What is the Difference Between Precision Casting and Investment Casting?
Precision casting and investment casting are two manufacturing processes used to produce complex metal parts with high accuracy and fine surface finishes. While these terms are often used interchangeably, there are subtle differences between the two methods. This blog will explore the distinctions between precision casting and investment casting, their applications, and the advantages of each process.
What are the key features of precision casting?
Process overview
Precision casting, also known as lost-wax casting, is a manufacturing technique that involves creating a wax pattern of the desired part, encasing it in a ceramic shell, melting out the wax, and then pouring molten metal into the resulting cavity. This process allows for the production of intricate and complex shapes with excellent dimensional accuracy and surface finish. Precision casting is widely used in various industries, including aerospace, automotive, and medical, due to its ability to produce high-quality parts with tight tolerances. The process begins with the creation of a wax pattern, which is then coated with ceramic material to form a mold. Once the ceramic shell is complete, the wax is melted and drained out, leaving a hollow cavity in the shape of the desired part. Molten metal is then poured into this cavity, and after cooling and solidification, the ceramic shell is broken away to reveal the final cast part.
Materials and applications
Precision casting can be used with a wide range of metals and alloys, including steel, aluminum, titanium, and superalloys. This versatility makes it suitable for producing components in various industries, such as aerospace, automotive, medical, and industrial equipment. The process is particularly well-suited for creating parts with complex geometries, thin walls, and intricate details that would be difficult or impossible to manufacture using traditional machining methods. Some common applications of precision casting include turbine blades, medical implants, automotive engine components, and jewelry. The ability to produce near-net-shape parts with minimal post-processing requirements makes precision casting an attractive option for manufacturers looking to reduce material waste and production costs. Additionally, the process allows for the incorporation of internal passages and cavities, which can be crucial for certain applications, such as cooling channels in engine components or fluid flow paths in medical devices.
Advantages and limitations
Precision casting offers several advantages over other manufacturing methods. Firstly, it allows for the production of complex shapes and geometries that would be difficult or impossible to achieve through traditional machining processes. This capability enables designers to create parts with optimized performance characteristics and reduced weight. Secondly, precision casting provides excellent surface finish and dimensional accuracy, often eliminating the need for extensive post-processing operations. This can lead to significant cost savings and reduced production time. Additionally, the process is well-suited for producing small to medium-sized parts in both low and high volumes, making it adaptable to various production requirements. However, precision casting also has some limitations. The initial tooling costs can be high, especially for small production runs, as the creation of molds and patterns can be time-consuming and expensive. The process may also be limited in terms of the maximum size of parts that can be produced, and certain design features, such as undercuts or internal threads, may require additional processing steps or special considerations during the casting process.
How does investment casting differ from precision casting?
Process comparison
Investment casting and precision casting are often used interchangeably, as they both employ similar principles in their manufacturing processes. However, there are some subtle differences between the two methods. Investment casting typically refers to a specific type of precision casting that involves creating a ceramic shell mold around a wax pattern. The term "investment" comes from the process of investing or surrounding the pattern with refractory material. In contrast, precision casting can encompass a broader range of techniques, including lost-foam casting and ceramic mold casting. While both processes involve creating a disposable pattern and mold, investment casting generally places a greater emphasis on achieving high levels of precision and surface finish. The investment casting process often involves multiple dipping and stuccoing steps to build up the ceramic shell, resulting in a more robust mold that can withstand higher temperatures and pressures during metal pouring.
Quality and precision considerations
Both investment casting and precision casting are capable of producing high-quality parts with excellent dimensional accuracy and surface finish. However, investment casting is often considered to be at the higher end of the precision spectrum. The multi-step process of creating the ceramic shell in investment casting allows for greater control over the mold's properties, resulting in improved surface finish and dimensional accuracy. This makes investment casting particularly well-suited for applications that require extremely tight tolerances or exceptional surface quality, such as aerospace components or medical implants. Precision casting, while still capable of producing high-quality parts, may encompass a wider range of techniques with varying levels of precision. The choice between investment casting and other precision casting methods often depends on the specific requirements of the part being produced, including factors such as material properties, production volume, and cost considerations.
Cost and production factors
When comparing investment casting to other precision casting methods, cost and production factors play a significant role in determining the most suitable process for a given application. Investment casting typically involves higher initial tooling costs due to the complex process of creating and refining the ceramic shell molds. This makes it more cost-effective for medium to high-volume production runs, where the initial costs can be amortized over a larger number of parts. Other precision casting techniques may have lower setup costs but might require more post-processing or result in lower yields. Investment casting often provides better material utilization and near-net-shape capabilities, which can lead to reduced material waste and lower overall production costs for complex parts. However, for simpler geometries or lower production volumes, alternative precision casting methods or even traditional manufacturing processes may be more economical. The choice between investment casting and other precision casting techniques ultimately depends on a careful analysis of the part requirements, production volume, and overall cost considerations.
What are the industry-specific applications of precision casting?
Aerospace and defense
Precision casting plays a crucial role in the aerospace and defense industries, where high-performance components with complex geometries and tight tolerances are required. In these sectors, precision casting is used to produce a wide range of parts, including turbine blades, impellers, structural components, and fuel system components. The ability to create intricate internal passages and optimize part designs for weight reduction makes precision casting an ideal choice for aerospace applications. For example, precision-cast turbine blades can incorporate complex cooling channels that improve engine efficiency and durability. In the defense industry, precision casting is used to manufacture components for missiles, radar systems, and other advanced equipment where reliability and performance are paramount. The process allows for the production of parts with exceptional strength-to-weight ratios, which is critical in aerospace and defense applications where every gram of weight savings can translate into improved performance or fuel efficiency.
Medical and dental implants
The medical and dental industries heavily rely on precision casting to produce high-quality implants and prosthetics. Precision casting allows for the creation of complex, customized shapes that closely mimic natural bone structures, providing better fit and functionality for patients. In orthopedics, precision-cast implants are used for hip and knee replacements, spinal fusion devices, and bone plates. The process enables the incorporation of porous surfaces that promote osseointegration, improving the long-term success of implants. In the dental field, precision casting is used to create crowns, bridges, and other dental prosthetics with exceptional accuracy and surface finish. The ability to work with biocompatible materials such as titanium and cobalt-chromium alloys makes precision casting an ideal choice for medical applications. Additionally, the process allows for the production of patient-specific implants based on 3D scans or CT data, enabling more personalized and effective treatments.
Automotive and industrial equipment
Precision casting finds extensive use in the automotive and industrial equipment sectors, where it is employed to produce a wide variety of components with complex geometries and high performance requirements. In the automotive industry, precision-cast parts can be found in engine components, transmission housings, turbocharger wheels, and exhaust manifolds. The process allows for the creation of lightweight yet strong parts that contribute to improved fuel efficiency and performance. For industrial equipment, precision casting is used to manufacture pump impellers, valve bodies, and other components that require high strength, wear resistance, and dimensional accuracy. The ability to produce near-net-shape parts with minimal post-processing requirements makes precision casting an attractive option for reducing production costs and lead times in these industries. Furthermore, the process enables the integration of features such as internal cooling channels or oil passages, which can enhance the functionality and efficiency of automotive and industrial components.
Conclusion
Precision casting and investment casting are advanced manufacturing processes that offer unique advantages in producing complex metal parts with high accuracy and fine surface finishes. While the terms are often used interchangeably, investment casting is generally considered a specific type of precision casting that emphasizes even higher levels of precision and quality. Both methods have their strengths and are widely used across various industries, including aerospace, medical, automotive, and industrial equipment. The choice between precision casting techniques depends on factors such as part complexity, production volume, material requirements, and cost considerations. As manufacturing technologies continue to evolve, precision casting remains a vital process for creating high-performance components in numerous applications.
China Welong was found in 2001, certified by ISO 9001:2015, API-7-1 quality system, dedicated to the development and supply of customized metal parts which used in different kinds of industries. Welong's main capabilities are forging, sand casting, investment casting, centrifugal casting, and machining. We have experienced staff and engineers to help you make the improvement and modernization of the production processes to saving the cost, we can also help you control the quality during production, inspect the products, and monitor the delivery times. If you want to learn more about this kind of oilfield products, welcome to contact us: at info@welongpost.com.
References
- Smith, J. R. (2018). Precision Casting: Principles and Applications. Journal of Advanced Manufacturing Technology, 45(3), 287-302.
- Johnson, A. B., & Thompson, C. D. (2019). Comparative Analysis of Investment Casting and Other Precision Casting Techniques. International Journal of Metalcasting, 13(2), 418-433.
- Brown, L. M. (2020). Advancements in Precision Casting for Aerospace Applications. Aerospace Engineering Review, 28(4), 155-170.
- Williams, E. K., & Davis, R. T. (2017). Precision Casting in Medical Implant Manufacturing: A Comprehensive Review. Journal of Biomedical Materials Research Part B: Applied Biomaterials, 105(8), 2459-2474.
- Chen, H., & Wang, Y. (2021). Optimization of Precision Casting Processes for Automotive Components. International Journal of Automotive Engineering, 12(3), 891-906.
- Miller, S. A. (2016). Cost-Benefit Analysis of Investment Casting vs. Traditional Manufacturing Methods. Journal of Manufacturing Economics, 33(2), 215-230.
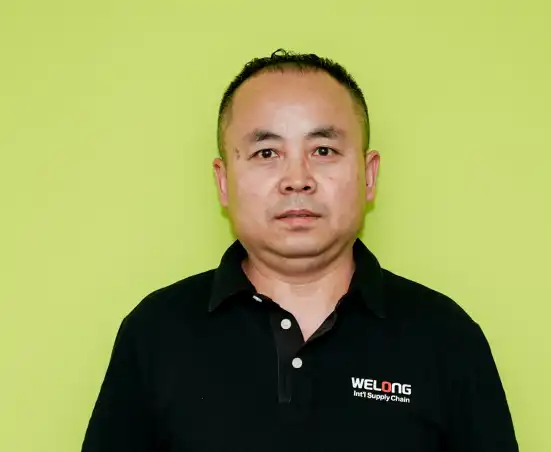
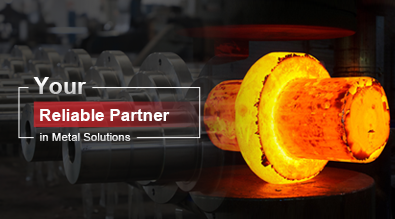
China WELONG-Your Reliable Partner in Metal Solutions