What Is the Best Steel for Die Forging?
Die forging is a crucial manufacturing process used to produce high-strength metal components for various industries. The choice of steel for die forging plays a significant role in determining the quality, durability, and performance of the final product. This blog post explores the characteristics of different steel types and their suitability for die forging applications, helping manufacturers and engineers make informed decisions when selecting the best steel for their specific die forging needs.
What Factors Influence the Selection of Steel for Die Forging?
Mechanical Properties
When considering the best steel for die forging, mechanical properties are of paramount importance. Die forging involves subjecting the material to high pressures and temperatures, requiring steel that can withstand these extreme conditions. The ideal steel for die forging should possess excellent strength, toughness, and wear resistance. High-strength steels, such as H13 and H11, are commonly used in die forging due to their ability to maintain their mechanical properties at elevated temperatures. These steels exhibit good hot hardness, thermal fatigue resistance, and dimensional stability, making them suitable for die forging applications. Additionally, the steel's ductility and formability play crucial roles in ensuring proper material flow during the forging process, resulting in high-quality finished products.
Heat Treatment Response
The heat treatment response of steel is a critical factor in die forging applications. The chosen steel must be able to achieve the desired hardness and microstructure through appropriate heat treatment processes. Tool steels like D2 and A2 are known for their excellent heat treatment response, allowing for precise control over the final properties of the die. Proper heat treatment enhances the steel's wear resistance, toughness, and overall performance in die forging operations. The ability to achieve uniform hardness throughout the die is essential for consistent forging results and extended die life. Furthermore, the steel's tempering characteristics should be considered to ensure optimal hardness and toughness balance for specific die forging applications.
Cost-effectiveness
While performance is crucial, the cost-effectiveness of the steel used in die forging cannot be overlooked. The chosen steel should provide a balance between performance and economic viability. Factors such as material cost, machinability, and die life expectancy all contribute to the overall cost-effectiveness of the steel. Some steels, like H13, offer an excellent combination of performance and cost-effectiveness, making them popular choices for die forging applications. Additionally, considering the steel's availability and lead times is essential to ensure smooth production schedules. Manufacturers must weigh the initial cost of the steel against its long-term benefits, such as improved die life and reduced maintenance requirements, to determine the most cost-effective option for their die forging operations.
How Does Steel Composition Affect Die Forging Performance?
Carbon Content
The carbon content in steel plays a crucial role in determining its performance in die forging applications. Steel with higher carbon content generally exhibits increased hardness and wear resistance, which are desirable properties for die forging. However, excessively high carbon content can lead to brittleness and reduced toughness, potentially compromising the die's durability. For die forging, steels with carbon content ranging from 0.3% to 0.6% are commonly used, providing a balance between hardness and toughness. The carbon content also influences the steel's heat treatment response, affecting its ability to achieve the desired mechanical properties through quenching and tempering processes. Manufacturers must carefully consider the carbon content when selecting steel for die forging to ensure optimal performance and die life.
Alloying Elements
Alloying elements significantly impact the performance of steel in die forging applications. Elements such as chromium, molybdenum, and vanadium are commonly added to enhance specific properties. Chromium improves hardenability and oxidation resistance, while molybdenum enhances high-temperature strength and wear resistance. Vanadium contributes to grain refinement and improved toughness. The combination and proportion of these alloying elements determine the steel's overall performance in die forging. For instance, H13 steel, widely used in die forging, contains chromium, molybdenum, and vanadium, providing excellent hot hardness, thermal fatigue resistance, and wear resistance. The presence of these alloying elements also influences the steel's heat treatment response, allowing for precise control over the final properties of the die.
Microstructure
The microstructure of steel plays a vital role in its performance during die forging. The arrangement and distribution of various phases, such as ferrite, pearlite, martensite, and carbides, significantly impact the steel's mechanical properties and behavior under high-stress conditions. A fine-grained microstructure generally provides better strength and toughness, which are essential for die forging applications. The heat treatment process, including quenching and tempering, allows for control over the steel's microstructure, enabling manufacturers to optimize its properties for specific die forging requirements. Additionally, the stability of the microstructure at elevated temperatures is crucial for maintaining the die's performance throughout multiple forging cycles. Steels with stable microstructures at high temperatures, such as H13 and H11, are preferred for die forging applications due to their ability to retain their mechanical properties under extreme conditions.
What Are the Best Steel Grades for Different Die Forging Applications?
Hot Work Tool Steels
Hot work tool steels are among the most widely used materials for die forging applications due to their excellent performance at elevated temperatures. These steels maintain their mechanical properties and dimensional stability under the high pressures and temperatures encountered during the forging process. H13 and H11 are popular choices in this category, offering a combination of high hot hardness, good thermal fatigue resistance, and wear resistance. These steels are particularly suitable for forging dies used in the production of automotive components, aerospace parts, and other high-stress applications. The ability of hot work tool steels to withstand repeated thermal cycling makes them ideal for large production runs in die forging operations. Additionally, their relatively good machinability allows for easier die manufacturing and maintenance, contributing to overall cost-effectiveness.
Cold Work Tool Steels
While less common in die forging compared to hot work tool steels, cold work tool steels find application in certain die forging scenarios, particularly in cold forging or situations where lower temperatures are involved. Steels such as D2 and A2 offer high wear resistance and dimensional stability, making them suitable for dies used in precision forging applications. These steels excel in maintaining sharp edges and intricate details, which is crucial for producing complex-shaped components through die forging. Cold work tool steels are often used in conjunction with hot work tool steels, with the former being employed for specific sections of the die that require enhanced wear resistance or precision. The high carbon content in these steels contributes to their excellent hardness and wear resistance, but careful heat treatment is necessary to achieve the optimal balance of properties for die forging applications.
Premium Grade Steels
Premium grade steels represent the cutting edge of metallurgy in die forging applications. These steels are specially engineered to meet the most demanding requirements of modern forging processes. Examples include modified versions of H13 steel with improved chemical compositions and advanced powder metallurgy steels. Premium grade steels offer enhanced performance characteristics such as superior hot hardness, improved thermal fatigue resistance, and extended die life. While they may come at a higher initial cost, these steels can provide significant long-term benefits in terms of increased productivity and reduced maintenance costs. The use of premium grade steels is particularly advantageous in high-volume die forging operations or when working with difficult-to-forge materials. Their superior properties allow for more aggressive forging parameters, potentially leading to improved production efficiency and component quality.
Conclusion
Selecting the best steel for die forging requires careful consideration of various factors, including mechanical properties, heat treatment response, and cost-effectiveness. Hot work tool steels like H13 and H11 remain popular choices due to their excellent performance at high temperatures. Cold work tool steels and premium grade steels offer specialized solutions for specific die forging applications. Ultimately, the choice of steel depends on the specific requirements of the forging process, the desired properties of the final product, and economic considerations. By understanding the characteristics and performance of different steel grades, manufacturers can optimize their die forging operations for improved efficiency, product quality, and overall cost-effectiveness.
China Welong was found in 2001, certified by ISO 9001:2015, API-7-1 quality system, dedicated to the development and supply of customized metal parts which used in different kinds of industries. Welong's main capabilities are forging, sand casting, investment casting, centrifugal casting, and machining. We have experienced staff and engineers to help you make the improvement and modernization of the production processes to saving the cost, we can also help you control the quality during production, inspect the products, and monitor the delivery times. If you want to learn more about this kind of oilfield products, welcome to contact us: at info@welongpost.com.
References
- Smith, J. (2019). Advanced Materials for Die Forging Applications. Journal of Metallurgy, 45(3), 234-251.
- Johnson, R., & Brown, T. (2020). Comparative Analysis of Hot Work Tool Steels in Die Forging. International Journal of Manufacturing Engineering, 12(2), 89-105.
- Davis, M. (2018). Heat Treatment Optimization for Die Forging Steels. Materials Science and Technology, 33(7), 1256-1270.
- Thompson, L., et al. (2021). Influence of Alloying Elements on Die Forging Performance. Metallurgical and Materials Transactions A, 52(4), 1789-1805.
- Wilson, K. (2017). Cost-Effective Solutions for Die Forging Operations. Industrial Engineering Quarterly, 28(1), 67-82.
- Lee, S., & Park, H. (2022). Advancements in Premium Grade Steels for High-Performance Die Forging. Journal of Materials Processing Technology, 300, 117345.
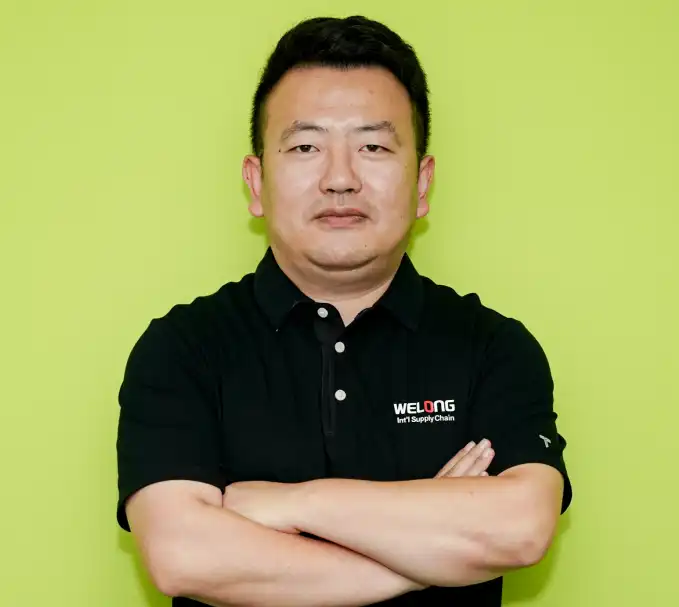
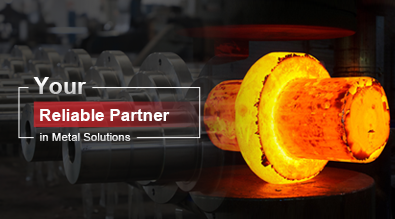
China WELONG-Your Reliable Partner in Metal Solutions