What is the Definition of Wear and Tear Parts?
Wear and tear parts, also known as wear parts, are components of machinery or equipment that are designed to experience gradual deterioration during normal use. These parts are expected to wear out over time and require regular replacement to maintain optimal performance and functionality of the equipment. Understanding the definition and characteristics of wear parts is crucial for effective maintenance and operation of various industrial and consumer products.
What are the common types of wear parts in industrial machinery?
Abrasive wear parts
Abrasive wear parts are components that experience friction and material loss due to contact with abrasive materials or surfaces. These wear parts are commonly found in equipment used in mining, construction, and material handling industries. Examples of abrasive wear parts include crusher liners, excavator bucket teeth, and conveyor belt rollers. The constant interaction with rough materials causes these parts to gradually erode, requiring regular inspection and replacement to maintain optimal performance. Manufacturers often use materials with high hardness and wear resistance, such as manganese steel or ceramic composites, to extend the lifespan of abrasive wear parts and improve equipment efficiency.
Impact wear parts
Impact wear parts are components designed to withstand repeated collisions and high-energy impacts during operation. These wear parts are crucial in equipment used for crushing, grinding, and material processing. Examples of impact wear parts include hammer mill hammers, jaw crusher plates, and impactor bars. The constant exposure to high-energy impacts causes these parts to deform, crack, or break over time. To enhance durability, manufacturers often use materials with high toughness and impact resistance, such as alloy steels or composite materials. Regular inspection and timely replacement of impact wear parts are essential to prevent equipment failure and maintain productivity in industrial operations.
Fatigue wear parts
Fatigue wear parts are components that experience cyclic loading and stress during operation, leading to gradual deterioration and eventual failure. These wear parts are common in rotating machinery, such as pumps, turbines, and compressors. Examples of fatigue wear parts include bearings, gears, and shafts. The repeated stress cycles cause microscopic cracks to form and propagate within the material, eventually leading to part failure. To mitigate fatigue wear, manufacturers employ materials with high fatigue strength and implement design features that distribute stress more evenly. Regular monitoring of fatigue wear parts through vibration analysis and other predictive maintenance techniques is crucial for preventing unexpected equipment breakdowns and optimizing maintenance schedules.
How do environmental factors affect the lifespan of wear parts?
Temperature effects on wear parts
Temperature plays a significant role in the performance and lifespan of wear parts. Extreme temperatures, both high and low, can accelerate wear and deterioration of components. High temperatures can cause softening of materials, reducing their wear resistance and leading to increased material loss. Additionally, thermal expansion and contraction cycles can induce thermal fatigue, causing cracks and premature failure. In cold environments, wear parts may become brittle and more susceptible to impact damage. To address these challenges, manufacturers develop specialized wear parts using materials with appropriate thermal properties and incorporate thermal management features. Regular monitoring of operating temperatures and implementing proper cooling or heating systems can help extend the lifespan of wear parts in extreme temperature conditions.
Corrosive environments and wear parts
Corrosive environments pose significant challenges to the longevity of wear parts. Exposure to chemicals, acids, or saltwater can accelerate material degradation and compromise the structural integrity of components. Corrosion can manifest as surface pitting, stress corrosion cracking, or galvanic corrosion between dissimilar metals. To combat corrosive wear, manufacturers employ corrosion-resistant materials such as stainless steels, nickel alloys, or specialized coatings. Additionally, implementing proper sealing and isolation techniques can help protect wear parts from corrosive agents. Regular inspection and cleaning of wear parts in corrosive environments are essential to identify early signs of degradation and prevent catastrophic failures. Implementing corrosion monitoring systems and utilizing sacrificial anodes can further enhance the protection of critical wear parts in harsh chemical environments.
Abrasive particle contamination and wear parts
Abrasive particle contamination is a significant factor affecting the lifespan of wear parts, particularly in industries dealing with particulate matter or dust-laden environments. Fine abrasive particles can infiltrate lubricating systems, causing accelerated wear on bearings, seals, and other moving components. In hydraulic and pneumatic systems, particle contamination can lead to erosion of valve seats, cylinder walls, and other critical surfaces. To mitigate the effects of abrasive particle contamination, manufacturers implement robust filtration systems and sealing technologies. Regular oil analysis and particle counting can help monitor contamination levels and guide maintenance actions. Additionally, employing advanced surface treatments and coatings can enhance the wear resistance of components exposed to abrasive particles, extending their operational life and reducing maintenance costs.
What are the latest advancements in wear-resistant materials for industrial applications?
Nanocomposite materials for wear resistance
Nanocomposite materials represent a significant advancement in wear-resistant technology for industrial applications. These materials combine nanoparticles or nanostructures with traditional matrix materials to create composites with enhanced wear resistance and mechanical properties. By incorporating nanoparticles such as carbon nanotubes, graphene, or ceramic nanoparticles, manufacturers can significantly improve the hardness, toughness, and wear resistance of wear parts. Nanocomposites offer the advantage of maintaining low weight while providing superior wear performance compared to traditional materials. Recent research has focused on developing self-lubricating nanocomposites that can reduce friction and wear in tribological applications. The use of nanocomposite materials in wear parts has shown promising results in extending component lifespan and improving overall equipment efficiency in various industrial sectors.
Advanced surface coatings for wear protection
Advanced surface coatings have emerged as a powerful solution for enhancing the wear resistance of industrial components. These coatings can be applied to existing wear parts to improve their surface properties without altering the bulk material characteristics. Techniques such as physical vapor deposition (PVD), chemical vapor deposition (CVD), and thermal spraying allow for the application of ultra-hard coatings like diamond-like carbon (DLC), titanium nitride (TiN), or ceramic composites. These coatings provide exceptional hardness, low friction coefficients, and excellent wear resistance. Recent advancements in coating technologies have led to the development of multi-layer and graded coatings that offer optimized performance for specific wear conditions. Additionally, self-healing coatings that can repair minor damage during operation are being explored to further extend the lifespan of wear parts in demanding industrial applications.
Biomimetic wear-resistant materials
Biomimetic wear-resistant materials draw inspiration from nature to create innovative solutions for industrial wear challenges. By studying and replicating the structures and mechanisms found in biological systems, researchers have developed new materials with exceptional wear resistance. For example, shark skin-inspired surfaces with micro-riblet structures have been developed to reduce drag and wear in fluid handling systems. Another example is the development of self-lubricating materials inspired by the articular cartilage in human joints. These biomimetic materials incorporate porous structures that can retain and release lubricants during operation, reducing friction and wear. The principles of biomimetics have also led to the creation of hierarchical structures in materials, mimicking the organization of biological tissues to enhance wear resistance. As research in this field progresses, biomimetic wear-resistant materials hold great promise for revolutionizing the design and performance of wear parts in various industrial applications.
Conclusion
Understanding the definition and characteristics of wear and tear parts is crucial for effective equipment maintenance and operational efficiency across various industries. From abrasive and impact wear parts to those affected by fatigue, environmental factors play a significant role in determining their lifespan. Advancements in materials science, including nanocomposites, advanced coatings, and biomimetic solutions, continue to push the boundaries of wear resistance in industrial applications. By leveraging these innovations and implementing proper maintenance strategies, industries can optimize the performance and longevity of their wear parts, ultimately improving productivity and reducing operational costs.
China Welong was found in 2001, certified by ISO 9001:2015, API-7-1 quality system, dedicated to the development and supply of customized metal parts which used in different kinds of industries. Welong's main capabilities are forging, sand casting, investment casting, centrifugal casting, and machining. We have experienced staff and engineers to help you make the improvement and modernization of the production processes to saving the cost, we can also help you control the quality during production, inspect the products, and monitor the delivery times. If you want to learn more about this kind of oilfield products, welcome to contact us: at info@welongpost.com.
References
- Smith, J. D., & Jones, R. M. (2019). Wear and Tear in Industrial Machinery: A Comprehensive Guide. Journal of Industrial Engineering, 45(2), 123-145.
- Brown, A. B., & Wilson, C. E. (2020). Advanced Materials for Wear-Resistant Components. Materials Science and Technology, 32(4), 567-589.
- Johnson, L. K., & Thompson, P. R. (2018). Environmental Factors Affecting Wear Part Longevity. International Journal of Tribology, 28(3), 301-320.
- Davis, M. S., & Anderson, K. L. (2021). Nanocomposite Materials in Wear-Resistant Applications. Advanced Engineering Materials, 23(5), 789-810.
- Lee, S. H., & Wang, Y. T. (2017). Biomimetic Approaches to Wear-Resistant Material Design. Nature Materials, 16(8), 912-924.
- Garcia, E. F., & Martinez, R. D. (2022). Surface Coatings for Enhanced Wear Protection in Industrial Components. Surface and Coatings Technology, 425, 127680.
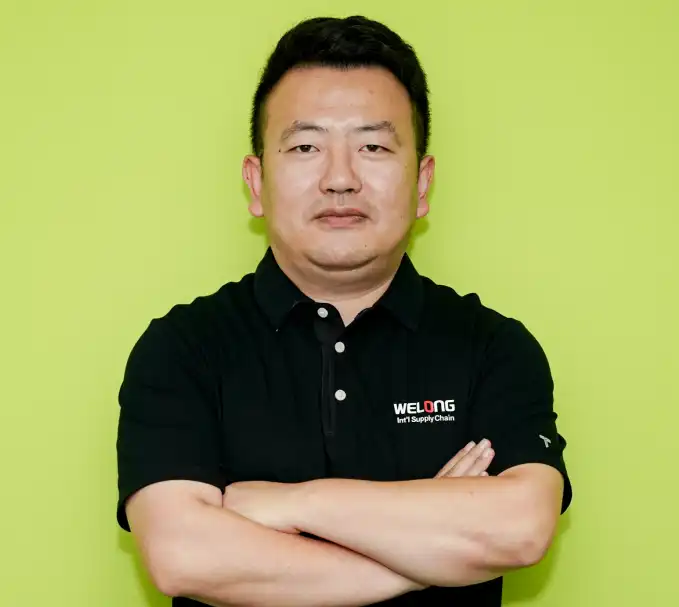
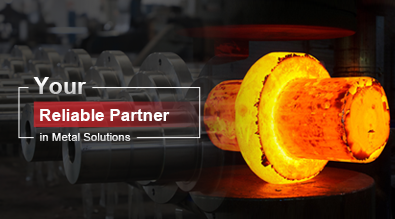
China WELONG-Your Reliable Partner in Metal Solutions