What are the Techniques of Precision Casting?
Precision casting, also known as investment casting or lost-wax casting, is a sophisticated manufacturing process used to create highly accurate and complex metal parts. This technique has been utilized for thousands of years and has evolved significantly with modern technology. In this blog post, we will explore the various techniques of precision casting, their applications, and the benefits they offer to manufacturers across different industries.
What are the main types of precision casting processes?
Investment Casting
Investment casting is one of the most widely used precision casting techniques. This process involves creating a wax pattern of the desired part, coating it with ceramic material to form a mold, melting out the wax, and then pouring molten metal into the cavity. Investment casting allows for the production of intricate parts with excellent surface finishes and dimensional accuracy. The process is particularly useful for creating components with complex geometries that would be difficult or impossible to manufacture using traditional machining methods. Industries such as aerospace, automotive, and medical device manufacturing heavily rely on investment casting for producing high-precision parts with tight tolerances.
Die Casting
Die casting is another precision casting technique that involves injecting molten metal into a reusable mold under high pressure. This process is ideal for producing large quantities of identical parts with excellent dimensional accuracy and surface finish. Die casting is commonly used in the automotive industry for manufacturing engine components, transmission housings, and structural parts. The process offers several advantages, including high production rates, excellent repeatability, and the ability to cast thin-walled sections. However, die casting is generally limited to non-ferrous metals such as aluminum, zinc, and magnesium alloys due to the high temperatures and pressures involved in the process.
Centrifugal Casting
Centrifugal casting is a precision casting technique that utilizes centrifugal force to distribute molten metal evenly within a rotating mold. This process is particularly effective for producing cylindrical or tubular parts with a high degree of accuracy and consistency. The centrifugal force helps to eliminate porosity and improve the overall density of the cast part. Centrifugal casting is commonly used in the production of pipes, tubes, and bushings for various industrial applications. The technique offers several advantages, including excellent material properties, uniform wall thickness, and the ability to cast parts with complex internal geometries.
How does precision casting differ from traditional casting methods?
Accuracy and Surface Finish
Precision casting techniques offer significantly higher accuracy and superior surface finish compared to traditional casting methods. The investment casting process, for example, can achieve tolerances as tight as ±0.05mm and surface finishes as smooth as 1.6 μm Ra. This level of precision is crucial for applications in industries such as aerospace and medical device manufacturing, where even minor deviations can have severe consequences. Traditional sand casting, on the other hand, typically produces parts with rougher surfaces and looser tolerances, often requiring extensive post-casting machining to achieve the desired specifications.
Complexity of Parts
One of the key advantages of precision casting is its ability to produce parts with complex geometries and intricate details. Investment casting, in particular, excels in creating components with undercuts, thin walls, and internal cavities that would be challenging or impossible to manufacture using conventional casting or machining techniques. This capability allows designers to optimize part geometries for performance and weight reduction without being constrained by manufacturing limitations. Traditional casting methods, such as sand casting, are generally limited in their ability to produce complex shapes and fine details, often resulting in simpler part designs or the need for assembly of multiple components.
Material Properties
Precision casting techniques often result in improved material properties compared to traditional casting methods. The controlled solidification and cooling rates achieved in processes like investment casting and centrifugal casting can lead to finer grain structures and more uniform mechanical properties throughout the part. Additionally, the reduced turbulence during mold filling in precision casting processes helps minimize the formation of inclusions and porosity, resulting in higher-quality castings. These improved material properties translate to better performance and longer service life for precision-cast components, making them ideal for critical applications in industries such as aerospace and automotive.
What are the key considerations when choosing a precision casting technique?
Part Geometry and Complexity
When selecting a precision casting technique, one of the primary considerations is the geometry and complexity of the part to be produced. Investment casting is particularly well-suited for components with intricate details, thin walls, and complex internal features. Die casting is more appropriate for parts with simpler geometries that require high production volumes. Centrifugal casting is ideal for cylindrical or tubular components with consistent wall thickness. The choice of casting technique should be based on the specific requirements of the part design and the ability of each process to achieve the desired features accurately and cost-effectively.
Production Volume and Cost
The production volume and associated costs play a crucial role in determining the most suitable precision casting technique. Investment casting generally has higher tooling costs but offers greater flexibility in terms of part design and material selection. It is often the preferred choice for low to medium production volumes or for parts that require frequent design changes. Die casting, on the other hand, has higher initial tooling costs but becomes more economical for high-volume production due to its faster cycle times and lower per-part costs. Centrifugal casting falls somewhere in between, offering a balance of flexibility and production efficiency for certain types of parts.
Material Selection
The choice of material is another critical factor in selecting the appropriate precision casting technique. Investment casting offers the widest range of material options, including ferrous and non-ferrous alloys, superalloys, and even some exotic metals. This versatility makes it suitable for a broad range of applications across various industries. Die casting is generally limited to non-ferrous alloys due to the high temperatures and pressures involved in the process. Centrifugal casting is commonly used for both ferrous and non-ferrous alloys but is particularly well-suited for materials that benefit from the centrifugal force during solidification, such as cast iron and bronze alloys.
Conclusion
Precision casting techniques offer manufacturers a powerful set of tools for producing high-quality, complex metal parts with excellent dimensional accuracy and surface finish. Whether through investment casting, die casting, or centrifugal casting, these methods provide unique advantages in terms of part geometry, material properties, and production efficiency. By carefully considering factors such as part complexity, production volume, and material requirements, manufacturers can select the most appropriate precision casting technique for their specific application. As technology continues to advance, precision casting will undoubtedly play an increasingly important role in the production of critical components across various industries.
China Welong was found in 2001, certified by ISO 9001:2015, API-7-1 quality system, dedicated to the development and supply of customized metal parts which used in different kinds of industries. Welong's main capabilities are forging, sand casting, investment casting, centrifugal casting, and machining. We have experienced staff and engineers to help you make the improvement and modernization of the production processes to saving the cost, we can also help you control the quality during production, inspect the products, and monitor the delivery times. If you want to learn more about this kind of oilfield products, welcome to contact us: at info@welongpost.com.
References
- Campbell, J. (2015). Complete Casting Handbook: Metal Casting Processes, Metallurgy, Techniques and Design. Butterworth-Heinemann.
- Beeley, P. R., & Smart, R. F. (1995). Investment Casting. Institute of Materials.
- Street, A. C. (1986). The Diecasting Book. Portcullis Press.
- Janco, N. (1992). Centrifugal Casting. American Foundrymen's Society.
- ASM International. (2008). ASM Handbook, Volume 15: Casting. ASM International.
- Kalpakjian, S., & Schmid, S. R. (2014). Manufacturing Engineering and Technology. Pearson.
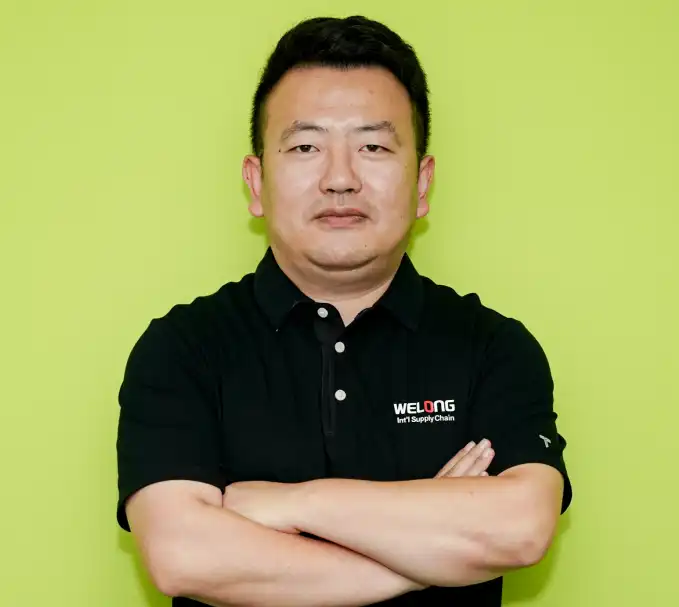
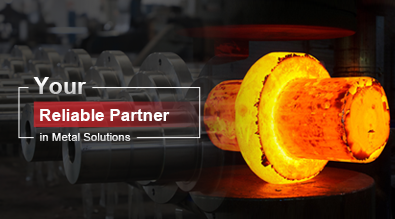
China WELONG-Your Reliable Partner in Metal Solutions