How to Cast Metal Parts From 3D Prints?
Casting is a fundamental manufacturing process that has been used for centuries to create complex metal parts and components. This blog will delve into the intricate world of casting, exploring various aspects of the process from initial design considerations to the final product. We'll examine different casting methods, discuss key factors that influence the quality of casting parts, and provide insights into the latest innovations in the industry.
What are the main types of casting processes used in manufacturing?
Sand Casting: The Versatile Foundation
Sand casting is one of the most widely used casting processes in manufacturing. This method involves creating a mold from sand and pouring molten metal into it. The versatility of sand casting allows for the production of a wide range of casting parts, from small components to large machinery parts. The process begins with creating a pattern, which is then used to form the mold cavity in sand. Once the mold is prepared, molten metal is poured into it and allowed to solidify. After cooling, the sand mold is broken away, revealing the cast part. Sand casting is particularly advantageous for producing parts with complex geometries and is cost-effective for both small and large production runs.
Die Casting: Precision and Speed
Die casting is a high-pressure casting process that involves forcing molten metal into a reusable metal mold, known as a die. This method is ideal for producing large quantities of small to medium-sized casting parts with excellent surface finishes and dimensional accuracy. The process begins with the creation of a custom-designed die, which is then mounted in a die casting machine. Molten metal is injected into the die at high pressure, rapidly filling the cavity and solidifying. Once cooled, the part is ejected from the die. Die casting is known for its ability to produce parts with thin walls, complex shapes, and fine details, making it popular in industries such as automotive and electronics manufacturing.
Investment Casting: Achieving Intricate Details
Investment casting, also known as lost-wax casting, is a process that excels in producing casting parts with high precision and intricate details. The process begins by creating a wax pattern of the desired part. This pattern is then coated with ceramic material to form a shell. Once the ceramic shell has hardened, the wax is melted out, leaving a hollow mold. Molten metal is then poured into this mold, filling the cavity and taking on the shape of the original wax pattern. After cooling and solidification, the ceramic shell is broken away to reveal the final cast part. Investment casting is particularly useful for creating parts with complex geometries, thin walls, and smooth surfaces, making it a popular choice in aerospace, medical, and jewelry industries.
How does material selection impact the quality of casting parts?
Influence of Metal Composition
The choice of metal alloy plays a crucial role in determining the properties and performance of casting parts. Different metals and alloys offer varying characteristics such as strength, durability, corrosion resistance, and thermal conductivity. For instance, aluminum alloys are often chosen for their lightweight properties and excellent corrosion resistance, making them ideal for automotive and aerospace applications. Cast iron, on the other hand, is known for its high compressive strength and wear resistance, making it suitable for heavy machinery components. The composition of the alloy can be fine-tuned to achieve specific properties, such as improved fluidity for better mold filling or enhanced mechanical properties for demanding applications. Understanding the relationship between material composition and the desired properties of the final casting parts is essential for achieving optimal results in the casting process.
Heat Treatment Considerations
Heat treatment is a critical post-casting process that can significantly influence the mechanical properties of casting parts. Different heat treatment methods, such as annealing, normalizing, and quenching, can be applied to modify the microstructure of the cast metal, thereby altering its strength, hardness, and ductility. For example, solution heat treatment followed by artificial aging can greatly enhance the strength and hardness of aluminum alloy castings. Similarly, normalizing can improve the uniformity of the microstructure in cast iron parts, leading to better machinability and more consistent properties. The choice of heat treatment process depends on the specific alloy used and the desired properties of the final casting parts. Proper heat treatment can help overcome some of the limitations inherent in the casting process, such as porosity or non-uniform cooling rates, resulting in higher quality and more reliable components.
Impurities and Inclusions Management
Managing impurities and inclusions is crucial for producing high-quality casting parts. Impurities can enter the metal during the melting process or from contaminants in the mold material. These unwanted elements can lead to defects in the final casting, such as porosity, reduced mechanical strength, or poor surface finish. To mitigate these issues, various techniques are employed in the casting process. For instance, degassing is used to remove dissolved gases from the molten metal, reducing the likelihood of gas porosity in the final casting. Filtration systems can be implemented to remove solid inclusions from the melt before it enters the mold. Additionally, careful control of the pouring temperature and cooling rate can help minimize the formation of harmful intermetallic compounds. By effectively managing impurities and inclusions, manufacturers can produce casting parts with improved structural integrity, better surface quality, and enhanced overall performance.
What are the latest innovations in casting technology?
3D Printing in Sand Casting
The integration of 3D printing technology into the sand casting process has revolutionized the way patterns and molds are created. Traditional methods of pattern making can be time-consuming and costly, especially for complex or one-off casting parts. 3D printing allows for rapid production of intricate sand molds and cores directly from digital designs, without the need for pattern equipment. This technology enables greater design freedom, faster prototyping, and the ability to produce highly complex geometries that would be challenging or impossible with conventional methods. 3D printed sand molds can achieve tighter tolerances and better surface finishes, resulting in higher quality casting parts. Moreover, this innovation has significantly reduced lead times and tooling costs, making it particularly beneficial for low-volume production runs and rapid prototyping in industries such as aerospace and automotive.
Simulation and Modeling Software
Advanced simulation and modeling software have become indispensable tools in modern casting processes. These powerful computational tools allow engineers to simulate the entire casting process virtually, from mold filling and solidification to predicting potential defects in the final casting parts. By using these simulations, manufacturers can optimize mold designs, gating systems, and process parameters before any physical casting takes place. This approach significantly reduces the need for trial-and-error in production, saving time and resources. Simulation software can predict issues such as shrinkage porosity, hot spots, and thermal stresses, enabling engineers to make informed decisions about mold design and process conditions. The result is a more efficient casting process, improved quality of casting parts, and reduced scrap rates. As these software tools continue to evolve, incorporating machine learning and AI, their predictive capabilities are becoming even more accurate and valuable to the casting industry.
In-Mold Sensors and Real-Time Monitoring
The implementation of in-mold sensors and real-time monitoring systems represents a significant advancement in casting technology. These systems allow for continuous monitoring of critical parameters during the casting process, such as temperature distribution, pressure, and mold filling dynamics. By embedding sensors directly into the mold, manufacturers can gather real-time data on the conditions inside the mold cavity as the metal solidifies. This information is crucial for ensuring consistent quality in casting parts and allows for immediate adjustments to process parameters if deviations are detected. Real-time monitoring also enables better traceability and quality control, as each casting can be associated with a complete set of process data. Additionally, the data collected over time can be analyzed to identify trends and opportunities for process improvement, leading to enhanced efficiency and reduced defect rates in the production of casting parts.
Conclusion
The casting process continues to evolve, driven by technological advancements and the ever-increasing demands for higher quality, more complex, and cost-effective components. From traditional methods like sand casting to innovative techniques involving 3D printing and real-time monitoring, the industry is constantly adapting to meet new challenges. The careful selection of materials, coupled with appropriate heat treatment and impurity management, plays a crucial role in determining the final properties of casting parts. As we look to the future, the integration of digital technologies, advanced simulations, and smart manufacturing principles promises to further enhance the capabilities and efficiency of casting processes, ensuring its continued relevance in modern manufacturing.
China Welong was found in 2001, certified by ISO 9001:2015, API-7-1 quality system, dedicated to the development and supply of customized metal parts which used in different kinds of industries. Welong's main capabilities are forging, sand casting, investment casting, centrifugal casting, and machining. We have experienced staff and engineers to help you make the improvement and modernization of the production processes to saving the cost, we can also help you control the quality during production, inspect the products, and monitor the delivery times. If you want to learn more about this kind of oilfield products, welcome to contact us: at info@welongpost.com.
References
- Campbell, J. (2015). Complete Casting Handbook: Metal Casting Processes, Metallurgy, Techniques and Design. Butterworth-Heinemann.
- Beeley, P. R. (2001). Foundry Technology. Butterworth-Heinemann.
- ASM International. (2008). ASM Handbook, Volume 15: Casting. ASM International.
- Stefanescu, D. M. (2015). Science and Engineering of Casting Solidification. Springer.
- Kalpakjian, S., & Schmid, S. R. (2014). Manufacturing Engineering and Technology. Pearson.
- Brown, J. R. (2000). Foseco Ferrous Foundryman's Handbook. Butterworth-Heinemann.
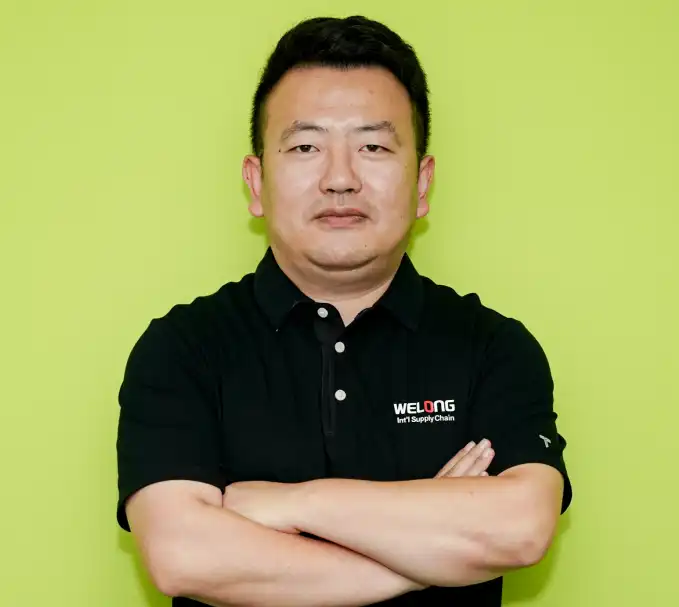
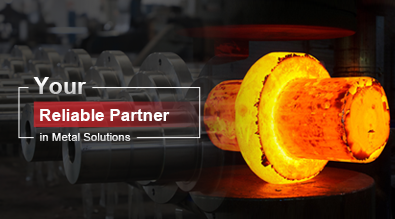
China WELONG-Your Reliable Partner in Metal Solutions