Surface Finish Options for Metal Spare Parts
When it comes to manufacturing metal spare parts, the surface finish is a crucial aspect that can significantly impact both the functionality and aesthetics of the final product. Various surface finish options are available for metal spare parts, each offering unique characteristics and benefits. This blog post will explore different surface finish techniques, their applications, and how they can enhance the performance and appearance of metal spare parts.
What are the most common surface finish options for metal spare parts?
Polishing
Polishing is a widely used surface finish option for metal spare parts, particularly in industries where aesthetics and smoothness are essential. This process involves removing a thin layer of material from the surface using abrasive materials, resulting in a smooth and reflective finish. Polishing can be performed manually or with automated equipment, depending on the size and complexity of the metal spare parts. For precision components, such as bearings or valve parts, polishing helps reduce friction and improve overall performance. Additionally, polished surfaces are easier to clean and maintain, making them ideal for applications in the food and pharmaceutical industries where hygiene is paramount. The level of polish can be customized to achieve different levels of reflectivity, from a satin finish to a mirror-like appearance, allowing manufacturers to tailor the surface finish to specific requirements of metal spare parts.
Brushing
Brushing is another popular surface finish option for metal spare parts, particularly in applications where a uniform, non-reflective appearance is desired. This process involves using abrasive brushes or wheels to create fine, parallel lines on the surface of the metal. Brushed finishes are often applied to stainless steel spare parts used in architectural applications, appliances, and industrial equipment. The brushed texture not only enhances the visual appeal of metal spare parts but also helps to conceal minor scratches and imperfections that may occur during use. This makes brushed finishes particularly suitable for high-traffic areas or components that are frequently handled. Additionally, the texture created by brushing can improve the adhesion of paints or coatings, making it an excellent choice for metal spare parts that require further surface treatments. The direction and pattern of the brushing can be customized to achieve different visual effects, allowing for greater flexibility in design and aesthetics.
Anodizing
Anodizing is an electrochemical process that creates a durable, corrosion-resistant oxide layer on the surface of metal spare parts, particularly those made from aluminum. This surface finish option not only enhances the appearance of the parts but also significantly improves their wear resistance and longevity. The anodized layer can be dyed in various colors, allowing for customization and color coding of metal spare parts. This is particularly useful in industries where part identification is crucial, such as aerospace or automotive manufacturing. Anodizing also provides excellent electrical insulation properties, making it ideal for metal spare parts used in electronic applications. The thickness of the anodized layer can be controlled, allowing manufacturers to tailor the surface finish to specific performance requirements. Additionally, anodized surfaces are more resistant to fading and discoloration compared to painted surfaces, ensuring that metal spare parts maintain their appearance over time, even in harsh environments.
How do different surface finishes affect the performance of metal spare parts?
Corrosion Resistance
The choice of surface finish can significantly impact the corrosion resistance of metal spare parts, which is crucial for components exposed to harsh environments or corrosive substances. For instance, electroplating with materials like zinc or nickel can provide excellent corrosion protection for steel spare parts. This process involves depositing a thin layer of metal onto the surface of the part, creating a barrier against corrosive elements. Similarly, passivation treatments for stainless steel spare parts can enhance their natural corrosion resistance by removing free iron from the surface and creating a protective oxide layer. In marine or offshore applications, where metal spare parts are constantly exposed to saltwater and humid conditions, specialized coatings like epoxy or polyurethane can be applied to provide long-lasting protection against corrosion. The appropriate surface finish can significantly extend the lifespan of metal spare parts, reducing maintenance costs and improving overall equipment reliability.
Wear Resistance
Surface finishes play a crucial role in enhancing the wear resistance of metal spare parts, particularly for components subjected to frequent friction or abrasion. Hard chrome plating, for example, is widely used in the automotive and aerospace industries to improve the wear resistance of engine components and hydraulic cylinders. This process creates a hard, smooth surface that can withstand high levels of wear and tear. For metal spare parts used in high-temperature applications, thermal spraying techniques like plasma spraying can be employed to create wear-resistant ceramic coatings. These coatings not only protect the underlying metal from wear but also provide thermal insulation. In some cases, surface hardening treatments like nitriding or carburizing can be used to increase the hardness of the metal surface without affecting the core properties of the spare part. By selecting the appropriate surface finish, manufacturers can significantly extend the service life of metal spare parts, reducing the frequency of replacements and minimizing downtime in industrial applications.
Friction Reduction
Certain surface finishes are specifically designed to reduce friction in metal spare parts, which is crucial for components in moving assemblies or those that come into contact with other parts. For instance, the application of dry film lubricants like molybdenum disulfide or PTFE can significantly reduce friction and prevent galling in threaded fasteners or sliding components. These coatings provide a low coefficient of friction even in the absence of liquid lubricants, making them ideal for metal spare parts used in vacuum or high-temperature environments. Another approach to friction reduction is the use of superfinishing techniques, which can create extremely smooth surfaces on bearings and gears, minimizing friction and improving energy efficiency. In some cases, textured surfaces created through laser etching or chemical etching can be used to create micro-reservoirs for lubricants, enhancing the lubrication properties of metal spare parts. By reducing friction, these surface finishes not only improve the performance of metal spare parts but also contribute to energy savings and extended component life in various industrial applications.
What factors should be considered when choosing a surface finish for metal spare parts?
Environmental Conditions
When selecting a surface finish for metal spare parts, it's crucial to consider the environmental conditions in which the parts will operate. For components exposed to outdoor environments, UV-resistant finishes or powder coatings might be necessary to prevent degradation and maintain appearance. In marine or coastal applications, where metal spare parts are exposed to salt spray and high humidity, specialized anti-corrosion coatings or stainless steel alloys with enhanced corrosion resistance might be required. For parts used in high-temperature environments, such as in furnaces or exhaust systems, ceramic coatings or heat-resistant alloys might be more suitable. In chemical processing plants, where metal spare parts may come into contact with corrosive substances, chemical-resistant coatings or materials like titanium or high-nickel alloys might be necessary. Additionally, for parts used in food processing or pharmaceutical industries, FDA-approved finishes that are easy to clean and sanitize should be considered. By carefully evaluating the environmental conditions, manufacturers can choose surface finishes that ensure the longevity and reliable performance of metal spare parts in their intended applications.
Functional Requirements
The functional requirements of metal spare parts play a significant role in determining the most appropriate surface finish. For parts that require high precision and minimal friction, such as bearings or hydraulic components, super-finished or lapped surfaces might be necessary to achieve the required tolerances and smooth operation. In applications where electrical conductivity is crucial, such as in electrical connectors or grounding components, finishes that maintain or enhance conductivity, like silver or gold plating, might be preferred. For parts that need to dissipate heat efficiently, such as heat sinks or engine components, finishes that increase surface area or improve thermal conductivity, like anodizing with specific pore structures, could be beneficial. In applications where parts need to be easily identified or traced, laser etching or engraving might be used to add serial numbers or barcodes without affecting the surface properties. For metal spare parts used in optical systems, highly reflective finishes or precisely controlled surface roughness might be required to achieve the desired optical properties. By carefully considering the functional requirements, manufacturers can select surface finishes that optimize the performance of metal spare parts in their specific applications.
Cost and Production Volume
The cost implications and production volume of metal spare parts are crucial factors in selecting an appropriate surface finish. For high-volume production of relatively low-cost parts, economical finishing methods like tumbling or mass finishing might be preferred to achieve a uniform surface finish quickly and cost-effectively. On the other hand, for high-value, precision components produced in smaller quantities, more expensive finishing processes like precision grinding or hand polishing might be justified to achieve the required surface quality. In some cases, the initial cost of applying a more durable finish, such as hard chrome plating or PVD coating, might be higher but can result in long-term cost savings due to extended part life and reduced maintenance. For prototype or small batch production of metal spare parts, versatile finishing methods like bead blasting or chemical etching might be preferred due to their flexibility and lower setup costs. Additionally, the cost of any necessary pre-treatment or post-treatment processes should be considered when evaluating different surface finish options. By balancing the cost considerations with the required performance characteristics and production volume, manufacturers can select the most cost-effective surface finish solution for their metal spare parts while meeting quality and functional requirements.
Conclusion
Selecting the appropriate surface finish for metal spare parts is a critical decision that can significantly impact their performance, durability, and overall value. From polishing and brushing to advanced coatings and treatments, each surface finish option offers unique benefits and considerations. By carefully evaluating factors such as environmental conditions, functional requirements, and production volumes, manufacturers can choose the most suitable surface finish to enhance the quality and longevity of their metal spare parts. As technology continues to advance, new surface finish options are likely to emerge, offering even greater possibilities for optimizing the performance and appearance of metal components across various industries.
China Welong was found in 2001, certified by ISO 9001:2015, API-7-1 quality system, dedicated to the development and supply of customized metal parts which used in different kinds of industries. Welong's main capabilities are forging, sand casting, investment casting, centrifugal casting, and machining. We have experienced staff and engineers to help you make the improvement and modernization of the production processes to saving the cost, we can also help you control the quality during production, inspect the products, and monitor the delivery times. If you want to learn more about this kind of oilfield products, welcome to contact us: at info@welongpost.com.
References
- Smith, J. (2019). Advanced Surface Finishing Techniques for Metal Components. Journal of Materials Engineering and Performance, 28(4), 2145-2160.
- Johnson, A. & Brown, T. (2020). Corrosion Protection Strategies for Metal Spare Parts in Harsh Environments. Corrosion Science, 165, 108412.
- Lee, S. et al. (2018). Influence of Surface Finishes on the Wear Resistance of Aerospace-grade Aluminum Alloys. Wear, 400-401, 62-69.
- Wilson, R. (2021). Cost-Effective Surface Finishing Methods for High-Volume Production of Metal Spare Parts. International Journal of Advanced Manufacturing Technology, 112(5), 1523-1537.
- García-Hernández, C. et al. (2020). Sustainable Surface Finishing Processes for Metal Components in the Automotive Industry. Journal of Cleaner Production, 252, 119851.
- Thompson, D. & White, E. (2019). Selecting Optimal Surface Finishes for Medical Device Components: A Comprehensive Guide. Medical Device and Diagnostic Industry, 41(3), 44-51.
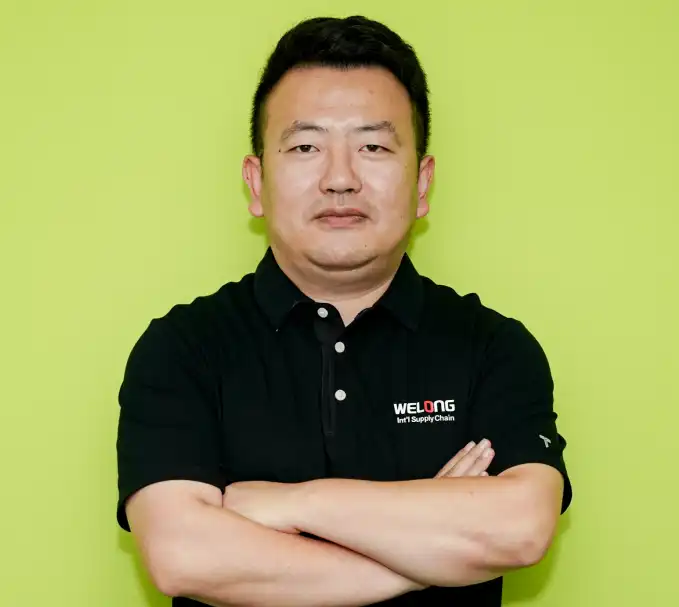
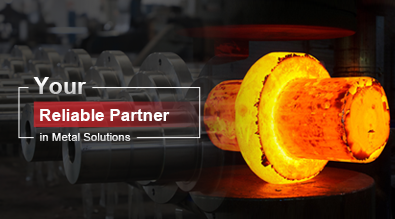
China WELONG-Your Reliable Partner in Metal Solutions