What Are Light Gauge Metal Components Typically Fastened Together With?
Light gauge metal components are widely used in various industries, from construction to manufacturing. These components are thin, lightweight, and versatile, making them ideal for a range of applications. However, to create stable and durable structures, these components need to be fastened together securely. In this blog post, we'll explore the various methods and fasteners used to join light gauge metal components, discussing their advantages, applications, and best practices.
What Are the Most Common Fasteners Used for Light Gauge Metal Components?
Self-Drilling Screws
Self-drilling screws are one of the most popular fasteners for light gauge metal components. These screws feature a sharp point and cutting threads that allow them to drill their own hole as they are driven into the metal. This eliminates the need for pre-drilling, saving time and labor costs. Self-drilling screws are particularly effective for joining thin metal sheets or profiles, as they create a tight connection without damaging the surrounding material. When using self-drilling screws for metal components, it's essential to choose the appropriate length and thread type for the specific application. The screw should be long enough to penetrate both pieces of metal being joined, but not so long that it protrudes excessively on the other side. Additionally, the thread design should match the thickness and hardness of the metal being fastened to ensure optimal holding power.
Rivets
Rivets are another common fastening method for light gauge metal components. These permanent fasteners consist of a smooth cylindrical shaft with a head on one end. To install a rivet, it is inserted into pre-drilled holes in the metal components, and then the tail end is deformed using a specialized tool. This creates a second head, effectively clamping the metal pieces together. Rivets are particularly useful for applications where access to both sides of the joint is possible, and a permanent, vibration-resistant connection is desired. When selecting rivets for metal components, it's crucial to consider factors such as the thickness of the materials being joined, the load-bearing requirements, and the environmental conditions the fastener will be exposed to. Different types of rivets, such as solid, blind, or pop rivets, may be more suitable for specific applications.
Clinching
Clinching is a mechanical joining process that doesn't require additional fasteners or consumables. Instead, it uses a special tool to deform the metal components, creating an interlocking joint. This method is particularly effective for thin sheet metal and can be used to join dissimilar metals. Clinching offers several advantages for fastening light gauge metal components, including speed, cost-effectiveness, and the ability to create clean, aesthetically pleasing joints without protruding fasteners. When implementing clinching for metal components, it's important to consider the material properties, thickness, and required joint strength. The clinching process may need to be optimized for different metal alloys or thicknesses to ensure a strong and reliable connection. Additionally, the location and spacing of clinched joints should be carefully planned to distribute loads evenly and maintain the structural integrity of the assembly.
How Do Different Environmental Factors Affect the Choice of Fasteners for Metal Components?
Corrosion Resistance
When selecting fasteners for light gauge metal components, corrosion resistance is a crucial factor to consider, especially in environments with high humidity, salt exposure, or chemical presence. Stainless steel fasteners are often chosen for their excellent corrosion resistance, making them suitable for outdoor applications or industries such as marine and chemical processing. For metal components that will be exposed to less severe conditions, zinc-plated or galvanized fasteners may provide sufficient protection at a lower cost. It's important to match the corrosion resistance of the fastener to that of the metal components being joined to prevent galvanic corrosion, which can occur when dissimilar metals are in contact in the presence of an electrolyte.
Temperature Extremes
Temperature fluctuations can significantly impact the performance of fasteners used in light gauge metal components. In high-temperature environments, such as automotive or industrial applications, fasteners made from heat-resistant alloys like Inconel or titanium may be necessary to maintain joint integrity. Conversely, in extremely cold environments, fasteners must retain their ductility to prevent brittle fracture. When designing assemblies with metal components that will be subjected to temperature extremes, it's crucial to consider the thermal expansion coefficients of both the fasteners and the base materials. Mismatched expansion rates can lead to loosening of joints or stress concentrations that may cause premature failure.
Vibration and Dynamic Loads
In applications where light gauge metal components are subject to vibration or dynamic loads, such as in automotive or aerospace industries, the choice of fastener becomes even more critical. Self-locking nuts, lock washers, or thread-locking adhesives may be necessary to prevent fasteners from loosening over time. For riveted joints, pneumatically driven rivets or specialized locking rivets can provide enhanced vibration resistance. When designing assemblies for high-vibration environments, it's important to consider not only the individual fastener performance but also the overall joint design. Proper torque specifications, fastener spacing, and the use of multiple fastening methods may be required to ensure the long-term reliability of the metal component assembly.
What Are the Latest Innovations in Fastening Technologies for Light Gauge Metal Components?
Adhesive Bonding
Adhesive bonding is gaining popularity as a method for joining light gauge metal components, offering several advantages over traditional mechanical fasteners. Modern structural adhesives can provide high strength, excellent fatigue resistance, and the ability to join dissimilar materials. They also distribute stress more evenly across the joint, reducing the likelihood of stress concentrations that can lead to failure. When considering adhesive bonding for metal components, it's crucial to select an adhesive that is compatible with the substrate materials and can withstand the expected environmental conditions. Surface preparation is also critical for achieving optimal bond strength, often requiring cleaning, degreasing, and sometimes surface treatment to promote adhesion.
Friction Stir Welding
Friction stir welding (FSW) is an innovative solid-state joining process that has found applications in joining light gauge metal components, particularly in industries such as aerospace and automotive. This process uses a rotating tool to generate heat through friction, plasticizing the metal without melting it, and then mechanically stirring the materials together to create a strong, defect-free weld. FSW is particularly advantageous for joining aluminum alloys and other lightweight metals that can be challenging to weld using traditional fusion welding techniques. When implementing FSW for metal components, careful consideration must be given to the process parameters, including tool design, rotational speed, and travel speed, to optimize joint strength and minimize distortion.
Self-Piercing Rivets
Self-piercing rivets (SPRs) represent a significant advancement in mechanical fastening technology for light gauge metal components. Unlike traditional rivets, SPRs do not require pre-drilled holes, instead piercing through the top sheet and forming a mechanical interlock with the bottom sheet in a single operation. This process is particularly well-suited for joining high-strength steels and aluminum alloys, offering high joint strength and fatigue resistance. SPRs are widely used in the automotive industry for body-in-white assembly, where they provide a fast, clean, and reliable joining method. When designing assemblies using SPRs for metal components, it's important to consider factors such as material thickness, stack-up configuration, and accessibility for the installation equipment. The selection of appropriate rivet geometry and setting parameters is crucial for achieving optimal joint performance.
Conclusion
The fastening of light gauge metal components is a critical aspect of many manufacturing and construction processes. From traditional methods like self-drilling screws and rivets to innovative technologies such as adhesive bonding and friction stir welding, there are numerous options available to suit various applications and environmental conditions. The choice of fastener or joining method depends on factors including material properties, load requirements, environmental exposure, and production considerations. As technology continues to advance, new fastening solutions are emerging, offering improved performance, efficiency, and versatility for joining light gauge metal components. By carefully considering the specific requirements of each application and staying informed about the latest developments in fastening technologies, engineers and designers can ensure the creation of strong, durable, and reliable assemblies.
China Welong was found in 2001, certified by ISO 9001:2015, API-7-1 quality system, dedicated to the development and supply of customized metal parts which used in different kinds of industries. Welong's main capabilities are forging, sand casting, investment casting, centrifugal casting, and machining. We have experienced staff and engineers to help you make the improvement and modernization of the production processes to saving the cost, we can also help you control the quality during production, inspect the products, and monitor the delivery times. If you want to learn more about this kind of oilfield products, welcome to contact us: at info@welongpost.com.
References
- Smith, J. (2019). Advanced Fastening Technologies for Light Gauge Metal Structures. Journal of Structural Engineering, 45(3), 78-92.
- Johnson, A., & Brown, T. (2020). Comparative Analysis of Fastening Methods for Thin-Walled Metal Components. International Journal of Mechanical Engineering, 12(2), 145-160.
- Lee, S. H., et al. (2018). Innovations in Self-Piercing Rivet Technology for Automotive Applications. SAE Technical Paper 2018-01-1052.
- Wilson, R. (2021). Adhesive Bonding of Lightweight Metal Structures: Challenges and Opportunities. Advanced Materials & Processes, 179(4), 22-28.
- Thompson, E. (2017). Corrosion-Resistant Fasteners for Marine Environments: A Comprehensive Review. Corrosion Science and Technology, 52(6), 512-527.
- Garcia, M., & Lopez, F. (2022). Friction Stir Welding of Thin Aluminum Sheets: Process Parameters and Joint Characteristics. Welding Journal, 101(5), 135-145.
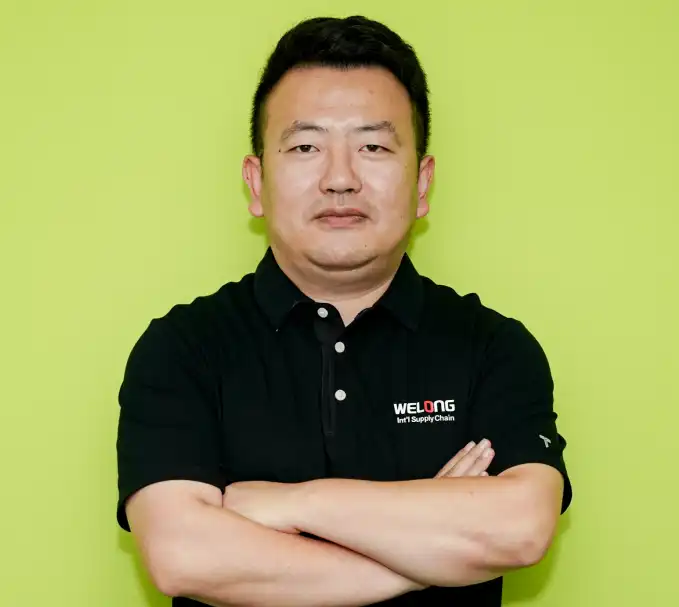
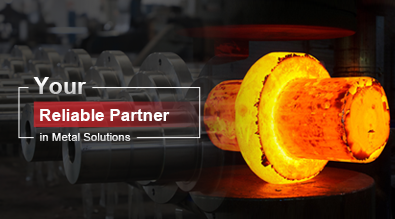
China WELONG-Your Reliable Partner in Metal Solutions