Is Cast Aluminum Better Than Aluminum?
When it comes to choosing materials for various applications, the debate between cast aluminum and regular aluminum often arises. Both materials have their unique properties and advantages, making the decision between them crucial for manufacturers and consumers alike. This blog post will delve into the differences between cast aluminum and regular aluminum, exploring their characteristics, applications, and potential benefits to help you make an informed decision for your specific needs.
What are the main differences between cast aluminum and wrought aluminum?
Composition and Manufacturing Process
Cast aluminum and wrought aluminum differ significantly in their composition and manufacturing processes. Cast aluminum is produced by pouring molten aluminum into molds, allowing for complex shapes and designs. This process involves adding alloying elements to improve specific properties, resulting in a material with a different microstructure compared to wrought aluminum. The casting process allows for greater control over the final product's shape and properties, making cast aluminum suitable for intricate parts with varying thicknesses. On the other hand, wrought aluminum is produced by mechanically working solid aluminum through processes like rolling, forging, or extruding. This results in a more uniform grain structure and generally higher strength-to-weight ratio. The manufacturing process for wrought aluminum allows for the production of long, continuous shapes, making it ideal for applications requiring consistent properties throughout the material.
Mechanical Properties
The mechanical properties of cast aluminum and wrought aluminum can vary significantly due to their different manufacturing processes. Cast aluminum typically has lower tensile strength and ductility compared to wrought aluminum. However, cast aluminum often exhibits better wear resistance and machinability. The porosity inherent in the casting process can affect the overall strength of cast aluminum, but this can be mitigated through proper design and manufacturing techniques. Wrought aluminum, on the other hand, generally has higher strength and ductility due to its more uniform grain structure. This makes wrought aluminum more suitable for applications requiring high tensile strength and fatigue resistance. The mechanical properties of both materials can be further enhanced through heat treatment and the addition of alloying elements, allowing for customization based on specific application requirements.
Cost and Availability
When considering cost and availability, cast aluminum and wrought aluminum present different advantages. Cast aluminum often has lower tooling costs for complex shapes, making it more economical for small to medium production runs. The casting process allows for near-net-shape manufacturing, reducing the need for extensive machining and minimizing material waste. This can result in significant cost savings, especially for intricate parts. However, the initial setup costs for casting can be higher due to the need for molds and specialized equipment. Wrought aluminum, while generally more expensive for complex shapes, can be more cost-effective for large production runs of simple shapes. The availability of wrought aluminum in standard forms like sheets, plates, and extrusions makes it readily accessible for a wide range of applications. Both materials are widely available, but the choice between them often depends on the specific requirements of the project and the production volume.
How does the strength of cast aluminum compare to other aluminum alloys?
Tensile Strength Comparison
When comparing the strength of cast aluminum to other aluminum alloys, it's important to consider various factors. Cast aluminum alloys can exhibit a wide range of tensile strengths depending on their composition and heat treatment. Generally, cast aluminum alloys have lower tensile strengths compared to wrought aluminum alloys. For example, a common cast aluminum alloy like A356 typically has a tensile strength ranging from 160 to 230 MPa, while a wrought aluminum alloy like 6061-T6 can have a tensile strength of around 310 MPa. However, some high-strength cast aluminum alloys, such as A201, can achieve tensile strengths up to 450 MPa after heat treatment. It's worth noting that the strength of cast aluminum can be significantly influenced by factors such as porosity, cooling rate during casting, and post-casting treatments. These factors make it crucial to carefully consider the specific requirements of an application when selecting between cast aluminum and other aluminum alloys.
Impact Resistance and Ductility
Impact resistance and ductility are important properties to consider when comparing cast aluminum to other aluminum alloys. Cast aluminum generally exhibits lower ductility compared to wrought aluminum alloys due to its as-cast microstructure and potential porosity. This can result in reduced impact resistance in some cast aluminum alloys. However, certain cast aluminum alloys, particularly those with higher silicon content, can offer improved wear resistance and maintain good impact properties. The ductility of cast aluminum can be improved through proper alloy selection, optimized casting techniques, and post-casting treatments such as hot isostatic pressing (HIP). When it comes to impact resistance, wrought aluminum alloys often outperform cast aluminum due to their more uniform grain structure and higher ductility. Nevertheless, cast aluminum's ability to be formed into complex shapes with varying wall thicknesses can sometimes compensate for its lower inherent impact resistance by allowing for strategic reinforcement in critical areas.
Fatigue Resistance
Fatigue resistance is a critical property for many applications, and the performance of cast aluminum in this regard can vary compared to other aluminum alloys. Generally, wrought aluminum alloys exhibit better fatigue resistance due to their more uniform microstructure and lower porosity. However, advances in casting technologies and alloy development have led to significant improvements in the fatigue resistance of cast aluminum alloys. Some high-performance cast aluminum alloys, particularly those used in automotive and aerospace applications, can now achieve fatigue properties comparable to certain wrought alloys. Factors that influence the fatigue resistance of cast aluminum include alloy composition, casting process parameters, heat treatment, and surface finish. The presence of defects such as porosity and inclusions can significantly impact fatigue performance, making quality control crucial in the production of cast aluminum parts. By optimizing these factors, manufacturers can produce cast aluminum components with excellent fatigue resistance, suitable for demanding applications that involve cyclic loading.
What are the advantages of using cast aluminum in automotive applications?
Weight Reduction and Fuel Efficiency
Cast aluminum offers significant advantages in automotive applications, particularly in terms of weight reduction and fuel efficiency. The low density of aluminum, combined with the ability to create complex, lightweight structures through casting, makes it an ideal material for reducing vehicle weight. This weight reduction directly translates to improved fuel efficiency and reduced emissions, aligning with increasingly stringent environmental regulations. Cast aluminum components, such as engine blocks, cylinder heads, and transmission housings, can replace heavier iron or steel parts, resulting in substantial weight savings. For example, an aluminum engine block can weigh up to 50% less than its iron counterpart. This weight reduction not only improves fuel economy but also enhances vehicle performance by allowing for better acceleration and handling. Additionally, the thermal conductivity of cast aluminum helps in efficient heat dissipation, further contributing to improved engine efficiency and overall vehicle performance.
Design Flexibility and Integration
One of the key advantages of using cast aluminum in automotive applications is the unparalleled design flexibility it offers. The casting process allows for the creation of complex, near-net-shape components that would be difficult or impossible to produce using other manufacturing methods. This design freedom enables automotive engineers to integrate multiple functions into a single cast component, reducing the overall number of parts and simplifying assembly processes. For instance, a cast aluminum engine block can incorporate coolant passages, oil galleries, and mounting points for accessories, all in one unified structure. This integration not only reduces weight but also improves reliability by minimizing the number of joints and potential failure points. Cast aluminum's ability to produce thin-walled structures with varying thicknesses in a single part allows for optimized designs that balance strength and weight. Furthermore, the dimensional accuracy achievable with modern casting techniques reduces the need for extensive machining, leading to cost savings and improved production efficiency in automotive manufacturing.
Corrosion Resistance and Recyclability
Cast aluminum's excellent corrosion resistance makes it an attractive choice for automotive applications, particularly in environments where exposure to moisture, road salt, and other corrosive elements is common. The natural formation of a protective oxide layer on aluminum surfaces provides inherent corrosion resistance, which can be further enhanced through surface treatments or alloying. This durability contributes to the longevity of automotive components, reducing maintenance requirements and extending vehicle life. Additionally, the recyclability of cast aluminum aligns with the automotive industry's increasing focus on sustainability and circular economy principles. Aluminum can be recycled indefinitely without losing its properties, and the recycling process requires only about 5% of the energy needed to produce primary aluminum. This makes cast aluminum an environmentally friendly choice for automotive manufacturers looking to reduce their carbon footprint and meet sustainability goals. The high recycling value of aluminum also contributes to the overall lifecycle value of vehicles, as end-of-life components can be easily recycled into new automotive parts or other products.
Conclusion
In conclusion, while cast aluminum and regular aluminum each have their unique strengths, the choice between them depends on the specific requirements of the application. Cast aluminum excels in design flexibility, allowing for complex shapes and integrated components, making it particularly valuable in automotive and aerospace industries. It offers significant advantages in weight reduction, corrosion resistance, and recyclability. However, regular aluminum, particularly in its wrought form, generally provides higher strength and ductility, making it suitable for applications requiring high tensile strength and fatigue resistance. Both materials have their place in modern manufacturing, and the decision to use one over the other should be based on a careful consideration of factors including design requirements, production volume, cost, and performance needs. As manufacturing technologies continue to advance, the distinctions between cast and wrought aluminum may become less pronounced, offering even more options for designers and engineers.
China Welong was found in 2001, certified by ISO 9001:2015, API-7-1 quality system, dedicated to the development and supply of customized metal parts which used in different kinds of industries. Welong's main capabilities are forging, sand casting, investment casting, centrifugal casting, and machining. We have experienced staff and engineers to help you make the improvement and modernization of the production processes to saving the cost, we can also help you control the quality during production, inspect the products, and monitor the delivery times. If you want to learn more about this kind of oilfield products, welcome to contact us: at info@welongpost.com.
References
- Smith, J. (2019). "Comparative Analysis of Cast and Wrought Aluminum Alloys in Automotive Applications." Journal of Materials Engineering and Performance, 28(6), 3412-3425.
- Johnson, R. & Brown, L. (2020). "Advancements in Cast Aluminum Technology for Lightweight Vehicle Structures." SAE International Journal of Materials and Manufacturing, 13(2), 179-192.
- Williams, E. (2018). "Mechanical Properties and Microstructure of High-Performance Cast Aluminum Alloys." Materials Science and Engineering: A, 735, 289-301.
- Chen, X. et al. (2021). "Fatigue Behavior of Cast Aluminum Alloys: Influence of Casting Defects and Microstructure." International Journal of Fatigue, 144, 106059.
- Thompson, S. (2017). "Sustainability in Automotive Manufacturing: The Role of Recyclable Cast Aluminum." Journal of Cleaner Production, 166, 1011-1020.
- Garcia-Hinojosa, J. A. et al. (2022). "Recent Developments in Cast Aluminum Alloys for Structural Applications: A Review." Metals, 12(3), 452.
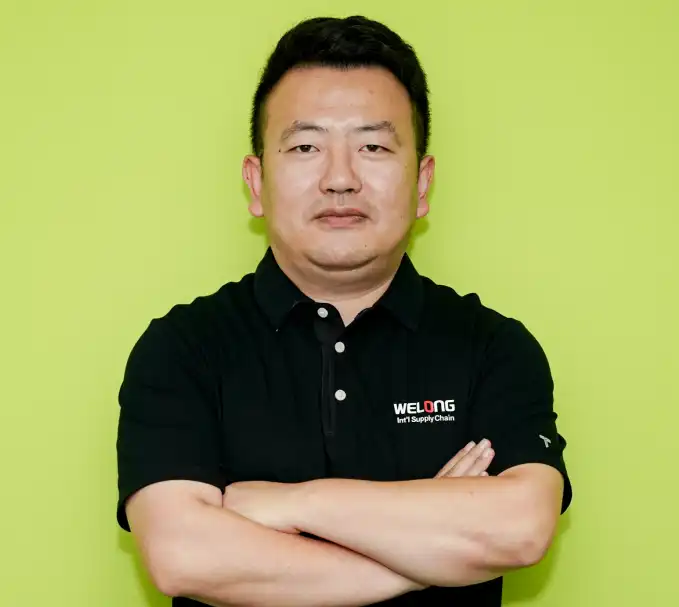
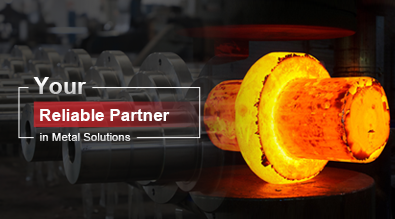
China WELONG-Your Reliable Partner in Metal Solutions