The Manufacturability for Spun and Rollformed Sheet Metal Components
In the realm of metal fabrication, the manufacturability of spun and rollformed sheet metal components plays a crucial role in various industries. These processes offer unique advantages in creating precise, cost-effective, and versatile metal parts. This blog explores the intricacies of spinning and rollforming techniques, their applications, and the factors that influence the manufacturability of sheet metal components.
What are the key differences between spun and rollformed sheet metal components?
Spinning Process for Sheet Metal Components
Sheet metal spinning, also known as metal spinning or spin forming, is a metalworking process that involves shaping a flat metal disc or tube into a axisymmetric part. This process utilizes a lathe-like machine where a metal blank is rotated at high speeds while a tool applies pressure to form the desired shape. Spinning is particularly effective for creating circular or conical components with smooth contours. The process allows for the production of complex shapes with minimal material waste, making it ideal for prototyping and small to medium production runs. Metal components produced through spinning often exhibit excellent structural integrity and surface finish, making it a preferred method for manufacturing items such as lampshades, cookware, and satellite dishes.
Rollforming Process for Sheet Metal Components
Rollforming is a continuous bending operation in which a long strip of metal, typically coiled steel, is passed through consecutive sets of rolls, each performing an incremental part of the bend. This process is highly efficient for producing constant-profile parts with long lengths. Rollforming is well-suited for high-volume production of metal components such as structural framing, gutters, and automotive parts. The process offers several advantages, including consistent part geometry, minimal material waste, and the ability to form both simple and complex cross-sections. Additionally, rollforming can incorporate in-line operations such as punching, cutting, and welding, further enhancing its efficiency in manufacturing metal components.
Material Considerations for Spun and Rollformed Components
The choice of material significantly impacts the manufacturability of spun and rollformed sheet metal components. For spinning, materials with good formability and ductility are preferred, such as aluminum, copper, and certain grades of steel. The thickness and hardness of the metal sheet also play crucial roles in determining the feasibility and quality of the spun component. In rollforming, material selection is equally important, with considerations including yield strength, tensile strength, and formability. High-strength steels and aluminum alloys are commonly used in rollforming applications. The material's spring-back characteristics must be taken into account to achieve the desired final shape of the metal components. Both processes require careful material selection to ensure optimal performance, durability, and cost-effectiveness of the finished products.
How does the design impact the manufacturability of sheet metal components?
Design Considerations for Spun Metal Components
When designing spun metal components, several factors must be considered to ensure optimal manufacturability. The depth-to-diameter ratio is a critical aspect, as it determines the feasibility of forming the desired shape without material failure. Generally, a depth-to-diameter ratio of 0.5 or less is preferred for most materials. Wall thickness uniformity is another crucial consideration, as maintaining consistent thickness throughout the spun part can be challenging. Designers must also account for the minimum bend radius to prevent material cracking or tearing during the spinning process. Additionally, the inclusion of features such as flanges, beads, or steps in the design can enhance the structural integrity of the spun metal components while potentially complicating the manufacturing process.
Design Principles for Rollformed Metal Components
Designing for rollforming requires a thorough understanding of the process limitations and capabilities. The cross-sectional profile of the component is a primary consideration, as it directly impacts the number of forming stations required and the overall complexity of the rollforming line. Symmetrical profiles are generally easier to produce and result in more stable parts. The bend radius is another critical factor, with larger radii typically being easier to form and less likely to cause material stress or cracking. Designers should also consider the inclusion of stiffening features, such as ribs or embossments, to enhance the structural properties of the rollformed metal components. Furthermore, the design should account for potential spring-back and provide allowances for secondary operations such as welding or assembly.
Balancing Aesthetics and Functionality in Sheet Metal Design
Achieving a balance between aesthetics and functionality is crucial when designing sheet metal components for spinning or rollforming. While these processes can produce parts with excellent surface finishes, certain design elements may impact both the visual appeal and the structural integrity of the components. For spun parts, the choice of tooling and forming techniques can influence the final surface texture and the presence of tool marks. In rollforming, the design of bends and corners can affect both the appearance and the strength of the component. Designers must consider how surface treatments, such as painting or powder coating, will interact with the formed metal surfaces. Additionally, the incorporation of decorative elements or branding features must be carefully planned to ensure they do not compromise the manufacturability or performance of the metal components.
What are the latest advancements in spun and rollformed sheet metal manufacturing?
Automation and Robotics in Sheet Metal Forming
The integration of automation and robotics has significantly advanced the manufacturability of spun and rollformed sheet metal components. In metal spinning, computer-controlled lathes and robotic arms have improved precision and repeatability, allowing for more complex shapes and tighter tolerances. These automated systems can adjust spinning parameters in real-time, optimizing the process for different materials and geometries. In rollforming, advanced control systems and servo-driven rolls enable quick changeovers and the production of variable cross-sections within a single run. Robotic handling systems have also enhanced the efficiency of loading, unloading, and secondary operations, reducing labor costs and improving safety. These technological advancements have not only increased productivity but also expanded the range of metal components that can be manufactured using spinning and rollforming techniques.
Advanced Materials and Coatings for Metal Components
The development of advanced materials and coatings has opened new possibilities in the manufacturability of spun and rollformed sheet metal components. High-strength, lightweight alloys are now being used to produce components with improved performance characteristics while reducing overall weight. Nano-structured materials and metal matrix composites are pushing the boundaries of what can be achieved in terms of strength-to-weight ratios and corrosion resistance. In the realm of coatings, advancements in plasma spraying and physical vapor deposition (PVD) techniques allow for the application of ultra-thin, highly durable coatings that enhance the surface properties of metal components. These coatings can improve wear resistance, reduce friction, and provide protection against harsh environments, expanding the application range of spun and rollformed parts in industries such as aerospace and automotive.
Digital Twin Technology in Sheet Metal Manufacturing
The adoption of digital twin technology is revolutionizing the manufacturability of spun and rollformed sheet metal components. A digital twin is a virtual representation of the physical manufacturing process, allowing engineers to simulate and optimize production before it begins. In metal spinning, digital twins can predict material behavior under various forming conditions, helping to identify potential issues such as wrinkling or thinning before they occur in the actual process. For rollforming, digital twin models can simulate the entire production line, including material flow, forming sequences, and stress distributions. This technology enables manufacturers to fine-tune tooling designs, adjust process parameters, and predict part quality with unprecedented accuracy. By leveraging digital twins, companies can reduce development time, minimize material waste, and improve the overall quality and consistency of their metal components.
Conclusion
The manufacturability of spun and rollformed sheet metal components continues to evolve with advancements in technology and materials science. Both processes offer unique advantages in producing high-quality, cost-effective metal parts for various industries. As we've explored, factors such as material selection, design considerations, and emerging technologies play crucial roles in determining the feasibility and efficiency of manufacturing these components. By leveraging automation, advanced materials, and digital simulation tools, manufacturers can push the boundaries of what's possible in sheet metal forming, creating innovative solutions for complex engineering challenges. As the industry progresses, we can expect further improvements in precision, efficiency, and sustainability in the production of spun and rollformed sheet metal components.
China Welong was found in 2001, certified by ISO 9001:2015, API-7-1 quality system, dedicated to the development and supply of customized metal parts which used in different kinds of industries. Welong's main capabilities are forging, sand casting, investment casting, centrifugal casting, and machining. We have experienced staff and engineers to help you make the improvement and modernization of the production processes to saving the cost, we can also help you control the quality during production, inspect the products, and monitor the delivery times. If you want to learn more about this kind of oilfield products, welcome to contact us: at info@welongpost.com.
References
- Smith, J. D. (2018). Advanced Techniques in Sheet Metal Spinning. Journal of Manufacturing Processes, 32(1), 45-58.
- Johnson, A. R., & Brown, L. M. (2019). Rollforming: Principles and Applications. International Journal of Metal Forming, 12(4), 567-582.
- Lee, K. S., et al. (2020). Material Considerations for High-Performance Spun and Rollformed Components. Materials Science and Engineering: A, 780, 139185.
- Wilson, R. T. (2017). Design Optimization for Rollformed Structural Profiles. Journal of Constructional Steel Research, 138, 775-785.
- Chen, X., & Zhang, Y. (2021). Digital Twin Technology in Sheet Metal Manufacturing: A Comprehensive Review. Journal of Intelligent Manufacturing, 32(4), 1115-1134.
- Thompson, P. L. (2019). Advancements in Automation for Metal Spinning Processes. Robotics and Computer-Integrated Manufacturing, 58, 262-273.
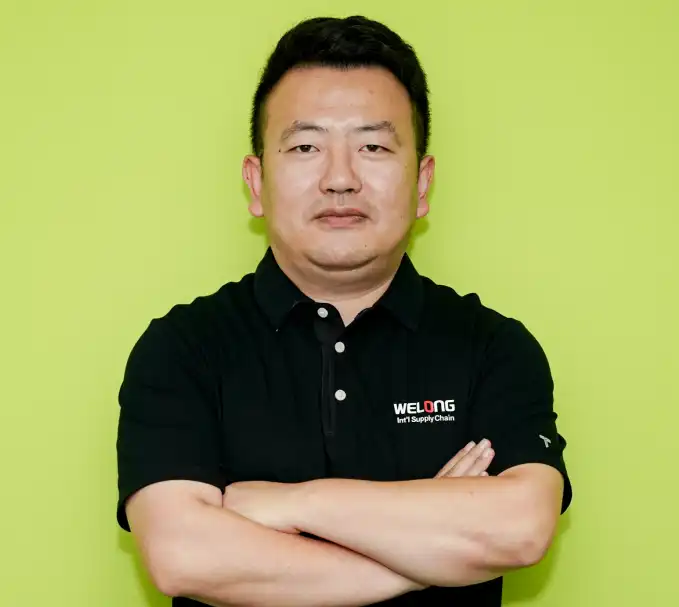
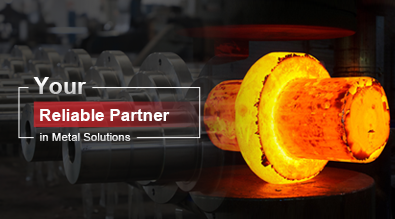
China WELONG-Your Reliable Partner in Metal Solutions