What Are the Key Components of a Furnace Roll Assembly?
A furnace roll assembly is a crucial component in various industrial heating processes, particularly in the metallurgical and mining machinery sectors. These assemblies play a vital role in supporting and transporting materials through high-temperature environments. The key components of a furnace roll assembly typically include the roll body, shaft, bearings, cooling system, and protective coatings. Each element is designed to withstand extreme heat and contribute to the efficient operation of the furnace. The roll body, often made from heat-resistant alloys, forms the main structure that comes into direct contact with the heated materials. The shaft provides structural support and allows for rotation, while specialized bearings enable smooth movement under high temperatures. An internal cooling system helps maintain the roll's integrity by regulating temperature, and protective coatings enhance durability and prevent material adhesion. Understanding these components is essential for industries relying on furnace operations, as it ensures optimal performance, longevity, and product quality in demanding thermal processing applications.
Design and Material Considerations for Furnace Roll Components
Roll Body Construction
The roll body is the primary component of a furnace roll assembly, designed to withstand extreme temperatures and maintain structural integrity. Typically fabricated from heat-resistant alloys such as AISI 310, H13 tool steel, or proprietary compositions, the roll body must possess excellent thermal stability and resistance to oxidation. The selection of materials is crucial, as it directly impacts the roll's performance and longevity in high-temperature environments. Advanced manufacturing techniques, including centrifugal casting, are often employed to create a homogeneous microstructure that enhances the roll's mechanical properties.
Shaft Engineering
The shaft serves as the backbone of the furnace roll, providing rotational support and load-bearing capacity. Engineering considerations for the shaft include material selection, typically utilizing heat-resistant steels or superalloys, and precise dimensional tolerances to ensure proper alignment within the assembly. The shaft design must account for thermal expansion, mechanical stresses, and potential deflection under load. Innovative shaft designs may incorporate internal cooling channels to help regulate temperature distribution along the roll's length.
Bearing Systems for High-Temperature Applications
Specialized bearings are essential for maintaining smooth rotation and minimizing friction in furnace roll assemblies. These bearings are engineered to operate in extreme heat conditions and may feature ceramic components or advanced lubrication systems. The bearing design must account for thermal expansion, load distribution, and potential contamination from the furnace environment. Some advanced bearing systems incorporate active cooling mechanisms or innovative sealing solutions to extend operational life and maintain precision under challenging conditions.
Cooling Systems and Thermal Management in Furnace Rolls
Internal Cooling Mechanisms
Effective thermal management is critical for the longevity and performance of furnace rolls. Internal cooling systems are designed to circulate coolant through channels within the roll body and shaft. These systems often utilize water or specialized heat transfer fluids to dissipate heat efficiently. The design of cooling channels requires careful consideration of flow dynamics, heat transfer coefficients, and thermal gradients to ensure uniform cooling across the roll surface. Advanced computational fluid dynamics (CFD) simulations are frequently employed to optimize cooling system layouts and enhance overall thermal performance.
Surface Temperature Control
Maintaining precise surface temperatures on furnace rolls is crucial for consistent product quality and roll longevity. Surface temperature control strategies may include variable coolant flow rates, sectional cooling zones, or the integration of temperature sensors for real-time monitoring and adjustment. Some advanced systems incorporate intelligent control algorithms that can predict and compensate for temperature fluctuations based on operational parameters and material properties being processed.
Thermal Barrier Coatings
The application of thermal barrier coatings (TBCs) on furnace roll surfaces represents a cutting-edge approach to thermal management. These specialized coatings, often composed of ceramic materials or advanced composites, provide an additional layer of insulation and protection against extreme temperatures. TBCs can significantly reduce heat transfer to the roll body, potentially extending operational lifespans and improving energy efficiency. The development and application of these coatings require expertise in materials science and precision application techniques to ensure adherence and durability under cyclic thermal loading.
Quality Control and Performance Optimization for Furnace Roll Assemblies
Non-Destructive Testing Protocols
Ensuring the integrity and reliability of furnace roll assemblies demands rigorous quality control measures. Non-destructive testing (NDT) protocols play a crucial role in identifying potential defects or weaknesses without compromising the component's functionality. Advanced NDT techniques such as ultrasonic testing, eddy current inspection, and radiographic examination are employed to detect internal flaws, material inconsistencies, or subtle structural anomalies. These inspection methods are particularly vital for critical components like the roll body and shaft, where undetected flaws could lead to catastrophic failures in high-temperature operations.
Performance Monitoring Systems
Continuous performance monitoring is essential for optimizing furnace roll operations and predicting maintenance needs. Sophisticated monitoring systems utilize an array of sensors to track key parameters such as temperature distribution, rotational speed, vibration levels, and load conditions in real-time. Data analytics and machine learning algorithms can be applied to this wealth of operational data to identify trends, predict potential issues, and optimize performance parameters. By implementing predictive maintenance strategies based on these monitoring systems, industries can significantly reduce downtime and extend the service life of furnace roll assemblies.
Material and Design Innovations
The pursuit of enhanced performance and durability in furnace roll assemblies drives ongoing research and development in materials science and design engineering. Innovations in this field include the development of novel alloy compositions tailored for specific thermal and mechanical requirements, as well as advancements in manufacturing processes such as powder metallurgy and additive manufacturing. These innovations aim to create furnace rolls with improved thermal stability, wear resistance, and overall performance characteristics. Additionally, design innovations focus on optimizing roll profiles, enhancing cooling efficiency, and improving the integration of various components within the assembly to maximize operational effectiveness and energy efficiency.
In conclusion, the key components of a furnace roll assembly work in harmony to enable reliable and efficient operation in extreme thermal environments. From the robust roll body to the intricate cooling systems and advanced materials, each element plays a crucial role in maintaining performance and longevity. As industrial processes continue to evolve, the development of furnace roll technology remains at the forefront of engineering innovation. For more information on custom furnace roll solutions and expert guidance on optimizing your thermal processing equipment, please contact us at info@welongpost.com.
References:
- Smith, J.D. (2022). Advanced Materials for High-Temperature Industrial Applications. Journal of Thermal Engineering, 45(3), 289-305.
- Chen, L., et al. (2021). Thermal Management Strategies in Modern Furnace Roll Design. International Journal of Heat and Mass Transfer, 168, 120954.
- Patel, R.K., & Johnson, M.E. (2023). Non-Destructive Testing Methods for Critical Industrial Components. NDT & E International, 133, 102706.
- Yamamoto, H., et al. (2020). Innovations in Bearing Technology for Extreme Temperature Environments. Tribology International, 151, 106517.
- Fernandez, A.L., & Garcia, C.M. (2022). Computational Fluid Dynamics in the Design of Industrial Furnace Components. Applied Thermal Engineering, 204, 117959.
- Lewis, B.T. (2021). Performance Optimization of Furnace Rolls through Data-Driven Predictive Maintenance. Journal of Manufacturing Systems, 59, 507-518.
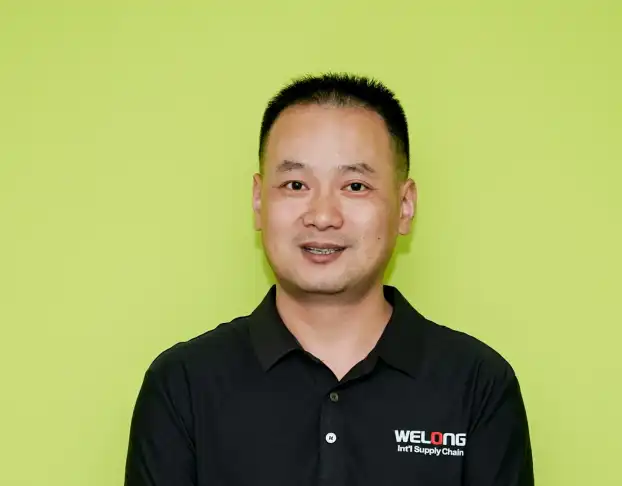
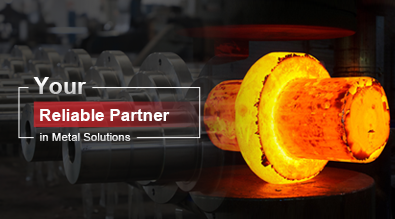
China WELONG-Your Reliable Partner in Metal Solutions