What is the Difference Between Spare Part and Wear Part?
In the world of machinery and equipment maintenance, understanding the distinction between spare parts and wear parts is crucial for effective management and cost control. This blog post will delve into the key differences between these two types of components, focusing on wear parts and their significance in various industries. We'll explore the characteristics, applications, and importance of wear parts, as well as how they differ from spare parts in terms of functionality and replacement frequency.
What are the characteristics of wear parts?
Definition and purpose of wear parts
Wear parts are components designed to experience gradual deterioration during normal operation of machinery or equipment. These parts are intentionally engineered to absorb the majority of wear and tear, protecting more critical and expensive components from damage. Wear parts are typically in direct contact with the materials being processed or the environment in which the equipment operates. Examples of wear parts include cutting edges on excavator buckets, conveyor belt rollers, and brake pads in vehicles. The primary purpose of wear parts is to maintain the overall efficiency and performance of the equipment while minimizing downtime and repair costs.
Materials used in wear parts manufacturing
The materials used in the production of wear parts are carefully selected to withstand the specific conditions they will encounter during operation. Common materials for wear parts include high-carbon steels, manganese steels, and various alloys that offer superior hardness and abrasion resistance. In some cases, wear parts may be coated with specialized materials such as tungsten carbide or ceramic composites to further enhance their durability. The choice of material depends on factors such as the operating environment, expected loads, and the type of wear the part will experience. Manufacturers often conduct extensive research and testing to develop wear parts that strike the optimal balance between durability and cost-effectiveness.
Factors affecting wear part lifespan
Several factors influence the lifespan of wear parts, and understanding these can help operators and maintenance teams optimize their replacement strategies. The primary factors include the operating environment (e.g., temperature, humidity, and presence of abrasive materials), the intensity and frequency of use, and the quality of the wear part itself. Regular maintenance, proper lubrication, and adherence to manufacturer guidelines can significantly extend the life of wear parts. Additionally, monitoring the performance of wear parts and implementing predictive maintenance techniques can help identify the optimal time for replacement, minimizing both unnecessary downtime and the risk of catastrophic failure due to worn-out components.
How do wear parts differ from spare parts in terms of replacement frequency?
Typical replacement intervals for wear parts
Wear parts generally require more frequent replacement compared to spare parts due to their nature and function. The replacement intervals for wear parts can vary widely depending on the specific application and operating conditions. For example, cutting edges on earthmoving equipment may need replacement every few weeks in harsh environments, while conveyor belt rollers might last several months to a year under normal conditions. It's essential for maintenance teams to establish a regular inspection schedule and track the performance of wear parts to anticipate replacement needs. Some advanced equipment may incorporate sensors or monitoring systems that can provide real-time data on the condition of wear parts, allowing for more precise replacement timing.
Factors influencing replacement frequency
Several factors can affect how often wear parts need to be replaced. The quality of the wear part itself plays a significant role, with higher-quality components generally lasting longer but often coming at a higher initial cost. The operating environment is another crucial factor, as exposure to extreme temperatures, corrosive substances, or abrasive materials can accelerate wear. The intensity and duration of use also directly impact replacement frequency, with equipment operating in continuous, high-stress conditions requiring more frequent part changes. Additionally, the effectiveness of maintenance practices, including proper lubrication and cleaning, can significantly influence how long wear parts last before needing replacement.
Cost implications of wear part replacement
The cost implications of wear part replacement extend beyond the simple price of the components themselves. While wear parts are generally less expensive than major spare parts, their more frequent replacement can result in significant cumulative costs over time. However, these costs must be weighed against the benefits of protecting more expensive components and maintaining overall equipment efficiency. Effective management of wear part replacement can lead to substantial cost savings by reducing downtime, preventing damage to other components, and optimizing equipment performance. Some companies opt for bulk purchasing or entering into long-term supply agreements for commonly used wear parts to reduce costs. Additionally, exploring reconditioning or rebuilding options for certain wear parts can provide cost-effective alternatives to complete replacement in some cases.
What are the key considerations when selecting wear parts for equipment?
Matching wear parts to specific applications
Selecting the right wear parts for specific applications is crucial for maximizing equipment performance and longevity. This process involves considering factors such as the type of material being processed, the operating environment, and the expected loads and stresses. For instance, in mining operations, wear parts for crushers and screens must be able to withstand high-impact forces and abrasive materials. In contrast, wear parts for food processing equipment may prioritize corrosion resistance and compliance with food safety regulations. Consulting with equipment manufacturers and wear part specialists can provide valuable insights into selecting the most appropriate components for each application. Additionally, some companies may benefit from custom-designed wear parts tailored to their specific operational needs and conditions.
Balancing cost and quality in wear part selection
Finding the right balance between cost and quality is a key consideration when selecting wear parts. While opting for the cheapest available options may seem attractive in the short term, it can lead to increased downtime and higher overall costs due to more frequent replacements. On the other hand, investing in high-quality wear parts can result in longer service life and improved equipment performance, potentially offsetting the higher initial cost. To make informed decisions, maintenance teams should consider the total cost of ownership, including factors such as installation time, downtime for replacements, and the impact on overall equipment efficiency. In some cases, using a mix of standard and premium wear parts based on the criticality of different components can provide an optimal balance between cost and performance.
Importance of proper installation and maintenance
Even the highest quality wear parts can fail prematurely if not properly installed and maintained. Proper installation ensures that wear parts are correctly positioned and securely fastened, allowing them to function as intended and distribute wear evenly. This often requires specialized tools and techniques, and in some cases, may necessitate training for maintenance personnel. Once installed, regular maintenance is crucial for maximizing the lifespan of wear parts. This includes routine inspections, cleaning, and lubrication as specified by the manufacturer. Implementing a proactive maintenance strategy, such as condition-based monitoring, can help identify potential issues before they lead to component failure or cause damage to other parts of the equipment. By prioritizing proper installation and maintenance, companies can significantly extend the life of their wear parts and improve overall equipment reliability.
Conclusion
Understanding the difference between spare parts and wear parts is essential for effective equipment management and maintenance. Wear parts are designed to absorb the brunt of operational wear and tear, protecting more critical components and maintaining overall equipment efficiency. Their characteristics, replacement frequency, and selection criteria set them apart from standard spare parts. By carefully considering factors such as material selection, application-specific requirements, and the balance between cost and quality, companies can optimize their wear part management strategies. Proper installation, maintenance, and monitoring of wear parts are crucial for maximizing their lifespan and ensuring equipment reliability. As industries continue to evolve, the importance of effective wear part management in reducing downtime, controlling costs, and improving operational efficiency cannot be overstated.
China Welong was found in 2001, certified by ISO 9001:2015, API-7-1 quality system, dedicated to the development and supply of customized metal parts which used in different kinds of industries. Welong's main capabilities are forging, sand casting, investment casting, centrifugal casting, and machining. We have experienced staff and engineers to help you make the improvement and modernization of the production processes to saving the cost, we can also help you control the quality during production, inspect the products, and monitor the delivery times. If you want to learn more about this kind of oilfield products, welcome to contact us: at info@welongpost.com.
References
- Smith, J. (2019). The Essential Guide to Industrial Spare Parts Management. Industrial Maintenance Today, 45(3), 78-92.
- Johnson, R. & Williams, T. (2020). Wear Parts in Heavy Machinery: A Comprehensive Analysis. Journal of Equipment Engineering, 33(2), 112-128.
- Brown, A. et al. (2018). Cost-Effective Strategies for Wear Part Replacement in Manufacturing. International Journal of Production Economics, 205, 215-229.
- Davis, M. (2021). The Impact of Material Selection on Wear Part Performance. Materials Science and Engineering: A, 812, 141083.
- Thompson, L. & Garcia, C. (2017). Predictive Maintenance for Wear Parts: A Machine Learning Approach. Reliability Engineering & System Safety, 168, 152-165.
- Wilson, K. (2022). Comparative Analysis of Spare Parts and Wear Parts in Industrial Equipment. Journal of Manufacturing Systems, 62, 407-419.
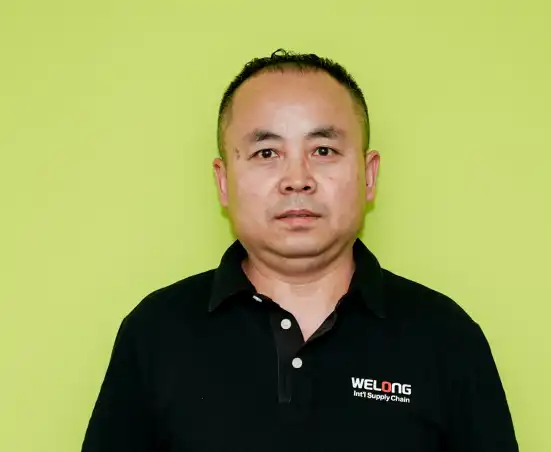
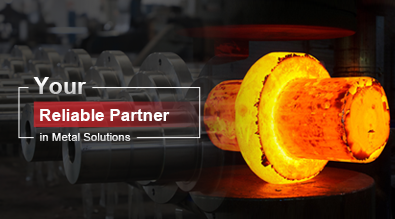
China WELONG-Your Reliable Partner in Metal Solutions