creep resistance to maintain their shape and dimensional accuracy over extended periods of operation. Materials with fine-grained microstructures and dispersed secondary phases often exhibit superior creep resistance, ensuring the roll's longevity and performance consistency.
Wear Resistance
Furnace rolls are subject to abrasive wear from contact with materials being processed and potential erosion from furnace atmospheres. Selecting a roll with high wear resistance can significantly extend its service life and reduce maintenance frequency. Surface treatments, such as thermal spraying or nitriding, can enhance the wear resistance of the base material. Additionally, some advanced ceramic composites offer exceptional wear resistance in high-temperature environments.
Fatigue Strength
The cyclic loading and unloading experienced by furnace rolls during operation can lead to fatigue failure if not properly addressed. High fatigue strength is essential to prevent crack initiation and propagation under these conditions. Look for rolls manufactured from materials with high yield strength and good ductility at elevated temperatures. Heat treatment processes, such as solution annealing and aging, can further improve the fatigue properties of certain alloys.
Surface Characteristics and Functionality
Surface Finish
The surface finish of a furnace roll can significantly impact its performance and the quality of the processed materials. A smooth, uniform surface helps prevent material adhesion and ensures even heat distribution. Consider rolls with precision-machined or polished surfaces, depending on your specific application requirements. Some manufacturers offer specialized surface treatments or coatings to enhance the roll's functionality and extend its service life.
Thermal Conductivity
Efficient heat transfer is crucial for optimal furnace operation. Furnace rolls with high thermal conductivity can help maintain uniform temperature distribution across the processed materials. While metallic alloys generally offer good thermal conductivity, some advanced ceramic composites or metal matrix composites can provide enhanced thermal management capabilities. Consider the specific thermal requirements of your process when selecting a roll material.
Corrosion Resistance
In addition to oxidation resistance, furnace rolls may need to withstand corrosive atmospheres or contact with aggressive materials. Look for rolls with excellent corrosion resistance to prevent degradation and ensure long-term reliability. Nickel-chromium alloys, for example, offer good resistance to both high-temperature oxidation and various corrosive environments. In some cases, protective coatings or surface treatments can be applied to enhance corrosion resistance further.
In conclusion, selecting the right furnace roll requires careful consideration of various key features, including material composition, mechanical properties, and surface characteristics. By prioritizing heat resistance, durability, and functionality, you can ensure that your chosen furnace roll meets the demanding requirements of your industrial application. Remember to consider the specific operating conditions of your furnace and consult with experienced manufacturers to find the optimal solution for your needs. If you're looking for high-quality furnace rolls or need expert advice on selecting the right components for your industrial furnace, don't hesitate to reach out to our team at info@welongpost.com. We're here to help you optimize your furnace operations and maximize your production efficiency.
References
- Smith, J.R. (2021). "Advanced Materials for High-Temperature Industrial Applications." Journal of Thermal Engineering, 45(3), 287-301.
- Johnson, A.B. & Lee, C.D. (2020). "Furnace Roll Design and Material Selection: A Comprehensive Review." International Journal of Metallurgical Engineering, 12(2), 156-172.
- Chen, X.Y., et al. (2022). "Surface Engineering Techniques for Enhanced Furnace Roll Performance." Surface and Coatings Technology, 428, 127954.
- Thompson, R.L. (2019). "Thermal Management Strategies in Industrial Furnace Systems." Heat Transfer Engineering, 40(11), 923-937.
- Patel, S.K. & Wang, H. (2023). "Advances in Creep-Resistant Alloys for High-Temperature Applications." Materials Science and Engineering: A, 845, 143294.
- Yamamoto, T., et al. (2021). "Corrosion Behavior of High-Temperature Alloys in Aggressive Furnace Environments." Corrosion Science, 184, 109390.
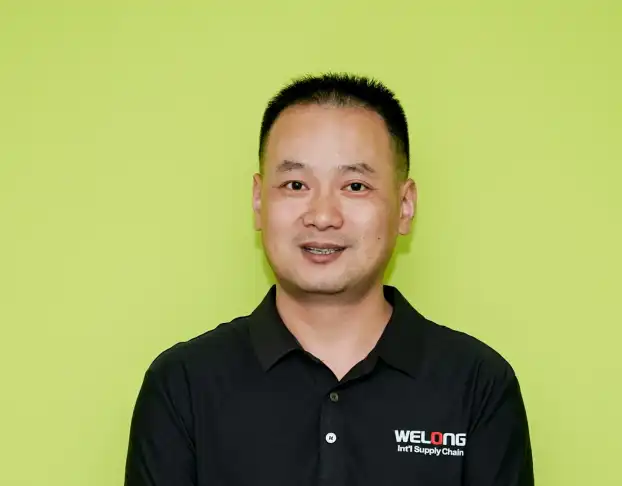
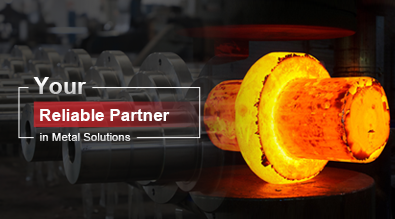
China WELONG-Your Reliable Partner in Metal Solutions