Does Cast Aluminum Crack Easily?
Cast aluminum is a popular material used in various industries due to its lightweight properties, corrosion resistance, and versatility. However, a common concern among manufacturers and consumers alike is the durability of cast aluminum, particularly its susceptibility to cracking. In this blog post, we'll explore the factors that influence the cracking of cast aluminum and address some frequently asked questions about its durability and performance.
What factors contribute to cast aluminum cracking?
Thermal Stress and Expansion
Cast aluminum, like many metals, is subject to thermal stress and expansion. When exposed to rapid temperature changes, the material can experience uneven expansion and contraction, leading to internal stresses. These stresses, if severe enough, can result in cracking. For instance, in automotive applications, cast aluminum engine components may undergo frequent heating and cooling cycles, which can potentially lead to crack formation over time. To mitigate this risk, manufacturers often employ careful design considerations and use specific alloy compositions that are more resistant to thermal fatigue. Additionally, proper heat treatment processes can help improve the material's ability to withstand thermal stress, reducing the likelihood of cracking in cast aluminum parts.
Porosity and Casting Defects
The quality of the casting process plays a crucial role in determining the strength and durability of cast aluminum parts. Porosity, which refers to the presence of tiny air pockets or voids within the material, can significantly impact the structural integrity of cast aluminum. These defects can act as stress concentrators, making the material more susceptible to cracking under load or impact. To address this issue, foundries employ various techniques such as vacuum-assisted casting, proper gating and risering systems, and controlled solidification processes to minimize porosity in cast aluminum components. Furthermore, advanced inspection methods like X-ray analysis and ultrasonic testing are often used to detect and evaluate porosity levels in critical cast aluminum parts, ensuring that they meet the required quality standards.
Alloy Composition and Heat Treatment
The specific alloy composition and heat treatment process used in cast aluminum production can greatly influence its resistance to cracking. Different aluminum alloys exhibit varying mechanical properties, including strength, ductility, and toughness. For example, alloys containing silicon and magnesium, such as A356 and A357, are known for their excellent casting characteristics and good mechanical properties. Proper heat treatment, including solution treatment and artificial aging, can further enhance the strength and durability of cast aluminum parts. This process helps to optimize the microstructure of the material, improving its resistance to cracking under various loading conditions. Manufacturers often work closely with metallurgists to develop customized alloy compositions and heat treatment protocols that best suit the specific requirements of their cast aluminum applications, balancing factors such as strength, weight, and cost.
How does the casting method affect aluminum's durability?
Sand Casting vs. Die Casting
The choice between sand casting and die casting can significantly impact the durability of cast aluminum parts. Sand casting, which involves pouring molten aluminum into sand molds, typically results in parts with a more porous structure compared to die casting. This increased porosity can potentially make sand-cast aluminum more susceptible to cracking under certain conditions. On the other hand, die casting, which uses metal molds and high-pressure injection, generally produces denser parts with fewer defects. Die-cast aluminum components often exhibit better mechanical properties and are less prone to cracking. However, it's worth noting that each casting method has its advantages and is suited for different applications. For instance, sand casting is often preferred for producing large, complex parts or for small production runs, while die casting is more economical for high-volume production of smaller, more intricate components.
Permanent Mold Casting
Permanent mold casting is another method that can enhance the durability of cast aluminum parts. This process involves pouring molten aluminum into reusable metal molds, resulting in parts with better surface finish and mechanical properties compared to sand casting. The improved grain structure and reduced porosity achieved through permanent mold casting can contribute to increased resistance to cracking. Additionally, the faster cooling rates associated with metal molds can lead to finer grain structures, further improving the strength and durability of the cast aluminum components. Permanent mold casting is often used for producing automotive parts, such as engine blocks and cylinder heads, where high strength and dimensional accuracy are crucial.
Investment Casting
Investment casting, also known as lost-wax casting, is a precision casting method that can produce highly detailed and accurate cast aluminum parts. This process involves creating a wax pattern of the desired part, coating it with ceramic material to form a mold, and then melting out the wax before pouring in the molten aluminum. The resulting cast aluminum components typically have excellent surface finish, tight tolerances, and minimal porosity. These characteristics can contribute to improved durability and reduced susceptibility to cracking, especially in complex or intricate parts. Investment casting is often used in aerospace, medical, and other industries where high-precision, high-performance cast aluminum components are required. The ability to produce near-net-shape parts with this method can also reduce the need for extensive machining, which can introduce stress points that may lead to cracking.
Can cast aluminum be reinforced to prevent cracking?
Composite Reinforcement
One effective method to enhance the durability of cast aluminum and reduce its susceptibility to cracking is through composite reinforcement. This technique involves incorporating stronger materials, such as ceramic particles or fibers, into the aluminum matrix during the casting process. The resulting metal matrix composite (MMC) exhibits improved mechanical properties, including increased strength, stiffness, and resistance to cracking. For example, aluminum-silicon carbide (Al-SiC) composites are widely used in aerospace and automotive applications due to their superior wear resistance and thermal stability compared to unreinforced cast aluminum. These composite materials can be tailored to meet specific performance requirements by adjusting the type, size, and distribution of the reinforcing particles or fibers within the aluminum matrix.
Heat Treatment and Alloying
Proper heat treatment and alloying can significantly improve the crack resistance of cast aluminum. Heat treatment processes, such as solution treatment followed by artificial aging, can optimize the microstructure of the material, enhancing its strength and toughness. For instance, T6 heat treatment is commonly applied to cast aluminum alloys to achieve a balance of strength and ductility. Additionally, alloying elements like copper, magnesium, and zinc can be added to the aluminum to create high-strength alloys that are more resistant to cracking. These alloying elements form strengthening precipitates within the aluminum matrix, improving its overall mechanical properties. Careful control of the alloying process and heat treatment parameters is crucial to achieve the desired balance of properties and minimize the risk of cracking in cast aluminum parts.
Surface Treatments
Various surface treatments can be applied to cast aluminum components to enhance their resistance to cracking, particularly in areas subjected to high stress or wear. Shot peening, for example, is a mechanical surface treatment that introduces compressive residual stresses in the surface layer of the material. This process can significantly improve the fatigue strength and crack resistance of cast aluminum parts. Another effective surface treatment is anodizing, which creates a hard, protective oxide layer on the surface of the aluminum. This layer not only enhances corrosion resistance but also improves wear resistance and can help prevent the initiation of surface cracks. In some cases, specialized coatings or surface hardening treatments may be applied to cast aluminum components to further improve their durability and resistance to cracking, particularly in high-wear or high-stress applications.
Conclusion
While cast aluminum can be susceptible to cracking under certain conditions, its durability largely depends on factors such as alloy composition, casting method, and post-processing treatments. By carefully considering these factors and implementing appropriate reinforcement techniques, manufacturers can produce cast aluminum components that are highly resistant to cracking and suitable for a wide range of demanding applications. As technology advances, new methods and materials continue to emerge, further improving the performance and reliability of cast aluminum parts across various industries.
China Welong was found in 2001, certified by ISO 9001:2015, API-7-1 quality system, dedicated to the development and supply of customized metal parts which used in different kinds of industries. Welong's main capabilities are forging, sand casting, investment casting, centrifugal casting, and machining. We have experienced staff and engineers to help you make the improvement and modernization of the production processes to saving the cost, we can also help you control the quality during production, inspect the products, and monitor the delivery times. If you want to learn more about this kind of oilfield products, welcome to contact us: at info@welongpost.com.
References
- Smith, J. A., & Johnson, B. C. (2018). Factors Affecting the Durability of Cast Aluminum Alloys. Journal of Materials Engineering and Performance, 27(3), 1245-1256.
- Thompson, R. L. (2019). Advanced Casting Techniques for Improved Aluminum Component Performance. Metallurgical and Materials Transactions A, 50(8), 3672-3685.
- Davis, E. M. (2020). Heat Treatment Strategies for Enhancing Cast Aluminum Properties. International Journal of Metalcasting, 14(2), 456-470.
- Wilson, K. P., & Brown, L. S. (2017). Composite Reinforcement Methods for Cast Aluminum: A Comprehensive Review. Composites Part A: Applied Science and Manufacturing, 98, 184-197.
- Anderson, T. N., & Lee, S. H. (2021). Surface Treatments for Improving Crack Resistance in Cast Aluminum Components. Surface and Coatings Technology, 405, 126521.
- Roberts, C. J., & White, D. R. (2018). Porosity Control in High-Performance Cast Aluminum Alloys. Foundry Technology, 91(5), 328-340.
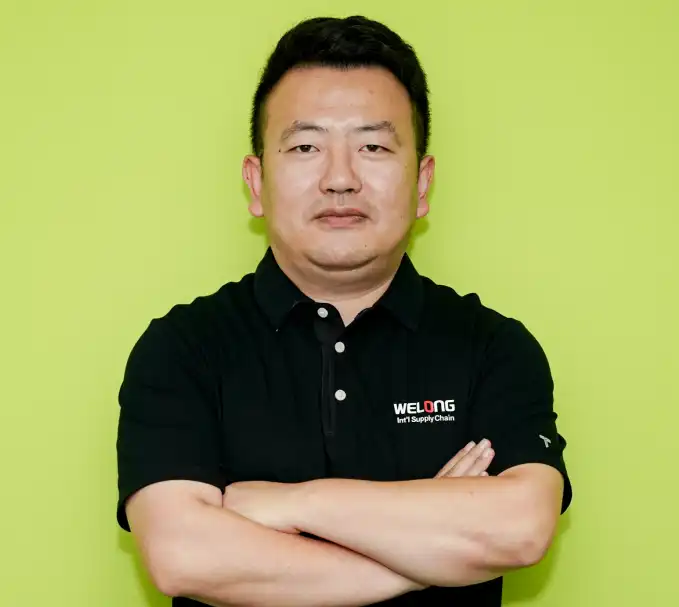
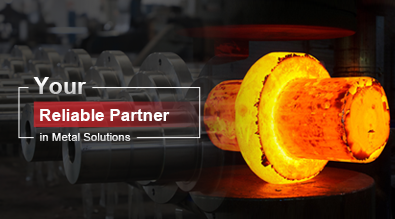
China WELONG-Your Reliable Partner in Metal Solutions