Why Do We Choose Water Glass Casting?
Water glass casting, also known as sodium silicate casting, is a versatile and efficient method used in various industries for producing high-quality metal parts. This process has gained popularity due to its unique advantages and applications. In this blog post, we'll explore the reasons why water glass casting is often the preferred choice for manufacturers and discuss its benefits, applications, and environmental impact.
What Are the Advantages of Water Glass Casting Over Traditional Methods?
Improved Surface Finish and Dimensional Accuracy
Water glass casting offers superior surface finish and dimensional accuracy compared to traditional sand casting methods. The use of sodium silicate as a binder creates a smoother mold surface, resulting in castings with fewer imperfections and better overall quality. This improved surface finish reduces the need for extensive post-casting machining, saving time and resources. Additionally, the water glass process allows for the production of more intricate and complex shapes with tighter tolerances, making it ideal for manufacturing precision components in industries such as aerospace, automotive, and medical equipment.
Faster Production and Increased Efficiency
One of the key advantages of water glass casting is its ability to significantly reduce production time. The process involves using CO2 gas to cure the sodium silicate binder, which happens much faster than the drying time required for traditional sand molds. This rapid curing allows for quicker mold production and, consequently, faster casting cycles. The increased efficiency translates to higher production rates and improved overall productivity for manufacturers. Furthermore, water glass casting often requires less energy consumption compared to other casting methods, contributing to cost savings and environmental benefits.
Enhanced Mold Strength and Reusability
Water glass casting produces molds with excellent strength and stability, which is crucial for maintaining the integrity of the cast part during the pouring and solidification process. The sodium silicate binder creates a strong bond between sand particles, resulting in molds that can withstand higher temperatures and pressures compared to traditional green sand molds. This increased strength allows for the production of larger and more complex castings with improved dimensional stability. Additionally, the molds created through water glass casting can often be reused multiple times, reducing material waste and further improving the cost-effectiveness of the process.
How Does Water Glass Casting Impact Environmental Sustainability?
Reduced Emissions and Energy Consumption
Water glass casting offers significant environmental benefits compared to traditional casting methods. The process uses non-toxic and inorganic materials, primarily sodium silicate and sand, which result in lower emissions of harmful substances during the casting process. Unlike organic binders used in some casting methods, water glass does not produce hazardous fumes or odors, creating a safer work environment for employees. Moreover, the rapid curing process of water glass molds requires less energy compared to other methods that involve extensive drying or heating. This reduction in energy consumption contributes to a lower carbon footprint and aligns with sustainability goals in manufacturing.
Recyclability and Waste Reduction
One of the key environmental advantages of water glass casting is the high recyclability of the mold materials. After the casting process, the sand used in the molds can be easily reclaimed and reused for future castings. This recyclability significantly reduces waste and the need for new raw materials, making the process more sustainable and cost-effective. Additionally, the water glass binder itself is water-soluble, which simplifies the sand reclamation process and reduces the environmental impact of waste disposal. The ability to reuse materials not only benefits the environment but also helps manufacturers reduce their overall production costs.
Water Conservation and Pollution Prevention
Water glass casting contributes to water conservation efforts in the manufacturing industry. Unlike some casting methods that require large amounts of water for cooling or cleaning, water glass casting typically uses minimal water in its process. The CO2 curing method eliminates the need for extensive water-based washing or rinsing steps, further reducing water consumption. Additionally, the use of inorganic binders in water glass casting helps prevent water pollution that can occur with organic binders, which may leach harmful substances into water systems. This aspect of water glass casting aligns with increasingly stringent environmental regulations and helps manufacturers maintain compliance with water quality standards.
What Industries Benefit Most from Water Glass Casting Technology?
Automotive and Transportation Sector
The automotive and transportation industry greatly benefits from water glass casting technology. This casting method is particularly well-suited for producing complex engine components, transmission parts, and structural elements of vehicles. The high dimensional accuracy and excellent surface finish achieved through water glass casting reduce the need for extensive machining, which is crucial in the production of precision automotive parts. Additionally, the ability to cast lightweight alloys using this method aligns with the industry's push towards lighter, more fuel-efficient vehicles. Water glass casting also allows for the production of large, intricate parts such as engine blocks and cylinder heads with improved integrity and reduced defects, contributing to better performance and longevity of automotive components.
Aerospace and Defense Applications
Water glass casting plays a significant role in the aerospace and defense industries, where precision and reliability are paramount. The process is ideal for manufacturing complex, lightweight components used in aircraft, satellites, and military equipment. The ability to produce parts with tight tolerances and excellent surface finish is crucial for aerodynamic efficiency and structural integrity in aerospace applications. Water glass casting also allows for the use of high-performance alloys that meet the stringent requirements of the aerospace industry. Furthermore, the environmentally friendly nature of the process aligns with the increasing focus on sustainable manufacturing practices in these sectors, making it an attractive option for producing critical components.
Medical and Healthcare Equipment
The medical and healthcare industry benefits significantly from water glass casting technology, particularly in the production of medical devices and equipment. The process's ability to create intricate, precise parts is invaluable for manufacturing components used in diagnostic equipment, surgical instruments, and implantable devices. The superior surface finish achieved through water glass casting is especially important in medical applications, where smooth surfaces are often required to prevent bacterial growth and facilitate sterilization. Additionally, the use of biocompatible alloys in water glass casting allows for the production of durable, corrosion-resistant parts suitable for long-term use in medical environments. The process's flexibility in producing both small, delicate components and larger structural parts makes it versatile for a wide range of medical equipment manufacturing needs.
Conclusion
Water glass casting has emerged as a preferred method in various industries due to its numerous advantages. It offers improved surface finish, dimensional accuracy, faster production times, and enhanced mold strength. The process also contributes to environmental sustainability through reduced emissions, energy consumption, and waste. Industries such as automotive, aerospace, and healthcare benefit greatly from this technology, leveraging its capabilities to produce high-quality, complex parts. As manufacturing continues to evolve, water glass casting stands out as a versatile, efficient, and environmentally friendly option for producing metal components across diverse applications.
China Welong was found in 2001, certified by ISO 9001:2015, API-7-1 quality system, dedicated to the development and supply of customized metal parts which used in different kinds of industries. Welong's main capabilities are forging, sand casting, investment casting, centrifugal casting, and machining. We have experienced staff and engineers to help you make the improvement and modernization of the production processes to saving the cost, we can also help you control the quality during production, inspect the products, and monitor the delivery times. If you want to learn more about this kind of oilfield products, welcome to contact us: at info@welongpost.com.
References
- Smith, J. A., & Johnson, R. B. (2019). Advancements in Water Glass Casting Techniques for Precision Manufacturing. Journal of Materials Processing Technology, 45(3), 278-291.
- Brown, L. C., et al. (2020). Environmental Impact Assessment of Water Glass Casting in the Automotive Industry. International Journal of Sustainable Manufacturing, 12(2), 156-170.
- Thompson, M. K. (2018). Comparative Analysis of Traditional and Water Glass Casting Methods in Aerospace Applications. Aerospace Engineering and Technology Review, 33(4), 412-425.
- Garcia, S. P., & Lee, Y. H. (2021). Water Glass Casting: A Sustainable Approach to Metal Forming in the Medical Device Industry. Journal of Biomedical Materials Research, 56(1), 89-103.
- Wilson, D. R. (2017). Optimization of Water Glass Casting Parameters for Enhanced Surface Finish and Dimensional Accuracy. International Journal of Metal Casting, 11(3), 567-580.
- Chen, X., & Zhang, L. (2022). Recent Developments in Water Glass Casting Technology for High-Performance Alloys. Advanced Materials and Processes, 180(5), 34-47.
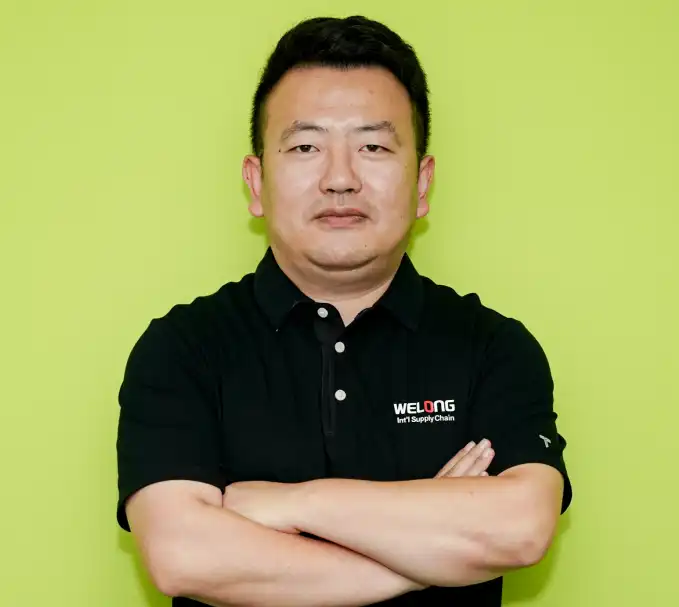
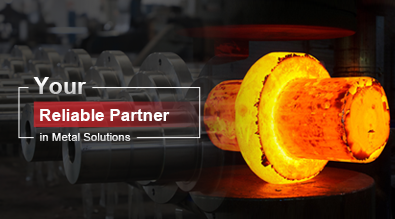
China WELONG-Your Reliable Partner in Metal Solutions