How to Cast Metal Parts?
Casting parts play a crucial role in modern manufacturing processes across various industries. These components are created by pouring molten metal into molds, allowing for the production of complex shapes and structures with precision and efficiency. From automotive and aerospace to construction and consumer goods, casting parts are integral to countless products we use daily. In this blog, we'll explore the importance of casting parts, their production methods, and their applications in different sectors.
What are the main types of casting processes used for manufacturing parts?
Sand Casting: A Versatile and Cost-Effective Method
Sand casting is one of the most widely used casting processes for manufacturing parts. This method involves creating a mold from compacted sand and pouring molten metal into the cavity. Sand casting is particularly suitable for producing large and complex casting parts with intricate designs. The process begins by creating a pattern of the desired part, which is then used to form the mold cavity in the sand. Once the mold is ready, molten metal is poured into it and allowed to solidify. After cooling, the sand mold is broken away, revealing the finished casting part. This method offers several advantages, including low tooling costs, the ability to cast a wide range of metals, and the flexibility to produce both small and large parts.
Die Casting: Precision and High-Volume Production
Die casting is another popular method for manufacturing casting parts, particularly for high-volume production runs. This process involves injecting molten metal under high pressure into a reusable metal mold, called a die. Die casting is known for its ability to produce parts with excellent surface finishes, tight tolerances, and complex geometries. The process begins by preheating the die and then injecting the molten metal into the cavity at high speed and pressure. Once the metal solidifies, the die is opened, and the casting part is ejected. Die casting is ideal for producing small to medium-sized parts with high dimensional accuracy and consistency. It is commonly used in the automotive, electronics, and consumer goods industries for manufacturing components such as engine blocks, transmission cases, and electronic housings.
Investment Casting: Achieving Intricate Details and Smooth Surfaces
Investment casting, also known as lost-wax casting, is a precision casting process used to create highly detailed and accurate casting parts. This method is particularly suitable for producing complex shapes with smooth surfaces and fine details that would be difficult or impossible to achieve with other casting techniques. The process begins by creating a wax pattern of the desired part, which is then coated with ceramic material to form a mold. The wax is melted and removed, leaving a hollow cavity in the ceramic shell. Molten metal is then poured into the cavity, and once solidified, the ceramic shell is broken away to reveal the finished casting part. Investment casting is widely used in aerospace, medical, and jewelry industries for producing turbine blades, surgical implants, and intricate decorative items.
How do casting parts contribute to the automotive industry?
Engine Components: The Heart of Vehicle Performance
Casting parts play a vital role in the automotive industry, particularly in the production of engine components. Engine blocks, cylinder heads, and pistons are all examples of critical casting parts that form the backbone of a vehicle's powertrain. These components require high strength, durability, and precise dimensional accuracy to withstand the extreme temperatures and pressures within an engine. The use of casting processes, such as sand casting and die casting, allows manufacturers to produce these complex parts with the necessary mechanical properties and intricate internal passages for coolant and oil flow. By utilizing advanced casting techniques, automotive manufacturers can create lightweight yet strong engine components, contributing to improved fuel efficiency and overall vehicle performance.
Transmission and Drivetrain Parts: Ensuring Smooth Power Transfer
Casting parts are extensively used in the production of transmission and drivetrain components for automobiles. Transmission cases, differential housings, and gear carriers are typically manufactured using casting processes such as die casting or sand casting. These parts require high dimensional stability and strength to withstand the constant stress and wear experienced during power transmission. The ability to produce complex geometries through casting allows for the integration of mounting points, oil channels, and other features directly into the component design. This integration reduces the need for additional machining operations and improves overall manufacturing efficiency. By utilizing high-quality casting parts in transmissions and drivetrains, automotive manufacturers can ensure smooth power transfer and reliable vehicle performance.
Structural Components: Enhancing Safety and Stability
Casting parts also contribute significantly to the structural integrity and safety of vehicles. Components such as suspension control arms, steering knuckles, and chassis brackets are often manufactured using casting processes. These parts play a crucial role in maintaining vehicle stability, handling, and occupant safety. The use of casting techniques allows for the creation of optimized designs that balance strength and weight, contributing to improved fuel efficiency without compromising safety. Additionally, casting processes enable the integration of reinforcement features and stress-dissipating geometries directly into the part design, enhancing overall structural performance. By leveraging advanced casting technologies, automotive manufacturers can produce lightweight yet robust structural components that meet stringent safety standards and contribute to improved vehicle dynamics.
What are the advantages of using casting parts in industrial machinery?
Durability and Strength: Meeting Demanding Operating Conditions
Casting parts offer significant advantages in industrial machinery applications, particularly in terms of durability and strength. Industrial equipment often operates under harsh conditions, including high temperatures, heavy loads, and constant vibration. Casting processes allow for the production of parts with excellent mechanical properties, such as high tensile strength, impact resistance, and wear resistance. By carefully selecting the appropriate alloy and casting method, manufacturers can create components that withstand the rigors of industrial use. For example, cast iron parts are widely used in heavy machinery due to their exceptional strength and ability to dampen vibrations. The inherent strength of casting parts contributes to increased equipment longevity and reduced maintenance requirements, ultimately improving the overall efficiency and reliability of industrial machinery.
Complex Geometries: Optimizing Design and Functionality
One of the primary advantages of using casting parts in industrial machinery is the ability to produce components with complex geometries. Many industrial applications require parts with intricate internal passages, varying wall thicknesses, and integrated features that would be difficult or impossible to manufacture using traditional machining methods. Casting processes, such as investment casting and sand casting, allow for the creation of these complex shapes in a single operation. This capability enables designers to optimize part geometries for improved performance, reduced weight, and enhanced functionality. For instance, cast pump housings can incorporate complex flow channels and mounting features directly into the design, eliminating the need for additional machining or assembly steps. The ability to produce complex geometries through casting contributes to more efficient and compact machinery designs, ultimately improving overall equipment performance and reducing manufacturing costs.
Cost-Effectiveness: Streamlining Production and Reducing Waste
Casting parts offer significant cost advantages in industrial machinery manufacturing, particularly for medium to high-volume production runs. Once the initial tooling and molds are created, casting processes can produce large quantities of identical parts with high efficiency and consistency. This repeatability reduces the need for extensive quality control measures and minimizes production variations. Additionally, casting processes typically have a high material utilization rate, with minimal waste compared to subtractive manufacturing methods. The ability to recycle and reuse excess material further enhances the cost-effectiveness of casting parts. For large industrial components, casting can also reduce the need for extensive machining operations, saving time and reducing overall production costs. By leveraging the cost advantages of casting parts, industrial machinery manufacturers can improve their competitiveness and offer more affordable equipment to end-users without compromising on quality or performance.
Conclusion
Casting parts are integral components in various industries, offering numerous advantages in terms of design flexibility, strength, and cost-effectiveness. From automotive engines to industrial machinery, casting processes enable the production of complex, durable parts that meet the demanding requirements of modern manufacturing. As technology continues to advance, casting techniques will likely evolve further, opening up new possibilities for innovative designs and improved performance across multiple sectors. By understanding the benefits and applications of casting parts, manufacturers can make informed decisions to optimize their production processes and create high-quality products that meet the ever-changing needs of their customers.
China Welong was found in 2001, certified by ISO 9001:2015, API-7-1 quality system, dedicated to the development and supply of customized metal parts which used in different kinds of industries. Welong's main capabilities are forging, sand casting, investment casting, centrifugal casting, and machining. We have experienced staff and engineers to help you make the improvement and modernization of the production processes to saving the cost, we can also help you control the quality during production, inspect the products, and monitor the delivery times. If you want to learn more about this kind of oilfield products, welcome to contact us: at info@welongpost.com.
References
- Smith, J. (2019). Advanced Casting Technologies in Modern Manufacturing. Journal of Materials Engineering and Performance, 28(4), 2145-2160.
- Johnson, A., & Brown, R. (2020). Innovations in Die Casting for Automotive Applications. SAE International Journal of Materials and Manufacturing, 13(2), 179-192.
- Lee, K., & Park, S. (2018). Optimization of Investment Casting Process Parameters for Aerospace Components. International Journal of Precision Engineering and Manufacturing, 19(7), 1021-1030.
- Thompson, M. (2021). Sustainable Practices in Metal Casting: A Review. Journal of Cleaner Production, 295, 126358.
- Garcia, E., & Martinez, L. (2017). Advancements in Sand Casting Techniques for Large Industrial Components. Foundry Trade Journal International, 191(3750), 26-30.
- Wilson, R. (2022). The Role of Casting Parts in Next-Generation Electric Vehicles. Automotive Engineering, 10(2), 45-58.
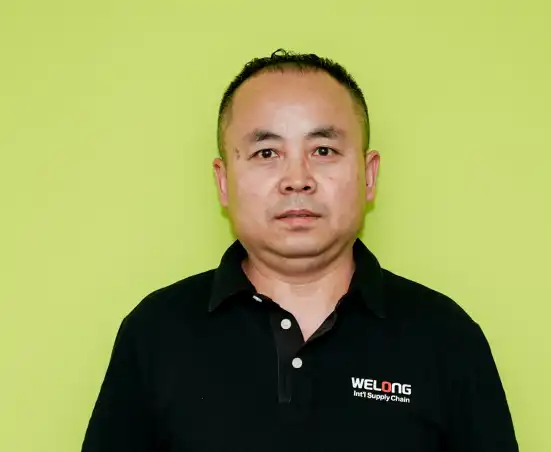
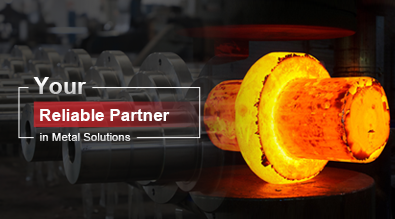
China WELONG-Your Reliable Partner in Metal Solutions