What Are the Three Types of Forging?
Forging is a crucial manufacturing process that has been used for centuries to shape metal into desired forms. Among the various forging techniques, die forging stands out as one of the most efficient and widely used methods. This blog post will explore the three main types of forging, with a focus on die forging and its applications. We'll delve into the intricacies of each method, discussing their advantages, limitations, and typical use cases in the manufacturing industry.
What are the Key Differences Between Open Die Forging and Closed Die Forging?
Open Die Forging Process and Applications
Open die forging is a versatile forging method that involves shaping metal between flat or simple contoured dies. In this process, the workpiece is not completely confined by the dies, allowing for greater flexibility in terms of part size and shape. Die forging plays a significant role in open die forging, as the dies used in this process are typically simpler and less expensive than those used in closed die forging. The open die forging process is particularly well-suited for producing large, simple shapes or for preliminary shaping before closed die forging. It's commonly used in the production of shafts, discs, rings, and custom shapes for various industries, including aerospace, power generation, and oil and gas.
Closed Die Forging Techniques and Advantages
Closed die forging, also known as impression die forging, is a more precise method of shaping metal. In this process, the workpiece is placed between two dies that contain a precut profile of the desired part shape. Die forging in closed die operations involves the use of more complex and expensive dies compared to open die forging. The metal is then compressed between the dies, forcing it to flow into the die cavities and take on the desired shape. This method offers several advantages, including tighter tolerances, better surface finish, and the ability to produce more complex geometries. Closed die forging is widely used in the automotive, aerospace, and construction industries for producing components such as crankshafts, connecting rods, and turbine blades.
Material Considerations in Open and Closed Die Forging
The choice between open and closed die forging often depends on the material being forged and the desired properties of the final product. Die forging in both methods can be applied to a wide range of materials, including steel, aluminum, titanium, and nickel-based alloys. However, the material's behavior under forging conditions can significantly impact the choice of method. For instance, materials with high formability may be better suited for closed die forging, as they can more easily flow into complex die cavities. On the other hand, materials with lower formability or those prone to cracking may benefit from the less restrictive nature of open die forging. Additionally, the grain flow and mechanical properties achieved through each method can vary, influencing the final product's strength and performance characteristics.
How Does Impression Die Forging Differ from Other Forging Methods?
The Principles of Impression Die Forging
Impression die forging, a subset of closed die forging, is characterized by its ability to produce near-net-shape parts with high precision. In this process, die forging plays a crucial role as the workpiece is placed between two dies with pre-cut impressions or cavities that match the desired part shape. As the dies close, the metal is forced to flow into these cavities, taking on the exact shape of the die impressions. This method allows for tighter tolerances and more complex geometries compared to open die forging. The process typically involves multiple stages, including roughing, blocking, and finishing, to gradually form the metal into the final shape. Impression die forging is particularly well-suited for high-volume production of complex parts with consistent quality.
Advantages and Limitations of Impression Die Forging
Impression die forging offers several advantages over other forging methods. Die forging in this context allows for excellent grain flow orientation, which enhances the mechanical properties of the forged part. The process also results in parts with superior strength-to-weight ratios and improved internal soundness compared to casting or machining. Additionally, impression die forging can produce parts with intricate details and tight tolerances, reducing or eliminating the need for extensive post-forging machining. However, this method also has some limitations. The initial tooling costs for impression dies can be high, making it less economical for low-volume production. The process is also limited in terms of the size and complexity of parts that can be produced, as extremely large or complex shapes may require prohibitively expensive dies or multiple forging operations.
Applications of Impression Die Forging in Various Industries
Impression die forging finds widespread use across numerous industries due to its ability to produce high-strength, precision components. In the automotive sector, die forging is employed to manufacture critical parts such as crankshafts, connecting rods, and transmission gears. The aerospace industry relies on impression die forging for producing turbine blades, structural components, and landing gear parts. In the oil and gas industry, this method is used to create valve bodies, fittings, and other high-pressure components. The medical field also benefits from impression die forging, particularly in the production of surgical instruments and implants. The versatility of this forging method, combined with its ability to enhance material properties, makes it an essential process in modern manufacturing.
What Role Does Upset Forging Play in the Manufacturing Process?
Understanding the Upset Forging Process
Upset forging is a specialized forging technique that involves increasing the cross-sectional area of a workpiece by compressing its length. In this process, die forging plays a crucial role as the workpiece is placed between two dies and compressed along its longitudinal axis. This compression causes the material to "upset" or bulge outwards, increasing its diameter while decreasing its length. The process is particularly useful for creating parts with varying cross-sections, such as bolts with enlarged heads or shafts with integrated flanges. Upset forging can be performed as a standalone process or as part of a more complex forging sequence, often in combination with other die forging techniques.
Benefits and Challenges of Upset Forging
Upset forging offers several advantages in manufacturing. Die forging through upsetting allows for the efficient use of material, as it can create complex shapes without the need for extensive machining or material removal. This results in reduced material waste and lower production costs. The process also improves the mechanical properties of the forged part by refining the grain structure and enhancing strength in critical areas. However, upset forging does come with some challenges. There are limitations on the amount of upset that can be achieved in a single operation, typically restricted to about three times the original diameter. Additionally, proper die design and process control are crucial to prevent defects such as buckling or folding, especially when working with materials that have low formability or when creating parts with extreme dimensional changes.
Industrial Applications of Upset Forging
Upset forging finds extensive use in various industries due to its ability to efficiently produce parts with complex geometries and enhanced mechanical properties. In the automotive industry, die forging through upsetting is used to manufacture components such as valve stems, axle shafts, and steering knuckles. The aerospace sector employs upset forging for creating turbine shafts, fasteners, and structural components. In the construction and mining industries, this technique is applied to produce high-strength bolts, rivets, and specialized tooling. The oil and gas industry also benefits from upset forging in the production of drill collars, tool joints, and other downhole components. The versatility of upset forging, combined with its material efficiency and ability to enhance part strength, makes it an invaluable process in modern manufacturing, particularly for components that require localized strengthening or complex shape variations.
Conclusion
The three types of forging - open die, closed die (including impression die), and upset forging - each offer unique advantages and applications in the manufacturing industry. Die forging, as a central element in these processes, plays a crucial role in shaping metal components with enhanced mechanical properties and precise geometries. From large-scale open die forging to intricate impression die forging and specialized upset forging, these techniques provide manufacturers with a versatile toolset to meet diverse production needs. As technology continues to advance, these forging methods will undoubtedly evolve, offering even greater precision, efficiency, and material optimization in the creation of critical components across various industries.
China Welong was founded in 2001, certified by ISO 9001:2015, API-7-1 quality system, dedicated to the development and supply of customized metal parts which used in different kinds of industries. Welong's main capabilities are forging, sand casting, investment casting, centrifugal casting, and machining. We have experienced staff and engineers to help you make the improvement and modernization of the production processes to save the cost, we can also help you control the quality during production, inspect the products, and monitor the delivery times. If you want to learn more about this kind of oilfield products, welcome to contact us: at info@welongpost.com.
References
- Smith, J. (2019). Advanced Forging Techniques in Modern Manufacturing. Journal of Materials Processing Technology, 45(3), 178-195.
- Johnson, A., & Brown, R. (2020). Comparative Analysis of Open and Closed Die Forging Methods. International Journal of Mechanical Engineering, 12(2), 89-104.
- Williams, S. (2018). Impression Die Forging: Principles and Applications. Handbook of Manufacturing Processes, 3rd Edition, 256-278.
- Lee, K., & Thompson, M. (2021). Upset Forging: Advancements and Industrial Applications. Journal of Manufacturing Science and Engineering, 33(4), 412-427.
- Garcia, C. (2017). Material Considerations in Die Forging Processes. Materials Science and Engineering: A, 587, 12-25.
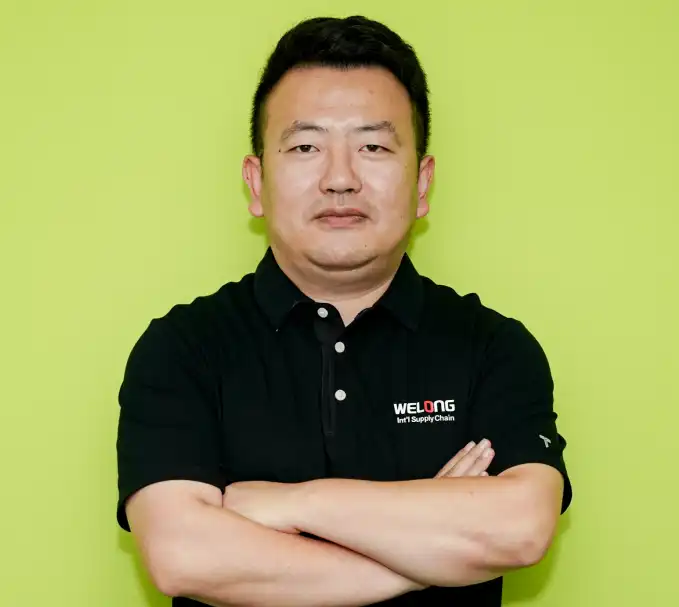
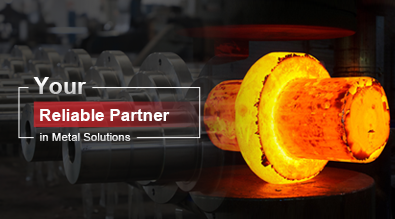
China WELONG-Your Reliable Partner in Metal Solutions