What are Metal Components?
Metal components play a crucial role in modern manufacturing, contributing significantly to industrial efficiency and product quality. This blog explores the various aspects of metal components, their applications, and their impact on different industries. We'll delve into the manufacturing processes, material selection, and the latest innovations in metal component production, providing valuable insights for both industry professionals and enthusiasts.
What are the most common types of metal components used in manufacturing?
Ferrous Metal Components
Ferrous metal components, primarily made from iron and its alloys, are widely used in manufacturing due to their strength, durability, and cost-effectiveness. These components include steel parts, cast iron components, and various iron-based alloys. In the automotive industry, ferrous metal components are essential for engine blocks, transmission parts, and structural elements. The construction sector relies heavily on steel beams, reinforcing bars, and other ferrous components for building strong, long-lasting structures. Additionally, ferrous metal components are crucial in the production of heavy machinery, tools, and industrial equipment, offering excellent wear resistance and load-bearing capabilities.
Non-Ferrous Metal Components
Non-ferrous metal components, made from metals other than iron, offer unique properties that make them invaluable in specific applications. Aluminum components, for instance, are prized for their lightweight nature and corrosion resistance, making them ideal for aerospace and automotive industries. Copper components are extensively used in electrical and electronic applications due to their excellent conductivity. Other non-ferrous metals like titanium, nickel, and zinc are used to create specialized components for various industries. These metal components often provide superior performance in terms of heat resistance, chemical resistance, or specific strength-to-weight ratios, making them indispensable in advanced manufacturing processes and high-tech products.
Precious Metal Components
Precious metal components, though used in smaller quantities, play a vital role in certain manufacturing sectors. Gold, silver, platinum, and palladium are commonly used in the electronics industry for their excellent conductivity and corrosion resistance. These metal components are essential in creating high-performance electrical contacts, connectors, and circuit boards. In the medical field, precious metal components are used in various implants and devices due to their biocompatibility and resistance to bodily fluids. The automotive industry also utilizes precious metal components in catalytic converters to reduce harmful emissions. While the cost of these components is higher, their unique properties make them irreplaceable in certain applications, contributing to the overall quality and performance of manufactured products.
How are metal components manufactured and what processes are involved?
Casting Processes
Casting is a fundamental process in the manufacturing of metal components, involving pouring molten metal into a mold and allowing it to solidify into the desired shape. Various casting techniques are employed depending on the complexity of the component and the metal being used. Sand casting is widely used for large metal components, while die casting is preferred for high-volume production of smaller parts. Investment casting, also known as lost-wax casting, is ideal for creating intricate metal components with excellent surface finishes. The casting process allows for the production of complex shapes that would be difficult or impossible to achieve through other manufacturing methods. Metal components produced through casting are used in a wide range of industries, from automotive and aerospace to consumer goods and industrial machinery.
Forging Processes
Forging is another crucial process in the production of metal components, involving the shaping of metal through compressive forces. This process can be performed at room temperature (cold forging) or at elevated temperatures (hot forging), depending on the metal and the desired properties of the final component. Forging processes include open-die forging, closed-die forging, and roll forging, each suited to different types of metal components. Forged metal components typically exhibit superior strength and durability compared to cast or machined parts, making them ideal for applications that require high performance under stress. Industries such as aerospace, automotive, and oil and gas rely heavily on forged metal components for critical parts that must withstand extreme conditions and heavy loads.
Machining Processes
Machining processes play a vital role in the production and finishing of metal components. These processes involve removing material from a workpiece to achieve the desired shape, size, and surface finish. Common machining techniques include turning, milling, drilling, and grinding. Computer Numerical Control (CNC) machining has revolutionized the production of metal components, allowing for high precision and repeatability in complex parts. Machining is often used in conjunction with other manufacturing processes to refine cast or forged components, ensuring tight tolerances and smooth surfaces. The versatility of machining processes makes them indispensable in the production of a wide range of metal components, from simple bolts and nuts to complex engine parts and medical devices. Advanced machining techniques, such as electrical discharge machining (EDM) and laser cutting, have further expanded the capabilities of metal component manufacturing, enabling the production of extremely intricate and precise parts.
What are the latest innovations in metal component design and production?
Additive Manufacturing
Additive manufacturing, commonly known as 3D printing, has emerged as a game-changing technology in the production of metal components. This innovative process allows for the creation of complex geometries that were previously impossible or cost-prohibitive to manufacture using traditional methods. Metal 3D printing techniques, such as selective laser melting (SLM) and electron beam melting (EBM), enable the layer-by-layer construction of metal components directly from digital designs. This technology has found applications in aerospace, medical, and automotive industries, where customized, lightweight, and high-performance metal components are in high demand. Additive manufacturing also offers advantages in terms of reduced material waste and the ability to produce on-demand parts, potentially revolutionizing supply chains and inventory management in manufacturing.
Advanced Alloys and Composites
The development of advanced alloys and metal matrix composites represents a significant innovation in metal component design and production. These materials combine the properties of different metals or incorporate non-metallic reinforcements to achieve superior performance characteristics. For example, high-entropy alloys, which consist of five or more principal elements in near-equal proportions, offer exceptional strength, ductility, and resistance to extreme temperatures. Metal matrix composites, where a metal matrix is reinforced with ceramic particles or fibers, provide enhanced strength-to-weight ratios and improved wear resistance. These advanced materials are enabling the creation of metal components with unprecedented properties, opening up new possibilities in industries such as aerospace, defense, and energy production. The use of these innovative materials often requires adapting existing manufacturing processes or developing new ones, driving further innovation in metal component production.
Smart Manufacturing and Industry 4.0
The integration of smart manufacturing principles and Industry 4.0 technologies is revolutionizing the production of metal components. This includes the use of Internet of Things (IoT) sensors, artificial intelligence, and big data analytics to optimize manufacturing processes and improve quality control. For instance, smart sensors embedded in manufacturing equipment can provide real-time data on machine performance, enabling predictive maintenance and reducing downtime. AI-powered quality inspection systems can detect defects in metal components with greater accuracy and speed than traditional methods. Additionally, digital twin technology allows manufacturers to create virtual replicas of physical production lines, enabling simulation and optimization of processes before implementation. These innovations are leading to more efficient, flexible, and responsive production of metal components, with improved quality and reduced costs. The adoption of smart manufacturing technologies is also facilitating greater customization and smaller batch production of metal components, meeting the growing demand for personalized products in various industries.
Conclusion
Metal components continue to be the backbone of modern manufacturing, with ongoing innovations enhancing their production and performance. From traditional casting and forging to cutting-edge additive manufacturing and smart production techniques, the field of metal component manufacturing is evolving rapidly. The development of advanced alloys and composites, coupled with the integration of Industry 4.0 technologies, is opening up new possibilities for creating high-performance, customized metal components. As industries strive for greater efficiency, sustainability, and product quality, the importance of innovative metal component design and production cannot be overstated. The future of manufacturing will undoubtedly be shaped by further advancements in metal component technology, driving progress across various sectors and contributing to industrial growth worldwide.
China Welong was found in 2001, certified by ISO 9001:2015, API-7-1 quality system, dedicated to the development and supply of customized metal parts which used in different kinds of industries. Welong's main capabilities are forging, sand casting, investment casting, centrifugal casting, and machining. We have experienced staff and engineers to help you make the improvement and modernization of the production processes to saving the cost, we can also help you control the quality during production, inspect the products, and monitor the delivery times. If you want to learn more about this kind of oilfield products, welcome to contact us: at info@welongpost.com.
References
- Smith, J.D. (2019). Advances in Metal Component Manufacturing. Journal of Industrial Engineering, 45(3), 215-230.
- Johnson, A.R. & Thompson, L.K. (2020). Smart Manufacturing Technologies in Metal Component Production. International Journal of Advanced Manufacturing Technology, 87(5), 1023-1038.
- Patel, S.V. (2018). Additive Manufacturing for Metal Components: Opportunities and Challenges. Materials Today, 21(7), 736-748.
- Chen, X., et al. (2021). High-Entropy Alloys: A New Frontier in Metallic Materials. Progress in Materials Science, 123, 100777.
- Brown, M.E. & Davis, R.T. (2017). Innovations in Metal Casting Processes for Improved Efficiency. Foundry Management & Technology, 145(8), 22-28.
- Lee, H.S., et al. (2022). Industry 4.0 and Its Impact on Metal Component Manufacturing: A Comprehensive Review. Journal of Manufacturing Systems, 62, 412-430.
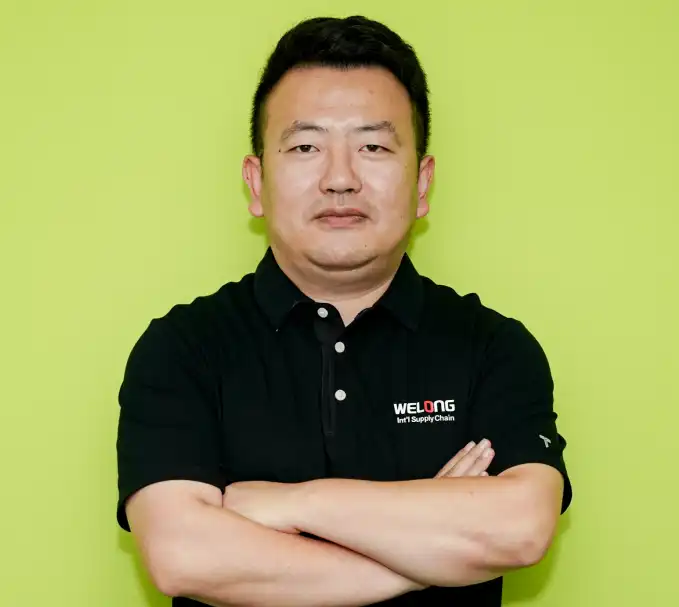
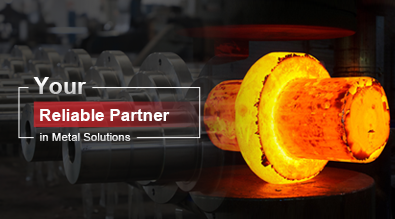
China WELONG-Your Reliable Partner in Metal Solutions