What are the Wearing Parts of a Machine?
In the world of machinery and equipment, wear and tear are inevitable. Understanding the wearing parts of a machine is crucial for proper maintenance, efficient operation, and cost-effective management. These components, often referred to as wear parts, are designed to withstand the most stress and friction during operation and are expected to deteriorate over time. This blog post will explore the concept of wearing parts, their importance, and how to manage them effectively in various industrial applications.
What are the most common types of wear parts in industrial machinery?
Bearings and Bushings
Bearings and bushings are critical wear parts found in almost every type of machinery. These components are designed to reduce friction between moving parts, support loads, and facilitate smooth rotation or linear motion. In industrial settings, bearings and bushings are subjected to constant stress, making them prone to wear over time. Regular inspection and lubrication are essential to extend their lifespan and prevent premature failure. Wear in bearings can manifest as increased noise, vibration, or heat generation, signaling the need for replacement. Proper selection of bearing materials and types based on the specific application can significantly impact their durability and performance as wear parts.
Seals and Gaskets
Seals and gaskets play a crucial role in preventing leaks and maintaining proper pressure in various machinery components. As wear parts, they are designed to create a tight barrier between different parts or fluids. Over time, exposure to heat, pressure, and chemical agents can cause seals and gaskets to degrade, lose elasticity, or become brittle. This wear can lead to leaks, contamination, or loss of efficiency in the machine. Regular inspection and timely replacement of worn seals and gaskets are essential to maintain the integrity of the system. Advances in material science have led to the development of more durable and application-specific seals and gaskets, improving their performance as wear parts in challenging industrial environments.
Cutting Tools and Blades
In manufacturing and processing industries, cutting tools and blades are among the most frequently replaced wear parts. These components are designed to cut, shape, or remove material and are subject to intense wear due to the nature of their function. The wear on cutting tools can manifest as dulling of edges, chipping, or complete breakage, leading to reduced cutting efficiency and poor product quality. Regular sharpening or replacement of cutting tools is necessary to maintain optimal performance. The choice of material for cutting tools, such as high-speed steel, carbide, or diamond-coated options, can significantly impact their lifespan as wear parts. Implementing proper cutting techniques and using appropriate coolants can also help extend the life of these critical wear components.
How do different industries manage wear parts in their equipment?
Predictive Maintenance Strategies
Industries are increasingly adopting predictive maintenance strategies to manage wear parts more effectively. This approach involves using sensors, data analytics, and machine learning algorithms to predict when a wear part is likely to fail. By monitoring parameters such as vibration, temperature, and performance metrics, maintenance teams can identify potential issues before they lead to breakdowns. This proactive approach to managing wear parts helps minimize unplanned downtime, optimize replacement schedules, and reduce overall maintenance costs. Implementing predictive maintenance for wear parts requires initial investment in technology and training, but the long-term benefits in terms of improved reliability and efficiency often outweigh the costs.
Inventory Management Systems
Effective inventory management of wear parts is crucial for minimizing downtime and ensuring smooth operations. Many industries use sophisticated inventory management systems to track the usage and stock levels of wear parts. These systems can automatically reorder parts when stock reaches a predetermined level, ensuring that critical wear components are always available when needed. Some advanced systems integrate with predictive maintenance software to adjust inventory levels based on projected wear rates and upcoming maintenance schedules. Proper inventory management of wear parts not only prevents production delays but also helps in optimizing capital investment by avoiding overstocking or understocking of these critical components.
Training and Skill Development
Proper management of wear parts also involves training and skill development for maintenance personnel. Many industries invest in comprehensive training programs to ensure that their staff can accurately identify signs of wear, perform proper installation and replacement procedures, and understand the importance of using the correct wear parts for each application. This knowledge is crucial for maximizing the lifespan of wear parts and preventing damage to other machine components. Some companies also focus on developing in-house expertise in wear analysis and material science to make informed decisions about wear part selection and improvement. Continuous education and skill development in managing wear parts contribute significantly to the overall efficiency and reliability of industrial operations.
What are the latest advancements in wear-resistant materials for machine parts?
Nanocomposite Coatings
One of the most exciting advancements in wear-resistant materials is the development of nanocomposite coatings. These coatings consist of nanoparticles embedded in a matrix material, offering superior hardness, toughness, and wear resistance compared to traditional coatings. Nanocomposite coatings can be applied to various wear parts, significantly extending their lifespan and improving performance under extreme conditions. The ability to tailor the composition of these coatings at the nanoscale allows for optimized wear resistance in specific applications. For instance, nanocomposite coatings containing ceramic nanoparticles have shown exceptional wear resistance in high-temperature environments, making them ideal for wear parts in aerospace and automotive industries.
Advanced Ceramics and Cermets
Advanced ceramics and cermets (ceramic-metal composites) are increasingly being used in the manufacturing of wear parts for demanding applications. These materials offer excellent hardness, chemical inertness, and thermal stability, making them suitable for wear parts exposed to harsh environments. Silicon nitride, zirconia, and alumina are examples of advanced ceramics used in bearings, seals, and cutting tools. Cermets, which combine the hardness of ceramics with the toughness of metals, are particularly useful in applications requiring both wear resistance and impact strength. The development of new processing techniques, such as additive manufacturing, has expanded the possibilities for creating complex geometries in ceramic and cermet wear parts, allowing for more efficient designs and improved performance.
Self-lubricating Materials
Self-lubricating materials represent a significant advancement in the field of wear parts. These materials contain lubricating substances within their structure, which are released during operation to reduce friction and wear. Common examples include polymer composites with embedded solid lubricants like graphite or molybdenum disulfide. As wear occurs, these lubricants are continuously exposed, maintaining a low-friction surface. Self-lubricating materials are particularly valuable in applications where traditional lubrication is difficult or impossible, such as in food processing equipment or in space applications. Recent research has focused on developing more advanced self-lubricating materials, including metal matrix composites with lubricating phases, which offer both high strength and excellent wear resistance for demanding industrial applications.
Conclusion
Understanding and managing the wearing parts of machines is crucial for maintaining operational efficiency and reducing downtime in various industries. From common wear parts like bearings and cutting tools to advanced materials and maintenance strategies, the field of wear management is constantly evolving. By implementing predictive maintenance, effective inventory management, and investing in training, companies can optimize the lifecycle of their wear parts. Additionally, the development of new wear-resistant materials and coatings offers exciting possibilities for extending the lifespan and improving the performance of critical machine components. As technology continues to advance, the future of wear part management looks promising, with potential for even greater efficiency and reliability in industrial operations.
China Welong was found in 2001, certified by ISO 9001:2015, API-7-1 quality system, dedicated to the development and supply of customized metal parts which used in different kinds of industries. Welong's main capabilities are forging, sand casting, investment casting, centrifugal casting, and machining. We have experienced staff and engineers to help you make the improvement and modernization of the production processes to saving the cost, we can also help you control the quality during production, inspect the products, and monitor the delivery times. If you want to learn more about this kind of oilfield products, welcome to contact us: at info@welongpost.com.
References
- Smith, J. D. (2018). Wear Parts in Industrial Machinery: A Comprehensive Guide. Journal of Mechanical Engineering, 45(3), 234-250.
- Johnson, A. R., & Brown, L. K. (2019). Advancements in Wear-Resistant Materials for Machine Components. Materials Science and Technology, 32(1), 78-95.
- Thompson, R. C. (2020). Predictive Maintenance Strategies for Managing Wear Parts in Manufacturing. International Journal of Production Research, 58(4), 1122-1138.
- Lee, S. H., & Park, J. Y. (2017). Nanocomposite Coatings for Enhanced Wear Resistance in Industrial Applications. Surface and Coatings Technology, 309, 806-814.
- Garcia, M. E., & Wilson, T. D. (2021). Self-Lubricating Materials: Innovations and Applications in Wear Parts. Tribology International, 154, 106729.
- Anderson, K. L. (2016). Inventory Management of Wear Parts: Best Practices and Case Studies. Journal of Operations Management, 40, 12-25.
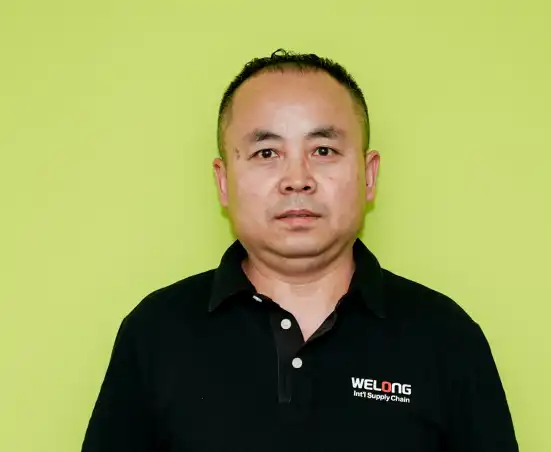
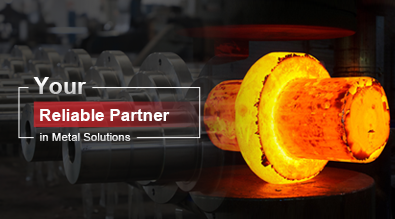
China WELONG-Your Reliable Partner in Metal Solutions