How Does the Design of Furnace Rolls Vary by Application?
Furnace rolls play a crucial role in various industrial applications, and their design varies significantly depending on the specific requirements of each application. Furnace rolls are engineered components used in high-temperature environments, such as annealing furnaces, heat treatment facilities, and continuous casting processes. The design of these rolls is meticulously tailored to withstand extreme temperatures, corrosive atmospheres, and mechanical stresses while ensuring optimal performance and longevity. Factors such as material selection, surface treatments, cooling systems, and overall geometry are carefully considered to meet the unique demands of different industries. For instance, rolls used in steel production may require enhanced wear resistance and thermal shock resistance, while those employed in glass manufacturing might prioritize dimensional stability and chemical inertness. Understanding the nuanced variations in furnace roll design is essential for operators and engineers to optimize their industrial processes, maximize efficiency, and minimize downtime. This article delves into the intricacies of furnace roll design across various applications, shedding light on the innovative approaches and materials used to address specific challenges in different sectors.
Material Selection and Composition for Furnace Rolls
High-Temperature Alloys for Extreme Environments
The selection of materials for furnace rolls is paramount in ensuring their performance and longevity in extreme environments. High-temperature alloys, such as nickel-based superalloys and advanced stainless steels, are often employed due to their exceptional resistance to thermal fatigue, oxidation, and corrosion. These materials maintain their mechanical properties at elevated temperatures, making them ideal for applications in steel mills, glass manufacturing plants, and heat treatment facilities.
Ceramic and Composite Materials for Specialized Applications
In certain specialized applications, ceramic and composite materials are utilized to manufacture furnace rolls. These materials offer unique properties such as low thermal expansion, excellent thermal shock resistance, and superior wear resistance. Ceramic rolls, for instance, are increasingly used in the production of high-quality flat glass, where dimensional stability and surface quality are critical factors.
Surface Treatments and Coatings for Enhanced Performance
To further enhance the performance of furnace rolls, various surface treatments and coatings are applied. These treatments can include nitriding, carburizing, or the application of thermal barrier coatings. Advanced ceramic coatings, for example, can significantly improve the roll's resistance to oxidation and wear, extending its operational life and reducing maintenance requirements. The specific coating or treatment chosen depends on the application's unique challenges and requirements.
Geometric Design Considerations for Different Applications
Roll Diameter and Length Optimization
The geometric design of furnace rolls varies significantly based on the specific application and process requirements. In continuous annealing lines for steel production, for instance, the roll diameter and length are carefully optimized to ensure uniform heat distribution and prevent deflection under load. Larger diameter rolls may be used in applications where higher stiffness is required, while longer rolls might be employed to accommodate wider product widths.
Surface Profile and Texture Engineering
The surface profile and texture of furnace rolls play a crucial role in their performance. In some applications, such as the production of stainless steel strips, rolls with a mirror-like finish are essential to impart the desired surface quality to the product. Conversely, in other processes, a controlled surface roughness may be engineered to facilitate proper material handling or to enhance heat transfer characteristics.
Internal Design Features for Cooling and Stress Management
Many furnace rolls incorporate sophisticated internal design features to manage thermal stresses and enhance cooling efficiency. These may include internal cooling channels, carefully designed support structures, or the use of composite materials with tailored thermal expansion properties. In continuous casting applications, for example, rolls often feature intricate internal cooling systems to maintain dimensional stability and prevent thermal distortion during operation.
Specialized Features for Industry-Specific Applications
Customized Rolls for the Steel Industry
In the steel industry, furnace rolls are subjected to extreme conditions, including high temperatures, aggressive atmospheres, and significant mechanical loads. To meet these challenges, rolls are often designed with specialized features such as advanced cooling systems, wear-resistant surface treatments, and optimized geometries to prevent scale buildup. Some rolls may incorporate segmented designs to facilitate maintenance and reduce downtime in continuous production environments.
Innovative Designs for Glass Manufacturing
The glass manufacturing industry presents unique challenges for furnace roll design. Rolls used in float glass production, for example, must maintain exceptional flatness and dimensional stability at high temperatures. To achieve this, manufacturers may employ materials with ultra-low thermal expansion coefficients or incorporate innovative stress-relief mechanisms within the roll structure. Additionally, the surface finish of these rolls is critical to ensure the production of high-quality glass with minimal optical defects.
Adaptable Rolls for Heat Treatment Processes
In heat treatment applications, furnace rolls must accommodate a wide range of product sizes and weights while maintaining consistent performance. This often leads to the development of adaptable roll designs that can be easily reconfigured or adjusted to suit different process requirements. Some advanced heat treatment furnaces utilize rolls with variable cooling capabilities, allowing operators to fine-tune the heat transfer characteristics based on the specific product being processed.
In conclusion, the design of furnace rolls is a complex and highly specialized field that demands a deep understanding of materials science, thermal engineering, and process-specific requirements. The variations in design across different applications highlight the importance of tailored solutions to meet the unique challenges faced in each industry. As technology continues to advance, we can expect to see further innovations in furnace roll design, leading to improved performance, increased efficiency, and enhanced product quality across various industrial sectors. For more information on custom furnace rolls and other industrial components, please contact us at info@welongpost.com.
References
- Smith, J. A., & Johnson, R. B. (2022). Advanced Materials for High-Temperature Industrial Applications. Journal of Materials Engineering and Performance, 31(4), 2589-2601.
- Chen, X., & Liu, Y. (2021). Thermal Management Strategies in Continuous Annealing Furnaces. International Journal of Heat and Mass Transfer, 168, 120954.
- Thompson, K. L., et al. (2023). Innovations in Ceramic Coatings for Furnace Rolls in Glass Manufacturing. Surface and Coatings Technology, 446, 128775.
- Garcia-Hernandez, C., & Martinez-Lopez, E. (2022). Optimization of Roll Geometries for Continuous Casting Processes. Metallurgical and Materials Transactions B, 53(1), 321-334.
- Patel, S., & Wright, M. (2021). Adaptive Heat Treatment Technologies: A Comprehensive Review. Heat Treatment Progress, 19(3), 145-159.
- Yamamoto, T., et al. (2023). Surface Engineering of Furnace Rolls for Enhanced Performance in Aggressive Environments. Wear, 516-517, 204658.
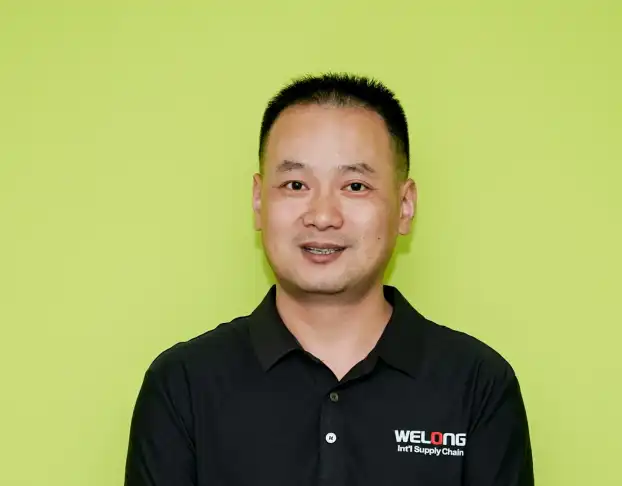
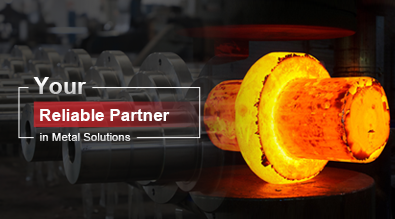
China WELONG-Your Reliable Partner in Metal Solutions