What are the Components of Metal Casting?
Metal casting is a fundamental manufacturing process that has been used for thousands of years to create intricate and complex metal components. This process involves pouring molten metal into a mold, allowing it to solidify, and then removing the finished product. Understanding the components of metal casting is essential for anyone involved in the manufacturing industry or interested in the production of metal parts. In this blog, we'll explore the key elements that make up the metal casting process and discuss their importance in creating high-quality metal components.
What are the main types of metal casting processes?
Sand Casting
Sand casting is one of the most widely used metal casting processes, particularly for producing metal components. This method involves creating a mold using compacted sand mixed with binders. The sand mold is formed around a pattern, which is then removed, leaving a cavity in the shape of the desired component. Molten metal is then poured into this cavity and allowed to solidify. Sand casting is versatile and can be used for a wide range of metals, including iron, steel, aluminum, and copper alloys. It's particularly suitable for producing large and complex metal components with intricate details. The sand mold can be easily broken apart after the casting has solidified, making it ideal for both small and large production runs. One of the advantages of sand casting is its ability to produce metal components with excellent surface finishes and dimensional accuracy.
Investment Casting
Investment casting, also known as lost-wax casting, is a precision metal casting process used to create highly detailed and accurate metal components. This method begins with creating a wax pattern of the desired component. The wax pattern is then coated with ceramic material to form a shell. Once the ceramic shell has hardened, the wax is melted out, leaving a precise cavity. Molten metal is then poured into this cavity, filling the intricate details of the mold. After the metal has solidified, the ceramic shell is broken away, revealing the finished metal component. Investment casting is particularly useful for producing complex shapes with smooth surfaces and fine details that would be difficult or impossible to achieve with other casting methods. It's commonly used in industries such as aerospace, automotive, and medical device manufacturing, where precision and quality are paramount in metal components.
Die Casting
Die casting is a metal casting process that involves forcing molten metal under high pressure into a mold cavity. The mold, also known as a die, is typically made from hardened tool steel and can produce thousands of identical metal components before requiring replacement. This process is ideal for high-volume production of small to medium-sized metal parts with excellent surface finishes and dimensional accuracy. Die casting is particularly well-suited for non-ferrous metals such as aluminum, zinc, copper, magnesium, and lead alloys. The high pressure used in die casting results in metal components with dense, uniform grain structures and superior mechanical properties. This process also allows for the production of thin-walled parts and complex geometries that would be challenging to achieve with other casting methods. Die casting is widely used in industries such as automotive, electronics, and consumer goods manufacturing, where large quantities of precise metal components are required.
What are the key materials used in metal casting?
Metals and Alloys
The choice of metals and alloys is crucial in metal casting, as it directly influences the properties and performance of the final metal components. Common metals used in casting include iron, steel, aluminum, copper, zinc, and magnesium. Each metal or alloy has its unique characteristics, such as strength, durability, corrosion resistance, and thermal conductivity. For instance, cast iron is known for its excellent wear resistance and ability to dampen vibrations, making it ideal for engine blocks and machine tool bases. Aluminum alloys are popular for their lightweight properties and corrosion resistance, often used in automotive and aerospace components. Steel castings offer high strength and toughness, suitable for heavy-duty applications in construction and mining equipment. The selection of the appropriate metal or alloy depends on factors such as the intended use of the component, required mechanical properties, cost considerations, and manufacturing constraints.
Molding Materials
Molding materials play a critical role in shaping the metal components during the casting process. The most common molding material is sand, which is used in various forms such as green sand, dry sand, and resin-bonded sand. Green sand, a mixture of silica sand, clay, and water, is widely used due to its versatility and cost-effectiveness. For more precise castings, chemically bonded sand molds or shell molds may be employed. In investment casting, ceramic slurry is used to create the mold, providing excellent surface finish and dimensional accuracy. Die casting utilizes metal molds, typically made from tool steel, which can withstand the high pressures and temperatures involved in the process. The choice of molding material affects not only the quality of the final metal components but also the production rate, cost, and environmental impact of the casting process.
Binders and Additives
Binders and additives are essential components in metal casting, particularly in sand casting processes. Binders are used to hold the sand particles together, giving the mold sufficient strength to withstand the pressure of molten metal. Common binders include clay for green sand molds, and chemical binders such as furan resins or phenolic urethanes for chemically bonded sand molds. Additives are incorporated into the molding materials to enhance various properties. For example, carbon additives can improve the surface finish of iron castings, while chromite sand can be added to prevent metal penetration in steel castings. In investment casting, additives in the ceramic slurry control its viscosity and drying characteristics. These binders and additives significantly influence the quality of the metal components, affecting properties such as surface finish, dimensional accuracy, and defect rates. Proper selection and control of these materials are crucial for producing high-quality metal castings consistently.
How do patterns and cores contribute to metal casting?
Pattern Design and Materials
Patterns are the replicas of the desired metal components used to create the mold cavity in sand casting processes. The design and material of the pattern are crucial factors that influence the quality and accuracy of the final casting. Patterns can be made from various materials, including wood, metal, plastics, or even 3D printed materials, depending on the production volume and required precision. Wood patterns are cost-effective for low-volume production, while metal patterns offer better durability for high-volume casting. The pattern design must account for factors such as shrinkage allowance, draft angles, and parting lines to ensure the metal components can be easily removed from the mold. Advanced pattern designs may incorporate features like cores prints, which create spaces for cores to be inserted, allowing for the creation of internal cavities in the metal components. The accuracy and surface finish of the pattern directly affect the quality of the final casting, making pattern design and material selection critical aspects of the metal casting process.
Core Making and Assembly
Cores are used in metal casting to create internal cavities or complex external features in metal components that would be difficult or impossible to form with the mold alone. Core making is a specialized process that involves creating these separate sand shapes, which are then placed into the mold before casting. The core material must be strong enough to withstand the pressure of the molten metal but also easily removable after casting. Common core materials include silica sand bonded with organic or inorganic binders. The core-making process can be manual or automated, depending on the complexity and production volume. Core assembly is a critical step in the mold preparation process, as the correct positioning of cores ensures the accurate formation of internal features in the metal components. Advances in 3D printing technology have also revolutionized core making, allowing for the production of complex, precision cores that were previously challenging to manufacture.
Pattern and Core Maintenance
Proper maintenance of patterns and cores is essential for ensuring consistent quality in metal components produced through casting. Patterns, especially those made from wood or plastic, can wear over time due to repeated use and exposure to molding materials. Regular inspection and repair of patterns are necessary to maintain dimensional accuracy and surface quality. This may involve recoating, refinishing, or even replacing pattern sections. Metal patterns, while more durable, may require periodic machining to maintain precise dimensions. Core boxes, used to create sand cores, also require regular maintenance to ensure the cores produced are consistent and accurate. Proper storage of patterns and cores is crucial to prevent damage from moisture, temperature fluctuations, or physical impacts. In high-volume production environments, implementing a systematic pattern and core maintenance program can significantly improve the overall quality and consistency of metal components, reduce defects, and extend the lifespan of these critical casting tools.
Conclusion
Understanding the components of metal casting is crucial for producing high-quality metal parts efficiently. From the various casting processes like sand casting, investment casting, and die casting to the selection of appropriate metals, molding materials, and additives, each element plays a vital role in shaping the final product. The design and maintenance of patterns and cores further contribute to the precision and complexity of the cast components. As technology advances, new techniques and materials continue to enhance the metal casting process, enabling the production of increasingly sophisticated and precise metal parts. By mastering these components, manufacturers can optimize their casting processes, reduce defects, and produce superior metal components for a wide range of industries.
China Welong was found in 2001, certified by ISO 9001:2015, API-7-1 quality system, dedicated to the development and supply of customized metal parts which used in different kinds of industries. Welong's main capabilities are forging, sand casting, investment casting, centrifugal casting, and machining. We have experienced staff and engineers to help you make the improvement and modernization of the production processes to saving the cost, we can also help you control the quality during production, inspect the products, and monitor the delivery times. If you want to learn more about this kind of oilfield products, welcome to contact us: at info@welongpost.com.
References
- Campbell, J. (2015). Complete Casting Handbook: Metal Casting Processes, Metallurgy, Techniques and Design. Butterworth-Heinemann.
- Beeley, P. (2001). Foundry Technology. Butterworth-Heinemann.
- Kalpakjian, S., & Schmid, S. R. (2014). Manufacturing Engineering and Technology. Pearson.
- ASM International. (2008). ASM Handbook, Volume 15: Casting. ASM International.
- Brown, J. R. (1999). Foseco Ferrous Foundryman's Handbook. Butterworth-Heinemann.
- Schey, J. A. (2000). Introduction to Manufacturing Processes. McGraw-Hill.
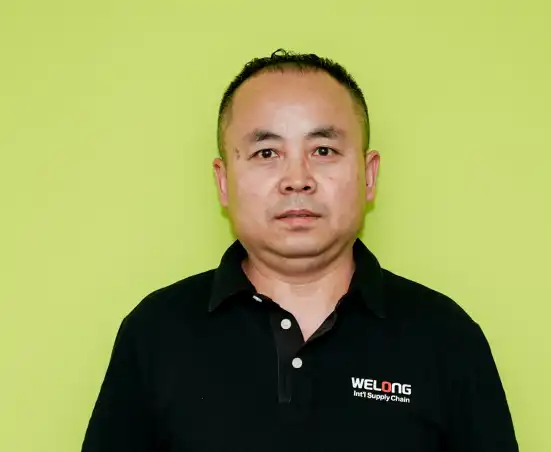
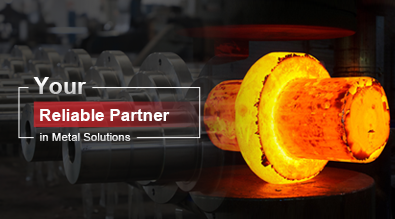
China WELONG-Your Reliable Partner in Metal Solutions