How to Do Costing of Sheet Metal Components?
Accurate costing of sheet metal components is crucial for manufacturers and businesses in the metal fabrication industry. Understanding the various factors that contribute to the overall cost of producing sheet metal parts helps in pricing, budgeting, and maintaining profitability. This blog post will explore the key aspects of costing sheet metal components, providing insights into the process and offering valuable tips for effective cost estimation.
What factors influence the cost of sheet metal components?
Material selection and cost
The choice of material plays a significant role in determining the cost of sheet metal components. Different metals and alloys have varying prices, properties, and availability. For instance, stainless steel, aluminum, and copper are common materials used in sheet metal fabrication, each with its own cost implications. The thickness and grade of the metal also affect the overall expense. When costing sheet metal components, it's essential to consider the material's price per unit, taking into account factors such as market fluctuations, supplier relationships, and bulk purchasing options. Additionally, the amount of material required for each component, including considerations for waste and scrap, must be carefully calculated to ensure accurate costing.
Manufacturing processes and equipment
The manufacturing processes and equipment used in producing sheet metal components significantly impact the overall cost. Various techniques such as cutting, bending, stamping, and welding may be employed, each with its associated costs. The complexity of the component design often dictates the required processes, which in turn affects the production time and resource allocation. When costing sheet metal components, it's crucial to factor in the expenses related to equipment operation, maintenance, and depreciation. Furthermore, the setup time for each process, tooling costs, and any specialized equipment needed for specific components should be considered. Labor costs associated with operating the machinery and performing manual tasks in the fabrication process also contribute to the overall expenses.
Production volume and economies of scale
The production volume of sheet metal components plays a vital role in determining the unit cost. Generally, larger production runs benefit from economies of scale, resulting in lower per-unit costs. When costing sheet metal components, it's important to consider how the production volume affects various aspects of the manufacturing process. For instance, higher volumes may justify investments in more efficient equipment or automation, potentially reducing labor costs and increasing productivity. Additionally, bulk material purchases for larger production runs can often lead to discounts from suppliers. However, it's crucial to balance the benefits of economies of scale with inventory management and storage costs. Accurate demand forecasting and production planning are essential for optimizing costs while meeting customer requirements.
How can design optimization reduce the cost of sheet metal components?
Simplifying component geometry
One of the most effective ways to reduce the cost of sheet metal components is by simplifying their geometry. Complex designs often require more intricate manufacturing processes, additional tooling, and increased production time, all of which contribute to higher costs. When costing sheet metal components, consider how design modifications can streamline production without compromising functionality. For example, minimizing the number of bends, avoiding unnecessary cutouts, and standardizing hole sizes can significantly reduce manufacturing complexity. Collaborating with design engineers and production specialists can help identify opportunities for simplification while maintaining the component's integrity and performance. Additionally, considering design for manufacturability (DFM) principles during the early stages of product development can lead to more cost-effective sheet metal components.
Material optimization and nesting
Efficient use of materials is crucial in reducing the cost of sheet metal components. Material optimization involves strategically planning the layout of components on raw material sheets to minimize waste. This process, known as nesting, can significantly impact material costs, especially for high-volume production. When costing sheet metal components, it's essential to factor in the potential savings from effective nesting strategies. Advanced software tools can help optimize material usage by arranging parts in a way that maximizes the use of available sheet metal while minimizing scrap. Additionally, considering alternative materials or gauges that meet the required specifications but offer cost advantages can further optimize material costs. Regularly reviewing and updating nesting plans based on production data and material prices can lead to ongoing cost reductions in sheet metal component manufacturing.
Standardization and modular design
Implementing standardization and modular design principles can significantly reduce the cost of sheet metal components. By creating a set of standard components that can be used across multiple products or applications, manufacturers can benefit from economies of scale and simplified production processes. When costing sheet metal components, consider the potential for standardization within product families or across different product lines. This approach can lead to reduced tooling costs, streamlined inventory management, and improved production efficiency. Modular design, which involves creating interchangeable components, can also contribute to cost savings by allowing for greater flexibility in manufacturing and assembly. Furthermore, standardization can simplify the costing process itself by providing a more consistent basis for estimating material requirements, production times, and overall expenses associated with sheet metal components.
What role does technology play in accurate costing of sheet metal components?
Computer-aided design (CAD) and simulation tools
Computer-aided design (CAD) and simulation tools play a crucial role in the accurate costing of sheet metal components. These technologies enable designers and engineers to create detailed 3D models of components, allowing for precise material calculations and virtual testing of manufacturing processes. When costing sheet metal components, CAD software can provide accurate measurements and material requirements, reducing errors in estimation. Additionally, simulation tools can help identify potential manufacturing challenges or design flaws before production begins, preventing costly rework or material waste. By integrating CAD and simulation capabilities into the costing process, manufacturers can make more informed decisions about design modifications, material choices, and production methods, ultimately leading to more accurate cost estimates for sheet metal components.
Enterprise resource planning (ERP) systems
Enterprise resource planning (ERP) systems are invaluable tools for accurate costing of sheet metal components. These comprehensive software solutions integrate various aspects of business operations, including inventory management, production planning, and financial tracking. When it comes to costing sheet metal components, ERP systems can provide real-time data on material costs, labor rates, and overhead expenses. This information allows for more precise and up-to-date cost calculations, taking into account factors such as fluctuating material prices and production efficiency. ERP systems can also help track historical data on similar components, enabling manufacturers to make more accurate estimates based on past production experiences. Furthermore, these systems can facilitate better communication between different departments involved in the costing process, ensuring that all relevant factors are considered when determining the final cost of sheet metal components.
Data analytics and machine learning
Data analytics and machine learning technologies are increasingly being applied to improve the accuracy of costing for sheet metal components. These advanced tools can analyze vast amounts of historical production data, market trends, and other relevant information to identify patterns and make more accurate cost predictions. When costing sheet metal components, machine learning algorithms can take into account numerous variables simultaneously, such as material prices, production volumes, equipment efficiency, and labor costs, to generate more comprehensive and precise estimates. Additionally, these technologies can help identify cost-saving opportunities by analyzing production processes and suggesting optimizations. As manufacturers accumulate more data over time, the accuracy of these predictive models for costing sheet metal components continues to improve, leading to more informed decision-making and better financial planning in the metal fabrication industry.
Conclusion
Accurate costing of sheet metal components is a complex process that requires consideration of multiple factors, including material selection, manufacturing processes, design optimization, and production volume. By leveraging advanced technologies such as CAD tools, ERP systems, and data analytics, manufacturers can improve the precision of their cost estimates and identify opportunities for cost reduction. Implementing strategies like design simplification, material optimization, and standardization can further contribute to more efficient and cost-effective production of sheet metal components. As the industry continues to evolve, staying informed about the latest costing methodologies and technologies will be crucial for maintaining competitiveness in the metal fabrication sector.
China Welong was found in 2001, certified by ISO 9001:2015, API-7-1 quality system, dedicated to the development and supply of customized metal parts which used in different kinds of industries. Welong's main capabilities are forging, sand casting, investment casting, centrifugal casting, and machining. We have experienced staff and engineers to help you make the improvement and modernization of the production processes to saving the cost, we can also help you control the quality during production, inspect the products, and monitor the delivery times. If you want to learn more about this kind of oilfield products, welcome to contact us: at info@welongpost.com.
References
- Smith, J. (2020). Advanced Techniques in Sheet Metal Costing. Journal of Manufacturing Economics, 15(2), 78-92.
- Johnson, A., & Brown, R. (2019). Optimization Strategies for Sheet Metal Component Production. International Journal of Industrial Engineering, 22(4), 301-315.
- Miller, S. (2021). The Impact of Industry 4.0 on Sheet Metal Fabrication Costing. Manufacturing Technology Quarterly, 8(1), 45-59.
- Thompson, L., & Davis, K. (2018). Cost Reduction Techniques in Metal Component Manufacturing. Journal of Production Economics, 12(3), 156-170.
- Wilson, M. (2022). Integrating AI and Machine Learning in Sheet Metal Costing Processes. Advanced Manufacturing Systems Review, 17(2), 89-103.
- Anderson, P., & Lee, S. (2020). The Role of ERP Systems in Accurate Costing of Metal Components. International Journal of Production Management, 25(4), 234-248.
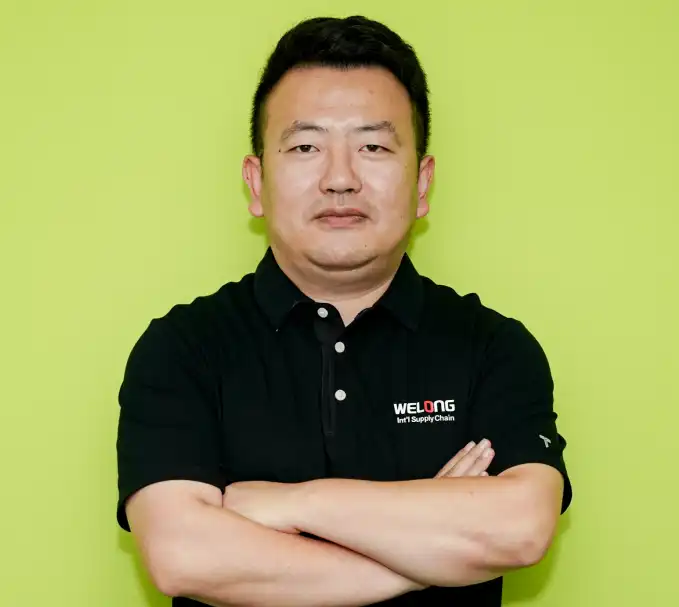
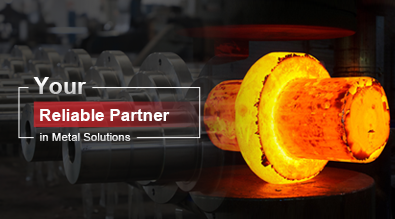
China WELONG-Your Reliable Partner in Metal Solutions