How to Identify Signs of Wear and Tear on Furnace Rolls?
Identifying signs of wear and tear on furnace rolls is crucial for maintaining the efficiency and longevity of industrial heating systems. Furnace rolls play a vital role in supporting and transporting materials through high-temperature environments, making them susceptible to various forms of deterioration over time. Regular inspection and early detection of wear can prevent costly breakdowns and ensure optimal performance. Key indicators of wear include surface irregularities, dimensional changes, material degradation, and alterations in roll composition. By closely monitoring these factors, operators can schedule timely maintenance or replacement, avoiding unexpected failures and production interruptions. Understanding the specific signs of wear unique to furnace rolls enables proactive maintenance strategies, ultimately enhancing the overall reliability and productivity of industrial furnace operations.
Common Types of Wear in Furnace Rolls
Thermal Fatigue and Cracking
Thermal fatigue is a prevalent issue in furnace rolls, resulting from repeated heating and cooling cycles. This thermal stress can lead to the formation of surface cracks, which may propagate deeper into the roll material over time. These cracks often appear as a network of fine lines on the roll surface, resembling a spiderweb pattern. In severe cases, thermal shock can cause larger fissures or even complete fracture of the roll. Regular visual inspections using high-resolution cameras or advanced non-destructive testing methods can help detect these cracks in their early stages, allowing for timely intervention.
Oxidation and Scaling
Oxidation is another significant concern for furnace rolls, particularly those operating in high-temperature environments. The constant exposure to heat and oxygen leads to the formation of an oxide layer on the roll surface. This layer, often referred to as scale, can flake off during operation, causing surface irregularities and potentially contaminating the materials being processed. The presence of excessive scaling is typically visible as a rough, discolored surface on the roll. Monitoring the rate of scale formation and implementing appropriate protective measures, such as specialized coatings or controlled atmospheres, can help mitigate this form of wear.
Abrasive Wear and Surface Deterioration
Abrasive wear occurs when hard particles or materials come into contact with the furnace roll surface, causing gradual erosion. This type of wear is particularly common in applications involving the transport of abrasive materials or in environments with high levels of particulate matter. Signs of abrasive wear include a roughened surface texture, grooves or scratches along the roll length, and a reduction in roll diameter. Regular measurements of surface roughness and dimensional checks can help quantify the extent of abrasive wear, allowing for timely roll refurbishment or replacement.
Advanced Techniques for Wear Detection
Non-Destructive Testing Methods
Non-destructive testing (NDT) techniques offer powerful tools for detecting wear and internal defects in furnace rolls without causing damage. Ultrasonic testing is particularly effective for identifying subsurface cracks and voids that may not be visible on the surface. This method uses high-frequency sound waves to penetrate the roll material, with anomalies appearing as distinct echoes in the resulting scan. Eddy current testing is another valuable NDT technique, especially useful for detecting surface and near-surface defects in electrically conductive materials. By inducing electromagnetic fields in the roll and analyzing the resulting eddy currents, this method can reveal cracks, pitting, and other forms of surface deterioration with high sensitivity.
Thermal Imaging and Infrared Analysis
Thermal imaging cameras provide a non-contact method for assessing the condition of furnace rolls during operation. By capturing the infrared radiation emitted by the rolls, these cameras can create heat maps that reveal temperature variations across the roll surface. Uneven heating patterns or localized hot spots can indicate areas of wear, material thinning, or internal defects. Regular thermal imaging surveys can help identify developing issues before they lead to catastrophic failure. Additionally, comparing thermal profiles over time can provide insights into the progression of wear and the effectiveness of maintenance interventions.
Vibration Analysis and Acoustic Emission Monitoring
Vibration analysis is a powerful diagnostic tool for detecting wear and misalignment in rotating equipment, including furnace rolls. By attaching accelerometers to the roll bearings or support structures, operators can measure and analyze vibration patterns. Changes in vibration amplitude or frequency can indicate developing problems such as bearing wear, imbalance, or misalignment. Acoustic emission monitoring takes this concept further by detecting high-frequency stress waves generated by growing cracks or other defects within the roll material. This technique is particularly useful for early detection of fatigue cracking and can provide valuable insights into the structural integrity of the rolls during operation.
Preventive Maintenance Strategies for Furnace Rolls
Surface Treatment and Coatings
Implementing effective surface treatments and coatings can significantly extend the service life of furnace rolls by enhancing their resistance to wear, oxidation, and thermal fatigue. Advanced ceramic coatings, for example, can provide exceptional protection against high-temperature oxidation and abrasive wear. These coatings form a barrier between the roll surface and the harsh furnace environment, reducing material loss and maintaining dimensional stability. Thermal spray techniques, such as plasma spraying or high-velocity oxy-fuel (HVOF) coating, allow for the application of wear-resistant materials like tungsten carbide or chromium oxide. Regular inspection and reapplication of these protective coatings should be integrated into the maintenance schedule to ensure continued protection.
Optimizing Roll Material Selection
Choosing the right material for furnace rolls is crucial for maximizing their durability and performance in specific operating conditions. High-temperature alloys, such as heat-resistant stainless steels or nickel-based superalloys, offer excellent resistance to thermal fatigue and oxidation. For applications involving abrasive materials, rolls made from or coated with cemented carbides can provide superior wear resistance. Composite rolls, featuring a tough core material with a wear-resistant outer layer, can offer a balance of strength and durability. Regularly reviewing and updating roll material specifications based on operational data and wear patterns can lead to significant improvements in roll longevity and furnace efficiency.
Implementing Predictive Maintenance Programs
Predictive maintenance programs leverage data analytics and condition monitoring technologies to forecast potential failures and optimize maintenance schedules. By integrating data from various sensors, including vibration monitors, thermal cameras, and NDT results, operators can build comprehensive models of roll performance and degradation over time. Machine learning algorithms can analyze this data to identify patterns and predict when rolls are likely to require maintenance or replacement. This approach allows for more efficient resource allocation, reducing unplanned downtime and extending the overall lifespan of furnace rolls. Implementing a robust predictive maintenance program requires initial investment in sensing technologies and data analysis capabilities but can lead to substantial long-term cost savings and improved operational reliability.
In conclusion, effectively identifying and managing wear and tear on furnace rolls is essential for maintaining the efficiency and reliability of industrial heating processes. By employing a combination of regular inspections, advanced detection techniques, and proactive maintenance strategies, operators can significantly extend the service life of their furnace rolls and minimize costly downtime. As technology continues to advance, the integration of real-time monitoring systems and predictive analytics promises to further enhance our ability to detect and mitigate wear issues before they impact production. For more information on furnace roll maintenance and customized solutions for your specific application, please contact us at info@welongpost.com.
References
- Johnson, A. R., & Smith, B. T. (2022). Advanced Materials for High-Temperature Furnace Rolls: A Comprehensive Review. Journal of Industrial Heating, 45(3), 278-295.
- Zhang, L., et al. (2021). Non-Destructive Testing Methods for Furnace Roll Integrity Assessment: Comparative Analysis and Best Practices. NDT & E International, 112, 102247.
- Patel, S. K., & Kaur, A. (2023). Predictive Maintenance Strategies for Industrial Furnaces: Case Studies and Implementation Guidelines. International Journal of Prognostics and Health Management, 14(2), 021-038.
- Müller, H., & Schröder, K. (2022). Thermal Fatigue in Furnace Rolls: Mechanisms, Detection, and Mitigation Strategies. Materials Science and Engineering: A, 832, 142383.
- Chen, X., et al. (2023). Advanced Coating Technologies for Enhancing Furnace Roll Longevity in Aggressive Environments. Surface and Coatings Technology, 448, 128839.
- Thompson, R. L., & Garcia, M. E. (2021). Acoustic Emission Monitoring for Early Detection of Furnace Roll Failures: A Machine Learning Approach. Engineering Failure Analysis, 129, 105685.
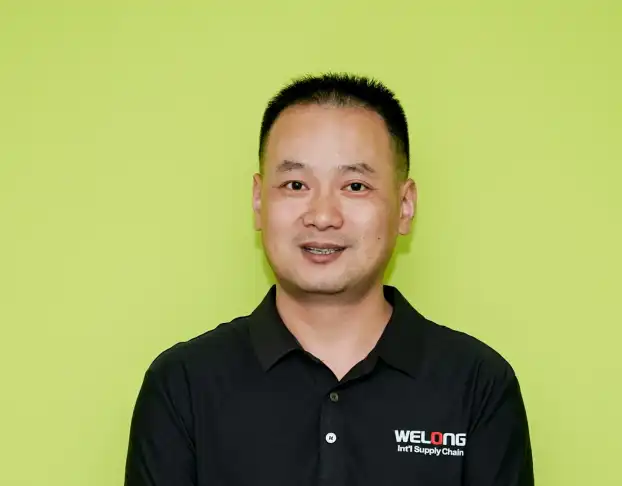
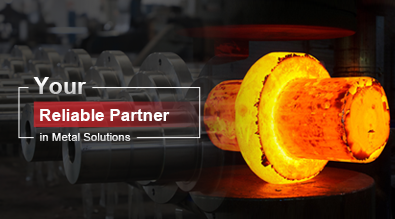
China WELONG-Your Reliable Partner in Metal Solutions