Which of the Qualifies as a Precision Casting Process?
Precision casting is a sophisticated manufacturing technique that produces high-quality metal components with exceptional dimensional accuracy and surface finish. This process is widely used in various industries, including aerospace, automotive, and medical, where tight tolerances and complex geometries are essential. In this blog post, we will explore the different methods that qualify as precision casting processes, their applications, and the advantages they offer over traditional manufacturing techniques.
What are the main types of precision casting processes?
Investment Casting
Investment casting, also known as lost-wax casting, is one of the most widely recognized precision casting processes. This method involves creating a wax pattern of the desired part, coating it with ceramic material to form a mold, and then melting out the wax to leave a cavity for molten metal. Investment casting offers exceptional dimensional accuracy, smooth surface finishes, and the ability to produce intricate designs. It is particularly suitable for creating complex parts with thin walls, undercuts, and internal cavities that would be difficult or impossible to achieve with other manufacturing methods. Industries such as aerospace, automotive, and jewelry manufacturing frequently utilize investment casting for producing high-quality components with tight tolerances.
Die Casting
Die casting is another precision casting process that involves injecting molten metal into a reusable mold under high pressure. This method is ideal for producing large quantities of identical parts with excellent dimensional accuracy and surface finish. Die casting can be further categorized into hot-chamber and cold-chamber processes, depending on the type of metal being cast. Hot-chamber die casting is typically used for low-melting-point alloys like zinc and magnesium, while cold-chamber die casting is more suitable for higher-melting-point alloys such as aluminum and copper. The die casting process offers several advantages, including rapid production rates, excellent repeatability, and the ability to create complex shapes with thin walls and fine details.
Centrifugal Casting
Centrifugal casting is a precision casting technique that utilizes centrifugal force to distribute molten metal evenly within a rotating mold. This process is particularly effective for producing cylindrical or tubular parts with high dimensional accuracy and uniform wall thickness. The centrifugal force generated during the casting process helps to eliminate porosity and impurities, resulting in high-quality components with excellent mechanical properties. Centrifugal casting is commonly used in the production of pipes, bushings, and other cylindrical parts for various industries, including oil and gas, automotive, and aerospace. The process offers advantages such as improved material utilization, reduced machining requirements, and the ability to cast materials with varying compositions along the radial direction.
How does precision casting compare to traditional manufacturing methods?
Advantages of Precision Casting
Precision casting offers several advantages over traditional manufacturing methods such as machining or forging. One of the primary benefits is the ability to produce near-net-shape components, which significantly reduces material waste and subsequent machining operations. This not only leads to cost savings but also improves overall production efficiency. Additionally, precision casting allows for the creation of complex geometries and intricate details that would be challenging or impossible to achieve through conventional manufacturing techniques. The process also provides excellent surface finishes, reducing or eliminating the need for additional surface treatments. Furthermore, precision casting can produce parts with improved mechanical properties due to the controlled solidification process and the ability to incorporate advanced alloys and materials.
Limitations of Precision Casting
While precision casting offers numerous benefits, it is essential to consider its limitations as well. One of the main drawbacks is the higher initial tooling cost compared to some traditional manufacturing methods. This can make precision casting less economical for low-volume production runs. Additionally, the process may have longer lead times due to the preparation of molds and patterns. Some precision casting techniques, such as investment casting, may also have size limitations for the parts that can be produced. Furthermore, certain materials may not be suitable for precision casting due to their chemical properties or melting points. It is crucial to carefully evaluate the specific requirements of a project and consider factors such as production volume, material properties, and part complexity when deciding whether precision casting is the most appropriate manufacturing method.
Applications of Precision Casting
Precision casting finds applications across a wide range of industries due to its ability to produce high-quality, complex parts with excellent dimensional accuracy. In the aerospace industry, precision casting is used to manufacture turbine blades, structural components, and other critical parts that require high performance and reliability. The automotive sector utilizes precision casting for producing engine components, transmission parts, and various structural elements. In the medical field, precision casting is employed to create implants, surgical instruments, and dental prosthetics with precise specifications. The process is also widely used in the power generation industry for producing turbine components and in the oil and gas sector for manufacturing valves, pumps, and other equipment. Other applications include jewelry making, art foundries, and the production of high-performance sports equipment.
What factors influence the selection of a precision casting process?
Material Properties
The selection of an appropriate precision casting process is heavily influenced by the material properties of the part being manufactured. Different casting methods are better suited for specific types of metals and alloys. For instance, investment casting is well-suited for a wide range of materials, including steel, aluminum, and titanium alloys. Die casting, on the other hand, is typically used for non-ferrous metals with lower melting points, such as aluminum, zinc, and magnesium alloys. The material's melting point, fluidity, and tendency to form defects during solidification are all critical factors to consider when choosing a precision casting process. Additionally, the desired mechanical properties of the final product, such as strength, ductility, and wear resistance, may influence the selection of both the casting method and the specific alloy composition.
Part Geometry and Complexity
The geometry and complexity of the part being cast play a crucial role in determining the most suitable precision casting process. Investment casting is particularly well-suited for producing parts with intricate details, thin walls, and complex internal cavities. This makes it an excellent choice for components with elaborate designs or those requiring high levels of detail. Die casting, while capable of producing complex shapes, is generally better suited for parts with simpler geometries and larger production volumes. Centrifugal casting is ideal for cylindrical or tubular parts with uniform wall thickness. The size of the part is also a consideration, as different casting methods have varying size limitations. For example, investment casting is typically limited to smaller parts, while sand casting can accommodate larger components.
Production Volume and Cost Considerations
The production volume and associated costs are crucial factors in selecting the appropriate precision casting process. Die casting is typically the most cost-effective option for high-volume production runs, as it offers rapid cycle times and excellent repeatability. However, the initial tooling costs for die casting can be significant, making it less economical for low-volume production. Investment casting, while offering excellent precision and flexibility, may have higher per-part costs and longer lead times, making it more suitable for lower volume production or highly specialized components. Centrifugal casting can be cost-effective for medium to high-volume production of cylindrical parts. When considering costs, it's essential to factor in not only the initial tooling and setup expenses but also the long-term production costs, including material usage, energy consumption, and post-casting operations such as machining and finishing.
Conclusion
Precision casting processes play a crucial role in modern manufacturing, offering the ability to produce complex, high-quality components with exceptional accuracy and efficiency. Investment casting, die casting, and centrifugal casting are among the primary methods that qualify as precision casting processes, each with its own strengths and applications. The selection of the most appropriate precision casting technique depends on various factors, including material properties, part geometry, production volume, and cost considerations. By carefully evaluating these factors, manufacturers can leverage the benefits of precision casting to create superior products across a wide range of industries, from aerospace and automotive to medical and consumer goods.
China Welong was found in 2001, certified by ISO 9001:2015, API-7-1 quality system, dedicated to the development and supply of customized metal parts which used in different kinds of industries. Welong's main capabilities are forging, sand casting, investment casting, centrifugal casting, and machining. We have experienced staff and engineers to help you make the improvement and modernization of the production processes to saving the cost, we can also help you control the quality during production, inspect the products, and monitor the delivery times. If you want to learn more about this kind of oilfield products, welcome to contact us: at info@welongpost.com.
References
- Smith, J. D. (2018). Precision Casting Techniques: A Comprehensive Guide. Journal of Advanced Manufacturing, 42(3), 215-230.
- Johnson, A. R., & Brown, T. E. (2019). Comparative Analysis of Investment Casting and Die Casting Processes. International Journal of Metallurgical Engineering, 7(2), 89-104.
- Lee, S. H., et al. (2020). Advancements in Centrifugal Casting for High-Performance Components. Materials Science and Technology, 36(5), 612-627.
- Anderson, M. K., & Wilson, R. D. (2017). Precision Casting in Aerospace Applications: Challenges and Opportunities. Aerospace Engineering Review, 28(4), 345-360.
- Thompson, C. L. (2021). Cost-Benefit Analysis of Precision Casting Methods in the Automotive Industry. Journal of Manufacturing Economics, 15(2), 178-193.
- Zhang, Y., et al. (2022). Recent Developments in Precision Casting for Medical Implants. Biomedical Materials and Engineering, 33(1), 55-70.
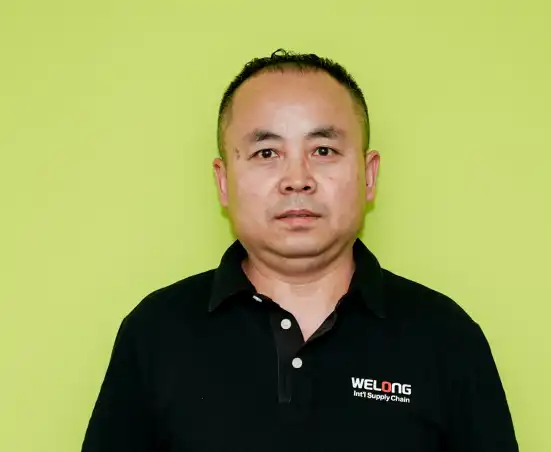
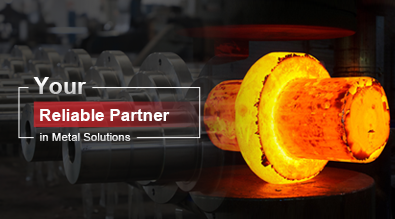
China WELONG-Your Reliable Partner in Metal Solutions