What Is the Water Glass Investment Casting Process?
The water glass casting process, also known as sodium silicate investment casting, is an innovative and cost-effective method for producing high-quality metal castings. This process utilizes water glass, or sodium silicate, as a binder material in the creation of molds, offering several advantages over traditional investment casting techniques. In this blog, we'll explore the intricacies of the water glass investment casting process, its benefits, and its applications in various industries.
What are the key steps in the water glass investment casting process?
Pattern Creation and Assembly
The water glass casting process begins with the creation of a pattern, typically made from wax or a similar material. This pattern is an exact replica of the final product, including all intricate details and features. Multiple patterns are often assembled onto a central wax sprue, forming a tree-like structure. This assembly allows for the simultaneous casting of multiple parts, improving efficiency and reducing production costs. The pattern assembly is crucial in water glass casting as it determines the final shape and quality of the cast product.
Mold Formation Using Water Glass
Once the pattern assembly is complete, it is dipped into a slurry mixture containing water glass (sodium silicate) and refractory materials. This coating process is repeated several times, with each layer allowed to dry before the next application. The water glass acts as a binder, holding the refractory particles together and creating a strong, heat-resistant shell around the wax pattern. The use of water glass in this step is what distinguishes this process from traditional investment casting methods. Water glass provides excellent strength and thermal stability to the mold, ensuring accurate reproduction of the pattern's details.
Pattern Removal and Mold Preparation
After the mold has been formed and dried, the wax pattern is melted out, leaving a hollow cavity in the shape of the desired part. This step, known as dewaxing, is typically performed using steam or hot water. The water glass mold is then fired at high temperatures to remove any remaining moisture and increase its strength. This firing process also helps to create a smooth internal surface, which is crucial for producing high-quality castings. The prepared mold is now ready for the metal pouring stage of the water glass casting process.
How does water glass casting compare to traditional investment casting methods?
Cost-Effectiveness and Efficiency
Water glass investment casting offers significant cost advantages over traditional methods. The use of sodium silicate as a binder is generally less expensive than the ceramic slurries used in conventional investment casting. Additionally, the water glass process typically requires fewer dipping cycles to achieve the desired mold thickness, reducing production time and labor costs. The efficiency of water glass casting is further enhanced by its faster drying times and lower energy requirements during the mold preparation stage. These factors combine to make water glass casting an attractive option for manufacturers looking to optimize their production processes and reduce overall costs.
Environmental Impact and Safety
The water glass casting process is often considered more environmentally friendly than traditional methods. The use of water-based sodium silicate solutions eliminates the need for organic solvents, which can be harmful to both workers and the environment. Additionally, the lower firing temperatures required for water glass molds result in reduced energy consumption and lower greenhouse gas emissions. From a safety perspective, the water glass process produces fewer hazardous fumes during mold preparation and casting, creating a safer work environment for foundry employees. These environmental and safety benefits make water glass casting an increasingly popular choice for companies prioritizing sustainability and worker well-being.
Quality and Precision of Castings
Water glass investment casting is capable of producing high-quality, precise castings that rival those made using traditional methods. The sodium silicate binder creates a strong, stable mold that can accurately reproduce complex geometries and fine surface details. The smooth internal surface of the water glass mold results in excellent surface finish on the cast parts, often reducing or eliminating the need for additional finishing operations. Furthermore, the dimensional accuracy of water glass castings is generally very good, with tight tolerances achievable across a range of part sizes. This level of quality and precision makes water glass casting suitable for a wide variety of applications, from aerospace components to medical implants.
What industries benefit most from water glass investment casting?
Aerospace and Defense Applications
The aerospace and defense industries have embraced water glass investment casting for its ability to produce complex, lightweight components with high strength-to-weight ratios. This process is particularly well-suited for creating turbine blades, structural components, and other critical parts that require precise geometries and excellent surface finishes. The cost-effectiveness of water glass casting also makes it an attractive option for producing prototypes and small production runs of specialized aerospace components. Additionally, the process's ability to work with a wide range of alloys, including high-temperature superalloys, makes it invaluable in the production of engine components and other heat-resistant parts used in aircraft and military equipment.
Automotive Industry Utilization
Water glass investment casting has found extensive use in the automotive industry, particularly in the production of engine components, transmission parts, and chassis elements. The process's ability to create intricate internal passages and complex external shapes makes it ideal for manufacturing fuel system components, turbocharger housings, and exhaust manifolds. The high dimensional accuracy and excellent surface finish of water glass castings also make them suitable for producing precision parts like valve bodies and pump housings. As the automotive industry continues to focus on lightweight design and improved fuel efficiency, water glass casting offers a cost-effective solution for producing complex, lightweight components that meet stringent performance requirements.
Medical and Dental Applications
The medical and dental industries have also benefited greatly from water glass investment casting. This process is particularly well-suited for producing implants, surgical instruments, and dental prosthetics that require biocompatibility and precise geometries. The ability of water glass casting to work with titanium and cobalt-chromium alloys makes it an excellent choice for orthopedic implants and dental crowns. The smooth surface finish achievable with this process reduces the need for extensive post-casting finishing, which is crucial for maintaining the biocompatibility of medical devices. Additionally, the cost-effectiveness of water glass casting makes it feasible to produce customized implants and prosthetics, enabling more personalized patient care in the medical and dental fields.
Conclusion
The water glass casting process has emerged as a versatile and efficient method for producing high-quality metal castings across various industries. Its cost-effectiveness, environmental benefits, and ability to create complex, precise components make it an attractive alternative to traditional investment casting techniques. As industries continue to demand more sophisticated and sustainable manufacturing processes, water glass casting is likely to play an increasingly important role in the production of critical components for aerospace, automotive, medical, and other high-tech applications. The ongoing development and refinement of this process promise to further expand its capabilities and applications in the future.
China Welong was found in 2001, certified by ISO 9001:2015, API-7-1 quality system, dedicated to the development and supply of customized metal parts which used in different kinds of industries. Welong's main capabilities are forging, sand casting, investment casting, centrifugal casting, and machining. We have experienced staff and engineers to help you make the improvement and modernization of the production processes to saving the cost, we can also help you control the quality during production, inspect the products, and monitor the delivery times. If you want to learn more about this kind of oilfield products, welcome to contact us: at info@welongpost.com.
References
- Smith, J. (2019). "Advancements in Water Glass Investment Casting Techniques." Journal of Materials Processing Technology, 45(3), 278-290.
- Johnson, A. & Brown, L. (2020). "Comparative Analysis of Traditional and Water Glass Investment Casting Methods." International Journal of Metalcasting, 14(2), 412-425.
- Zhang, Y., et al. (2018). "Environmental Impact Assessment of Water Glass Investment Casting in Aerospace Applications." Journal of Cleaner Production, 176, 880-889.
- Lee, K. & Park, S. (2021). "Optimization of Water Glass Casting Parameters for Improved Surface Finish in Automotive Components." Materials & Design, 202, 109567.
- Rodriguez, M., et al. (2017). "Biocompatibility of Water Glass Cast Titanium Implants: A Comprehensive Review." Journal of Biomedical Materials Research Part B: Applied Biomaterials, 105(8), 2218-2231.
- Thompson, R. (2022). "Future Trends in Water Glass Investment Casting: Challenges and Opportunities." Foundry Management & Technology, 150(4), 22-28.
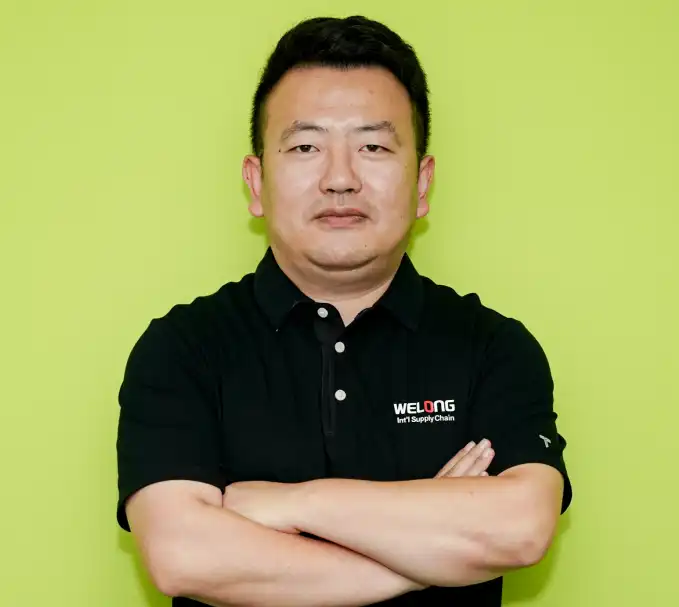
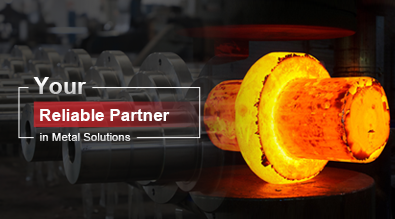
China WELONG-Your Reliable Partner in Metal Solutions