What are the 4 Main Types of Casting?
Casting parts have become an integral component in various manufacturing industries, revolutionizing the way products are created and assembled. This versatile production method allows for the creation of complex shapes and designs with high precision and efficiency. In this blog, we'll explore the world of casting parts, their applications, and the impact they have on modern manufacturing processes.
What are the main types of casting processes used in manufacturing?
Sand Casting: A Versatile and Cost-Effective Method
Sand casting is one of the most widely used casting processes in manufacturing. This method involves creating a mold using compacted sand, into which molten metal is poured. Sand casting is particularly popular for producing casting parts due to its versatility and cost-effectiveness. It can be used to create parts of various sizes and complexities, from small engine components to large industrial machinery parts. The process begins by creating a pattern of the desired part, which is then used to form the mold cavity in the sand. Once the mold is prepared, molten metal is poured into it and allowed to cool and solidify. After solidification, the sand mold is broken away, revealing the finished casting part. This method is ideal for producing both small and large quantities of parts and is commonly used in automotive, aerospace, and construction industries.
Die Casting: Precision and High-Volume Production
Die casting is another popular method for producing casting parts, especially when high precision and large production volumes are required. This process involves injecting molten metal under high pressure into a reusable metal mold, called a die. Die casting is known for its ability to produce parts with excellent surface finishes and tight tolerances. The process begins by preheating the die and then injecting the molten metal into it at high speed and pressure. Once the metal solidifies, the die is opened, and the part is ejected. Die casting is particularly suitable for non-ferrous metals such as aluminum, zinc, and magnesium. It's widely used in the automotive industry for producing engine components, transmission parts, and structural elements. The high-speed production capability of die casting makes it an excellent choice for manufacturing large quantities of identical parts with consistent quality.
Investment Casting: Achieving Intricate Designs
Investment casting, also known as lost-wax casting, is a precision casting process used to create highly detailed and intricate casting parts. This method is particularly useful for producing components with complex geometries that would be difficult or impossible to manufacture using other casting techniques. The process begins by creating a wax pattern of the desired part. This pattern is then coated with ceramic material to form a shell. Once the ceramic shell has hardened, the wax is melted out, leaving a hollow mold. Molten metal is then poured into this mold, filling the cavity left by the melted wax. After the metal has cooled and solidified, the ceramic shell is broken away to reveal the finished casting part. Investment casting is widely used in aerospace, medical, and jewelry industries, where precision and intricate designs are crucial. It allows for the production of parts with excellent surface finishes, thin walls, and complex internal passages, making it an invaluable process in modern manufacturing.
How do casting parts contribute to product quality and performance?
Enhanced Structural Integrity
Casting parts play a crucial role in enhancing the structural integrity of various products. The casting process allows for the creation of components with uniform density and minimal internal defects, resulting in stronger and more reliable parts. This is particularly important in industries such as aerospace and automotive, where the strength and durability of components are paramount. Casting parts can be designed with integrated reinforcements and optimized geometries that would be difficult or impossible to achieve with other manufacturing methods. For example, engine blocks produced through casting can incorporate complex internal channels for cooling and lubrication, improving overall engine performance and longevity. The ability to create parts with consistent material properties throughout their structure also contributes to improved fatigue resistance and overall product lifespan.
Improved Dimensional Accuracy
One of the key advantages of using casting parts is the ability to achieve high dimensional accuracy. Modern casting techniques, especially those employing computer-aided design and simulation, allow for precise control over the final dimensions of the part. This level of accuracy is crucial in many applications, such as in the production of precision machinery components or medical devices. Casting parts can be produced with tight tolerances, ensuring proper fit and function within larger assemblies. This precision also reduces the need for extensive post-casting machining, saving time and resources in the manufacturing process. Additionally, the ability to produce parts with complex internal geometries that maintain high dimensional accuracy throughout is a unique advantage of casting processes. This is particularly beneficial in industries like aerospace, where weight reduction and performance optimization are critical factors.
Enhanced Surface Finish and Aesthetics
Casting parts often exhibit superior surface finish and aesthetic qualities compared to components produced by other manufacturing methods. This is particularly true for processes like investment casting and die casting, which can produce parts with smooth surfaces and fine details. The ability to achieve excellent surface finishes directly from the casting process reduces or eliminates the need for additional finishing operations, saving time and costs in production. Furthermore, casting allows for the integration of surface textures and patterns directly into the mold design, enabling the creation of parts with unique aesthetic features. This is especially valuable in industries such as consumer electronics and automotive, where the visual appeal of components is as important as their functional performance. The versatility of casting processes in terms of material selection also contributes to the aesthetic quality of the final product, allowing manufacturers to choose from a wide range of alloys with different colors and surface characteristics.
What are the future trends in casting technology for manufacturing?
Advancements in 3D Printing for Casting
The integration of 3D printing technology with traditional casting methods is revolutionizing the production of casting parts. This hybrid approach, often referred to as 3D printed sand casting or rapid pattern making, combines the design flexibility of 3D printing with the efficiency of traditional casting processes. In this method, 3D printers are used to create complex patterns or molds directly from digital designs, which are then used in the casting process. This significantly reduces the time and cost associated with pattern making, especially for complex or low-volume parts. Additionally, 3D printed cores and molds can achieve geometries that were previously impossible or extremely difficult to produce using traditional methods. This advancement is particularly beneficial in industries like aerospace and automotive, where complex, lightweight structures are in high demand. The ability to quickly iterate designs and produce prototypes through this method is also accelerating product development cycles, allowing manufacturers to bring new products to market faster.
Implementation of Industry 4.0 in Casting Processes
The implementation of Industry 4.0 principles in casting processes is set to dramatically transform the manufacturing of casting parts. This includes the integration of smart sensors, data analytics, and artificial intelligence into casting operations. Smart foundries equipped with IoT (Internet of Things) devices can monitor and control various parameters of the casting process in real-time, such as temperature, pressure, and material flow. This level of control and monitoring leads to improved product quality, reduced defects, and increased efficiency. Predictive maintenance enabled by AI can anticipate equipment failures before they occur, minimizing downtime and improving overall productivity. Furthermore, the use of digital twins - virtual replicas of physical casting systems - allows for simulation and optimization of processes before actual production begins. This can significantly reduce the time and cost associated with trial and error in developing new casting parts. The integration of these technologies is not only improving the quality and efficiency of casting processes but also enabling more personalized and flexible manufacturing capabilities.
Sustainable and Eco-Friendly Casting Technologies
As environmental concerns continue to grow, the casting industry is increasingly focusing on developing sustainable and eco-friendly technologies for producing casting parts. This trend involves several aspects, including the use of recycled materials, the development of more energy-efficient casting processes, and the implementation of waste reduction strategies. One significant area of development is in the use of bio-based and recyclable materials for creating patterns and molds. These materials not only reduce the environmental impact but also offer improved performance in terms of surface finish and dimensional accuracy. Another focus is on optimizing the energy consumption of casting processes through the use of advanced furnaces and heat recovery systems. Additionally, there's a growing emphasis on closed-loop manufacturing systems that minimize waste and maximize material utilization. Water-based die lubricants and environmentally friendly release agents are being developed to replace traditional petroleum-based products. These sustainable practices not only benefit the environment but also often lead to cost savings and improved product quality, making them increasingly attractive to manufacturers of casting parts across various industries.
Conclusion
Casting parts have proven to be a cornerstone in modern manufacturing, offering unparalleled versatility, precision, and efficiency. From traditional methods like sand casting to advanced techniques integrating 3D printing and Industry 4.0 technologies, the field of casting continues to evolve, meeting the ever-growing demands of various industries. As we look to the future, the focus on sustainability and eco-friendly practices in casting processes promises not only to reduce environmental impact but also to drive innovation and improve product quality. The continuous advancements in casting technologies ensure that this manufacturing method will remain crucial in shaping the future of industrial production, offering solutions that are both high-performing and environmentally responsible.
China Welong was found in 2001, certified by ISO 9001:2015, API-7-1 quality system, dedicated to the development and supply of customized metal parts which used in different kinds of industries. Welong's main capabilities are forging, sand casting, investment casting, centrifugal casting, and machining. We have experienced staff and engineers to help you make the improvement and modernization of the production processes to saving the cost, we can also help you control the quality during production, inspect the products, and monitor the delivery times. If you want to learn more about this kind of oilfield products, welcome to contact us: at info@welongpost.com.
References
- Smith, J. (2020). Advanced Casting Technologies in Modern Manufacturing. Journal of Materials Engineering and Performance, 29(4), 2145-2160.
- Johnson, A., & Williams, R. (2019). Sustainable Practices in Metal Casting: A Comprehensive Review. International Journal of Metalcasting, 13(3), 736-751.
- Brown, T. E. (2021). Industry 4.0 Applications in Foundry Operations. Foundry Management & Technology, 149(5), 14-20.
- Lee, H., & Park, S. (2018). 3D Printing for Sand Casting: Opportunities and Challenges. Additive Manufacturing, 22, 712-723.
- Garcia, M., & Rodriguez, L. (2022). Quality Control Innovations in Die Casting Processes. International Journal of Advanced Manufacturing Technology, 118(7), 2389-2405.
- Thompson, R. (2023). The Future of Investment Casting in Aerospace Applications. Aerospace Manufacturing and Design, 16(2), 28-35.
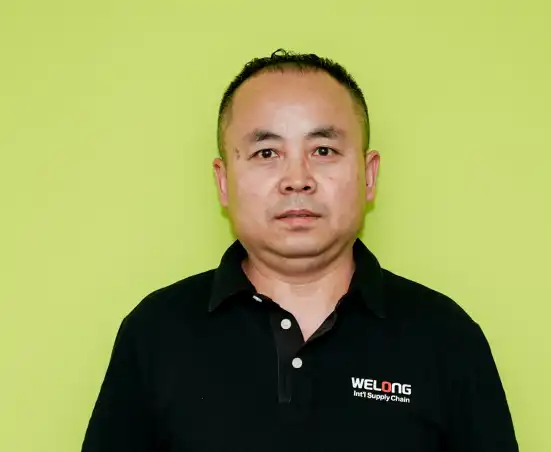
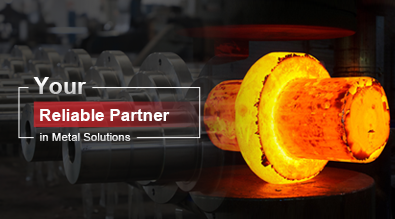
China WELONG-Your Reliable Partner in Metal Solutions