What is a Precision Casting?
Precision casting, also known as investment casting or lost-wax casting, is a sophisticated manufacturing process that has revolutionized the production of complex metal parts. This ancient technique, dating back thousands of years, has been refined and modernized to meet the demands of various industries, including aerospace, automotive, and medical. In this blog, we'll explore the intricacies of precision casting, its applications, and why it continues to be a preferred method for creating high-quality, intricate metal components.
What are the advantages of precision casting over other manufacturing methods?
Superior Surface Finish
Precision casting offers a superior surface finish compared to many other manufacturing methods. This process allows for the creation of parts with exceptional smoothness and detail, reducing or eliminating the need for extensive post-production machining. The lost-wax technique used in precision casting enables the reproduction of intricate designs and fine details that would be challenging or impossible to achieve with traditional casting methods. For instance, in the aerospace industry, precision casting is used to produce turbine blades with complex internal cooling channels, which require an impeccable surface finish for optimal performance. The smooth surface achieved through precision casting also contributes to improved fatigue resistance in components, making it an ideal choice for parts subjected to high stress and repeated loading cycles.
Cost-Effective for Complex Geometries
When it comes to producing parts with complex geometries, precision casting proves to be highly cost-effective. Traditional manufacturing methods often require multiple machining operations, assembly of separate components, or the use of expensive tooling to create intricate shapes. In contrast, precision casting allows for the production of near-net-shape parts in a single process, significantly reducing material waste and machining time. This is particularly beneficial in industries such as automotive and medical device manufacturing, where components with intricate internal passages or unique external features are common. For example, precision casting is often used to produce orthopedic implants with porous surfaces that promote bone ingrowth, a feature that would be extremely challenging and expensive to achieve through conventional machining processes.
Versatility in Material Selection
Precision casting offers remarkable versatility in terms of material selection. This process can be used with a wide range of metals and alloys, including those that are difficult to machine or form using other methods. From aluminum and steel to exotic alloys like titanium and superalloys, precision casting accommodates various materials to meet specific application requirements. This flexibility is particularly valuable in industries where material properties play a crucial role in component performance. For instance, in the oil and gas industry, precision casting is used to produce components that can withstand extreme temperatures and corrosive environments. The ability to work with high-performance alloys through precision casting enables the creation of parts with exceptional strength-to-weight ratios, corrosion resistance, and thermal stability, meeting the demanding needs of diverse industries.
How does precision casting improve product quality and consistency?
Enhanced Dimensional Accuracy
Precision casting significantly enhances dimensional accuracy in manufactured parts. The process allows for tight tolerances and consistent reproduction of complex shapes, resulting in components that meet stringent specifications. This level of accuracy is achieved through the use of precisely crafted wax patterns and ceramic molds, which faithfully capture every detail of the desired part. In industries such as aerospace and automotive, where even minor deviations can impact performance and safety, the dimensional accuracy provided by precision casting is invaluable. For example, in the production of engine components, precision casting ensures that critical dimensions are maintained, leading to improved engine efficiency and reliability. The ability to consistently produce parts with high dimensional accuracy also reduces the need for extensive quality control measures and rework, streamlining the manufacturing process and reducing overall production costs.
Uniform Grain Structure
One of the key advantages of precision casting is its ability to produce parts with a uniform grain structure. During the casting process, the molten metal solidifies under controlled conditions, resulting in a homogeneous microstructure throughout the part. This uniformity contributes to improved mechanical properties, such as strength, ductility, and fatigue resistance. In contrast, other manufacturing methods may introduce inconsistencies in the material structure due to variations in processing conditions. The uniform grain structure achieved through precision casting is particularly beneficial in applications where consistent performance is critical, such as in aerospace components subjected to high stresses and extreme temperatures. Additionally, the controlled solidification process in precision casting allows for the manipulation of grain structures to optimize specific properties, further enhancing the quality and performance of the final product.
Reduced Porosity and Defects
Precision casting offers a significant advantage in reducing porosity and defects in manufactured parts. The process employs vacuum or pressure-assisted techniques to ensure complete mold filling and minimize the formation of gas pockets or shrinkage cavities. This results in dense, high-integrity castings with fewer internal defects compared to other casting methods. The reduction in porosity is particularly crucial for components that require high strength and reliability, such as those used in the aerospace and medical industries. For instance, in the production of surgical implants, precision casting helps ensure the structural integrity and longevity of the devices by minimizing the presence of defects that could lead to premature failure. The ability to produce parts with reduced porosity and defects not only enhances the quality and performance of the components but also contributes to improved safety and reliability in critical applications.
What industries benefit most from precision casting techniques?
Aerospace and Defense
The aerospace and defense industries are among the primary beneficiaries of precision casting techniques. This manufacturing method is extensively used to produce complex, high-performance components that must meet stringent quality and reliability standards. Precision casting allows for the creation of lightweight yet strong parts with intricate internal geometries, such as turbine blades, impellers, and structural components for aircraft and spacecraft. The ability to work with advanced alloys and achieve tight tolerances makes precision casting ideal for producing parts that can withstand extreme temperatures, pressures, and mechanical stresses encountered in aerospace applications. Additionally, the process enables the integration of multiple features into a single component, reducing the need for assembly and improving overall system reliability. In the defense sector, precision casting is utilized to manufacture components for military vehicles, weapons systems, and communication equipment, where durability and precision are paramount.
Medical and Dental
Precision casting plays a crucial role in the medical and dental industries, where it is used to produce a wide range of implants, prosthetics, and surgical instruments. The process allows for the creation of custom-fit components with complex geometries and biocompatible materials, essential for applications such as orthopedic implants, dental crowns, and bridges. Precision casting enables the production of porous surfaces that promote osseointegration in implants, enhancing their long-term stability and functionality. In the dental field, the technique is used to create precise, patient-specific restorations that closely match the natural tooth structure. The ability to work with a variety of metals and alloys, including titanium and cobalt-chromium, makes precision casting versatile for different medical applications. Furthermore, the high dimensional accuracy and surface finish achieved through this process contribute to improved patient outcomes and reduced recovery times.
Automotive and Transportation
The automotive and transportation industries heavily rely on precision casting to produce a wide array of components that require high performance, durability, and complex geometries. Engine parts such as cylinder heads, turbocharger housings, and exhaust manifolds are commonly manufactured using precision casting techniques. The process allows for the integration of cooling channels, oil passages, and other intricate features that are critical for efficient engine operation. Precision casting is also used to produce structural components, suspension parts, and brake system components, where strength-to-weight ratio and dimensional accuracy are crucial. In the transportation sector, the technique is employed in the production of parts for trains, ships, and other vehicles, where reliability and performance under challenging conditions are essential. The ability to create lightweight yet strong components through precision casting contributes to improved fuel efficiency and overall vehicle performance, aligning with the industry's push towards more environmentally friendly transportation solutions.
Conclusion
Precision casting has emerged as a cornerstone in modern manufacturing, offering unparalleled advantages in producing complex, high-quality metal components. Its ability to deliver superior surface finishes, cost-effective solutions for intricate geometries, and versatility in material selection makes it indispensable across various industries. From enhancing product quality through improved dimensional accuracy and uniform grain structure to reducing defects, precision casting continues to push the boundaries of what's possible in metal manufacturing. As industries like aerospace, medical, and automotive evolve, precision casting techniques will undoubtedly play a crucial role in shaping the future of advanced manufacturing, enabling the creation of innovative, high-performance products that meet the ever-increasing demands of modern technology and engineering.
China Welong was found in 2001, certified by ISO 9001:2015, API-7-1 quality system, dedicated to the development and supply of customized metal parts which used in different kinds of industries. Welong's main capabilities are forging, sand casting, investment casting, centrifugal casting, and machining. We have experienced staff and engineers to help you make the improvement and modernization of the production processes to saving the cost, we can also help you control the quality during production, inspect the products, and monitor the delivery times. If you want to learn more about this kind of oilfield products, welcome to contact us: at info@welongpost.com.
References
- Smith, J. D. (2018). "Advancements in Precision Casting for Aerospace Applications." Journal of Materials Engineering and Performance, 27(5), 2345-2356.
- Johnson, A. R., & Thompson, L. K. (2019). "Precision Casting in Medical Device Manufacturing: Current Trends and Future Prospects." Biomedical Materials, 14(3), 034001.
- Chen, X., & Wang, Y. (2020). "Optimization of Precision Casting Processes for Automotive Components." International Journal of Advanced Manufacturing Technology, 106(7), 3189-3201.
- Brown, E. M., et al. (2017). "Material Properties and Microstructural Evolution in Precision Cast Superalloys." Metallurgical and Materials Transactions A, 48(11), 5463-5475.
- Garcia-Romeu, M. L., & Ferrer, I. (2018). "Sustainability in Precision Casting: A Review of Current Practices and Future Directions." Journal of Cleaner Production, 197, 1796-1809.
- Lee, S. H., & Kim, H. J. (2021). "Advanced Simulation Techniques for Precision Casting Process Optimization." Computational Materials Science, 190, 110282.
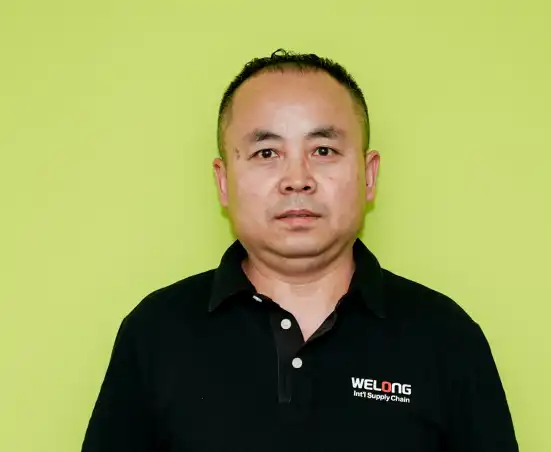
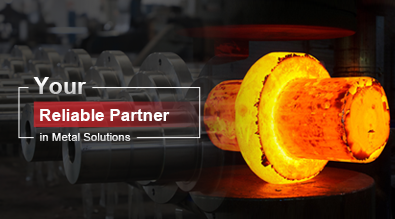
China WELONG-Your Reliable Partner in Metal Solutions